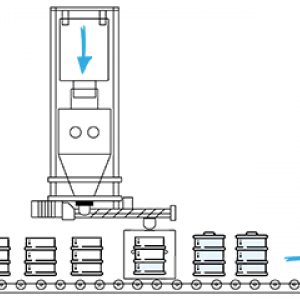
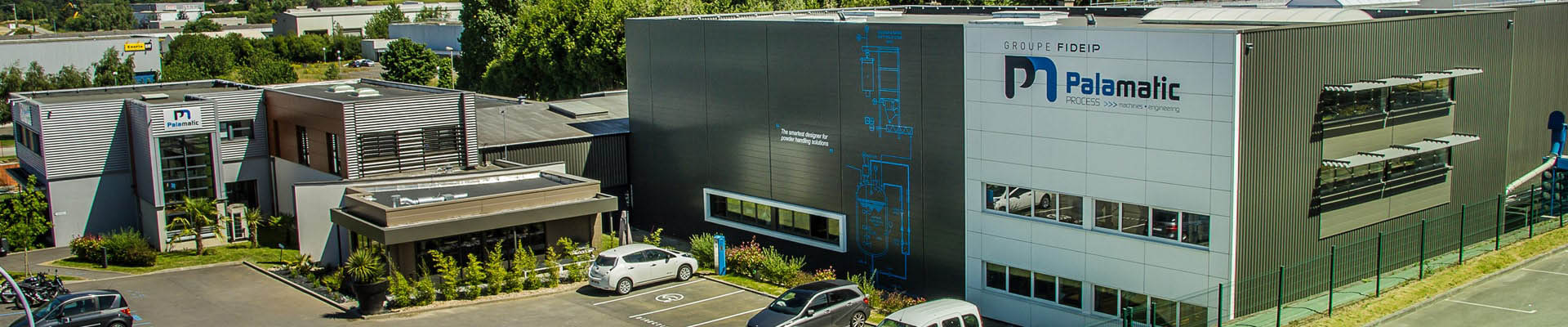
The manufacture of baby food must guarantee a precise and regular dosage of the raw ingredients in order to ensure food safety and quality of the production batches.
Throughout the manufacturing process, batch controls are performed. The manufacturing process is almost completely in a closed circuit, which strongly limits any risk of contamination.
Here are the different stages of the infant formula transformation process:
- reception of the cow's milk at the factory
- sanitary and traceability controls are carried out
- skimming: the fat is removed from the milk
- pasteurization
- addition of ingredients: proteins, lactose, milk derivatives, fats, fibres, whey, lactose, minerals...
- evaporation to remove water and start the process of transformation into milk powder.
- drying to obtain milk powder and then dry addition of new ingredients such as iron, vitamins, probiotics...
- packaging of milk powder in cans
The baby food industry is not only about milk powder. It also concerns fruit or vegetable purees with or without small pieces and ready-to-drink milk for infants.