1. Main characteristics of cement
The cement industry brings together a plurality of economic players. It is one of the most widely used building materials in the world.
There are several types of cement and various ingredients: Portland cement, clinker cement, pozzolanic cement, granulated slag, fly ash, calcined shale, silica fume, etc. Depending on the type of need, (high resistance to sulphates, rapid fixation, low heat of hydration, etc.) the type of cement used will not be the same.
For example, the kind of cement that gets used in the manufacture of concrete is a hydraulic binder. It results from an endothermic reaction between clay (20%) and limestone (80%) which, mixed with water, makes it possible to agglomerate aggregates and clay together.
To make cement, materials like rock, limestone and clay must first be turned into a powder. Then, the mixture will be heated to a very high temperature (1450°) in order to obtain the clinker, the main constituent of the cement, which will be ground to obtain the final form of the cement. Several mixtures are possible depending on the use of the cement.
To assemble blocks, it will be necessary to make a mortar with sand. For a slab, it will take concrete which is composed only of cement powder and water.
The cement powder takes on the appearance of a gray, free-flowing powder. The cement can also take the form of granules or grains depending on the degree of fineness resulting from the grinding phase of the component.
2. Main industrial applications of cement
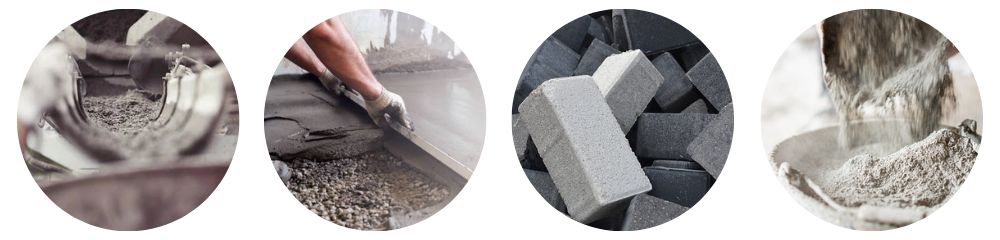
Cement is used in building construction and public works.
It is used to bind elements such as bricks or concrete blocks in order to make the foundations of construction projects.
3. Industrial handling of cement
After the quarry extraction stage, the cementitious limestone is crushed to obtain blocks with a maximum size of 80 mm. The various additives are then blended together according to the desired chemical composition. These raw materials are then dried and ground very finely to obtain a powder with a texture similar to flour. This mixture is then pre-heated before being introduced into a very high temperature oven (1450°). Upon exiting the kiln, the clinker passes through a cooling system before being stored in silos or hoppers. Then comes the grinding step with the possible introduction of other additives, depending on the desired finished quality. The production is then shipped in bulk or packaged in paper bags.
Grinding, storage, conveying, packaging, these are the main cement/clinker handling steps.
Cement, a hygrometric powder, must absolutely be stored in a dry place protected from bad weather and humidity.
4. Cement applications with Palamatic Process equipment
To respond to the problems of the industry, the Palamatic design office has developed dedicated equipment for handling cement.
Conveying
Palamatic Process offers a dense phase pneumatic transfer system, Cementveyor, specially designed for the transport of cement and other building materials over long distances. Cementveyor allows for reduced energy consumption and a healthy, dust-free working environment due to the complete sealing technology. Palamatic also has a pneumatic conveyor dedicated to the transfer of fly ash, MultiAshFlow®, at high temperature while avoiding any emission of dust and risk of leakage.
Grinding
The Palamatic pin mill provides high speed impact milling to obtain a finer micronized powder.
Storage
Storage silos (flexible, rigid) or stainless-steel containers allow the storage of cement in large quantities and in complete safety.
Packaging and unpacking
Cement can be packed or unpacked using bulk bag filling stations and bulk bag emptying stations adapted: dust containment, sealing, station mobility, automation, etc.
5. Palamatic Process customer applications with cement
Palamatic Process has been supporting manufacturers dealing with cement powder in their production process for more than 30 years. Several efficient installations have been installed with our customers:
• Installation for the automatic opening and emptying of 25kg bags at high speed with minimum operator intervention for supplying a pneumatic transfer system downstream.
• Discharge of big bags of cement for truck loading
• Supply of a plasterboard manufacturing process
• Mobile FlowMatic® 07 bulk bag filling system allowing connection instead of a truck tank, under a truck loading spout.
• Plasterboard manufacturing process with grinding of raw materials to standardize the production process.