Powders handled: lithium, NMC compounds (Nickel, Manganese, Cobalt), and anode/cathode materials (graphite, LiFePO4), which require secure handling due to their toxicity, hygroscopic nature, and reactivity.
OEB4/OEB5 Confinement Solution, Automated Discharge Systems, and Optimized Flow Management
The battery industry imposes strict standards for handling sensitive powders such as lithium and NMC compounds due to their toxic and hygroscopic properties. Palamatic Process has risen to the challenge by developing a custom solution that combines OEB4/OEB5 confinement, automated discharge systems, and optimized flow management. Learn how this innovative installation meets safety, productivity, and traceability requirements by drawing from the best practices in the pharmaceutical industry.
Client Objective
Our client, a major player in engineered materials, sought to optimize their sensitive powder processing and handling. Faced with stringent industrial constraints, their primary goal was to ensure a high level of operator safety while enabling efficient and confined material handling that complies with strict exposure and cleanliness standards.
The client aimed to reduce production downtime caused by manual handling and enhance overall process efficiency to sustain an industrial-scale production rate. Key objectives included:
- Controlling operator exposure to OEB4 and OEB5-classified substances.
- Ensuring optimal containment throughout the processing.
- Managing fine and compacted powders efficiently while maintaining constant productivity.
- Providing an automated interface for real-time traceability and supervision of operations.
The Proposed Solution
To meet the client’s specific needs, Palamatic Process designed and implemented a comprehensive, customized solution centered around the IBC Flow OEB, incorporating advanced industrial equipment. This installation leverages a combination of technical innovations to optimize the handling of sensitive powders while ensuring secure working conditions.
Key Features of the Solution
Confined and Automated Discharge Stations with IBC Flow OEB (OEB4 and OEB5)
The IBC Flow OEB is specifically designed to eliminate exposure risks and cross-contamination.
Advanced Containment Technology
- The system uses double-sealed valves where the docking between the IBC and process structure creates a unique airtight seal.
- This setup eliminates any possibility of powder leakage during discharge, even with highly volatile or toxic materials.
Enhanced Safety
- Operators are fully protected from exposure thanks to the automated system that eliminates the need for direct intervention.
- Ergonomic and secure design minimizes risks associated with manual handling.
Advanced Dust Collection Systems
- Systems capture airborne particles with a capacity of 1,500 m³/h, reducing inhalation risks through advanced filtration.
Butterfly and Guillotine Valves
- Stainless steel valves ensure precise and leak-proof powder flow management.
Custom IBCs
- Antistatic, corrosion-resistant containers designed to match powder density and required containment levels.
Automation and Centralized Supervision
- A digital interface manages critical parameters such as flow rate, pressure, and production cadence in real-time.
- Integrated traceability meets industrial and regulatory requirements.
Waste Compactors
- Hermetic compactors efficiently reduce the volume of bags and other residues for hygienic disposal.
Industrial Equipment Comprising the Installation
Meticulously selected and adapted equipment meets the strict requirements of sensitive powders, combining containment, flexibility, robustness, and ease of maintenance. These solutions incorporate proven technologies and innovations tailored to OEB4 and OEB5-classified materials, ensuring optimal performance in demanding industrial environments.
IBC Flow OEB Discharge Stations: Airtight and Highly Functional Design
Main Functionality
- Ensures rapid, controlled, and confined discharge of big bags, even for fine and compacted powders.
Specific Features
- Airtight containment sleeves prevent dust emissions.
- Integrated pneumatic massage system to fluidize powders prone to clumping.
- Ergonomic structure with adjustable settings for various big bag sizes.
Advantages of the IBC Flow OEB
- Reduction of manual handling, enhancing operator safety.
- Smooth and continuous discharge, ensuring consistent production rates.
- Easy cleaning and maintenance, minimizing production downtime.
Butterfly and Guillotine Valves: Precision and Durability
Main Functionality
- These valves provide precise and secure regulation of powder flows, whether for transfers, dosing, or interruptions.
Specific Features
- Constructed from 316L stainless steel, offering increased resistance to corrosive and abrasive materials.
- Maximum sealing, preventing material leakage or cross-contamination.
- Automatic actuation integrated with the Pal’Touch automation system for real-time control.
Advantages of Butterfly and Guillotine Valves
- Reduction of material losses through precise flow control.
- Enhanced operator safety by limiting direct exposure to powders.
- Increased durability thanks to a robust design suited for demanding industrial environments.
Lump Breakers and Pneumatic Vibrators: Ensuring Powder Fluidity and Uniformity
Main Functionality
- These systems break down compacted or agglomerated powders, ensuring uniform particle size before transfer or packaging.
Specific Features
- Rotary knife mechanisms effectively break down lumps.
- Integrated pneumatic vibrators facilitate powder flow through hoppers and transport systems.
- Modular design allows for customized installation based on specific constraints.
Advantages of Lump Breakers and Pneumatic Vibrators
- Prevention of blockages in transfer systems, reducing interruptions.
- Improved powder quality through complete homogenization.
- Adaptability to various material types, including abrasive and hygroscopic powders.
Tubular Conveyors: Complete Containment and Efficiency
Main Functionality
- These conveyors ensure continuous and fully enclosed transfer of sensitive powders, avoiding any contact with the external environment.
Specific Features
- High-quality materials (316L stainless steel) and electropolished finishes to minimize adhesion and simplify cleaning.
- Airtight connections between equipment to prevent losses or contamination.
- Hygienic design suitable for pharmaceutical and sensitive industrial environments.
Advantages of Tubular Conveyors
- Preservation of material quality throughout the process.
- Reduced changeover times with rapid cleaning solutions.
- Versatility to handle materials with varied characteristics.
Explore our wide range of conveyors for powder and granule transfer.
