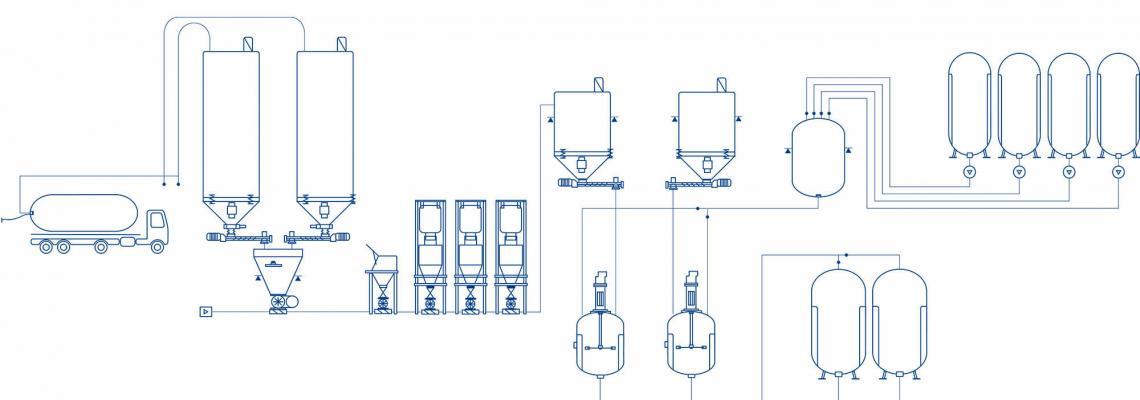
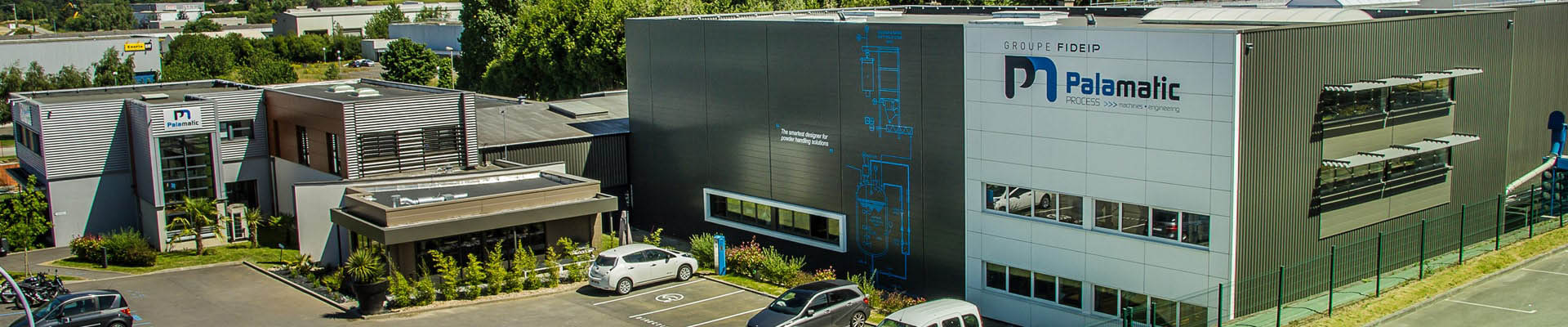
Storage, conveying, dosing of raw materials for the feeding of mashers/dispersers, precision of dosages with repeatability of recipes and containment for the handling of powders and raw products.
Main powders handled: titanium dioxide of titanium (titanium, TiO2), calcium carbonate, (CaCo3), talc, silica, silica, silica, aerosil, barium sulphate, pigment...
Powders handled: lithium, NMC compounds (Nickel, Manganese, Cobalt), and anode/cathode materials (graphite, LiFePO4), which require secure handling due to their toxicity, hygroscopic nature, and...
The systems include the installation of silos for the storage of materials (carbonate, titanium, talc...) initially stored in bulk trucks. Weighing hoppers (dosing hoppers) installed on scales, ensure the weighing of batches of raw materials to be loaded into the mashers/dispersers. Loading is generally carried out by pneumatic conveying (or conveying screws) with a throughput of up to 10t./h.-15t./h. and an associated accuracy of -/+ 2kg. The automation of the loading processes offers an optimal containment unlike manual loading of the dispersers. Depending on the production tonnages, the production lines integrate several dispersers whose powder feeding is centralized on the silos and intermediate storage.