1. Presenting the solutions: impact, crushing, attrition, percussion, abrasion, wear and shear
![]() |
![]() |
![]() |
Grinding by impact of the particle on the tool |
Grinding by moving of the tool on the particle |
Impact grinding between particles |
![]() |
![]() |
![]() |
Crushing with the tool |
Crushing by attrition with the tool | Shear milling with the tool |
The action of fragmentation causes particle size reduction of solid materials to achieve various objectives including: improvement of storage conditions, transport, mixing, etc.
Examples of installations:
- Grinding process line for production and packaging of icing sugar.
- Our turnkey solution PalSugarIce®: grinding unit for the manufacture of icing sugar.
Grinders are generally classified according to the size of the particles they process:
- Crushers to obtain large fragments
- Grinders for powder production
- Sprayers or micronizers for the preparation of very fine powders
- Disintegrators for breaking up fibrous materials.
2. The different types of fragmentation
Particle size reduction can be achieved through different types of fragmentation:
- Cutting: reduction of very large blocks of material from quarries or mines into pieces with dimensions greater than 100 mm
- Crushing: reduction to sizes ranging from 25 to 100 mm
- Granulation: reduction to sizes from 6.3 to 25 mm
- Grinding: reduction to sizes between 0.4 and 6.3 mm
- Spraying: production of particles smaller than 0.4 mm
- Micronization: reduction to the size of microns
- Defibration: fragmentation of fibrous materials
- Shredding: reduction by chopping flexible materials
- Cutting: sawing or shearing to obtain regular splinters
Some names of machines involved in the industrial fragmentation process:
Jaw crushers, gyratory crushers, roller crushers, roller mills, wheel mills, disc mills, rotary impact mills (hammer mills, pin mills), Bar mills, ball mills, jet mills, super mills, micronizers...
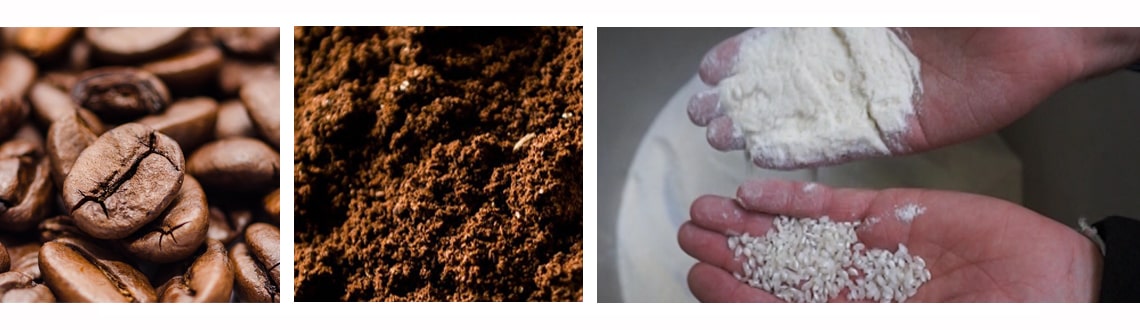
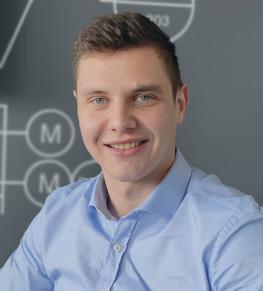
You have a project? I am available to advise you
and accompany you in your study.
Loïc, expert in powders
3. Definition of the main terms related to grinding process
- Reduction rate: this is the difference between the average dimensions of the particles before and after the fragmentation operation. The reduction rate varies from about 5 to 100.
- Hardness: it is defined in comparison to another material. A solid is harder than another if it scratches it and is not scratched by it. The commonly used hardness scale is the MOHS scale (examples: gypsum 2, fluorite 4, talc 1, diamond 10).
- Friability: it is represented by the ease with which a substance is broken by percussion. For example, coal and diamond are friable substances, plastics are not. Friability is not related to hardness.
- Moisture Content: A generally acceptable moisture content is 1-4%. Beyond that, there is a risk of formation of a pasty material.
- Dry or wet process: the wet process is used when the product is in a wet state or if it will be used wet. The dry process is preferred if the product is to be dried subsequently, and also to avoid agglomeration of the material.
- Energy consumption: The energy consumption during the grinding process is high and increases with the desired fineness. In dry grinding, the additional energy consumption can be up to 30%, but the advantage of wet grinding is lost if the product has to be dried or deagglomerated later in the process.