Dust Collection Systems: Optimal Safety and Cleanliness
Main Functionality
- These systems efficiently eliminate airborne particles, ensuring a clean atmosphere that complies with safety standards.
Specific Features
- High-performance HEPA or ULPA filters capturing ultrafine particles (up to 0.3 µm).
- Extraction capacity of 1,500 m³/h, suitable for environments with high dust concentrations.
- Direct connection to discharge stations, hoppers, and conveyors for comprehensive coverage.
Advantages of Dust Collection Systems
- Protection of operators from inhaling harmful particles.
- Reduction of dust deposits on equipment, minimizing maintenance requirements.
- Compliance with strict industrial and environmental regulations.
Discover our industrial dust collection solutions.
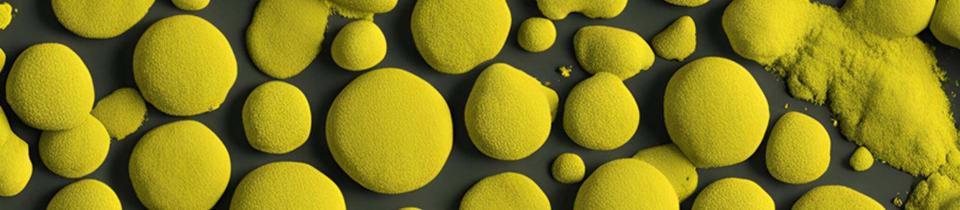
Summary
This combination of equipment ensures optimal management of sensitive powders, from discharge to transfer and packaging. The installation combines advanced technical performance with ergonomic and secure solutions, perfectly meeting the specific requirements of the battery powder and pharmaceutical industries.
Results and Benefits Achieved
Maximum Safety: Optimal Powder Containment
Handling OEB4 and OEB5-classified powders requires equipment that ensures strict containment, eliminating any risk of operator exposure and environmental contamination.
Advanced Containment
- IBC Flow EOB discharge stations are equipped with hermetic sleeves and glovebox systems, enabling fully isolated material handling.
Operator Protection
- Connected dust collection systems capture airborne particles at the source, reducing inhalation risks.
Compliance with Strict Standards
- The equipment is designed to meet industrial and pharmaceutical standards, adhering to OEB4 and OEB5 classifications for safety and containment.
Positive Impact
These systems enhance workplace health and safety while reducing potential material losses caused by leaks or accidental dispersions.
Increased Productivity: Reduced Interruptions
A key project priority was to enhance operational flow, minimizing downtime and slowdowns caused by blockages or complex handling.
Compacted Powder Management
- The integration of lump breakers and vibrating hoppers ensures continuous material flow, even for agglomerated or hygroscopic powders.
Automated Flow Management
- Butterfly and guillotine valves controlled by the Pal’Touch® system enable precise transfers without manual intervention, reducing human errors.
Quick Cleaning
- The equipment is designed for easy and rapid cleaning, minimizing downtime between batches or production campaigns.
Direct Results
- Thanks to these innovations, the client maintained high production rates, increasing overall productivity and operational efficiency.
Operational Flexibility: Integration of New Batches or Lines
Equipment adaptability is essential to meet evolving industry needs, particularly in advanced materials or pharmaceutical sectors.
Modular Design
- IBC containers, automated valves, and tubular conveyors can be quickly adjusted or replaced to accommodate different powder types or new requirements.
Scalable Installations
- The system allows for the addition of new lines or simultaneous management of multiple batches thanks to a modular architecture.
Integrated Traceability
Client Benefits
- This flexibility ensures the ability to meet new market demands without requiring major modifications to existing installations.
Cost Reduction: Limited Downtime and Optimized Flows
Optimizing industrial processes involves reducing operational costs by limiting interruptions and maximizing resource efficiency.
Simplified Maintenance
- Robust equipment designed for easy access requires less time and fewer resources for maintenance.
Reduced Material Loss
- Leak-proof systems and precise transfer mechanisms minimize losses due to leaks or human errors.
Energy Optimization
- High-efficiency tubular conveyors and dust collection systems reduce energy consumption while maintaining high performance.
Return on Investment
- Cost savings from improved flow, material, and human resource management enable a rapid return on investment.
Global Summary of Benefits
- Optimal safety for operators and the environment.
- Increased productivity through seamless and automated flow management.
- Industrial flexibility to adapt to changing market demands.
- Significant cost reduction, enhancing operational profitability.
These advantages make this solution a model of efficiency and adaptability for industries handling sensitive and demanding powders.
Conclusion
The IBC Flow OEB embodies Palamatic Process’s expertise in designing advanced equipment for handling sensitive powders. By combining automated, confined discharge with exceptional dosing precision, this solution ensures operator safety, material quality, and optimal industrial efficiency.
With the IBC Flow OEB, the client now has a reliable and high-performing tool that meets the strictest OEB containment and powder flow management standards. By integrating this equipment into a complete process line, large-scale production can be achieved while adhering to safety and quality norms.
This solution is also applicable for handling pharmaceutical powders.
Integration of IBC Flow OEB into a Complete Process Line
The IBC Flow OEB can be used independently or in combination with other Palamatic Process equipment to create a fully confined and automated process line.
Complementary Equipment:
- Flowmatic OEB: Big bag filling and discharge station.
- PalSack OEB: Confined sack discharge.
- PalDrum OEB: Confined drum discharge.
- Cyclone OEB: Powder filtration for efficient fine particle management.
Advantages of a Complete Line:
- Secure raw material deconditioning.
- Automated and controlled powder transfer between production stages.
- Strict compliance with OEB containment standards and industrial requirements.
Explore More About Sensitive Powders in Industry
European Powder Metallurgy Association (EPMA)