Atomization tower outlet packaging line
The DairyBagging® packaging line is designed for packaging products leaving the atomization tower for continuous powder production.
The packaging of dried powder is conducted with strong hygienic requirements imposed by the Dairy sector. The complete handling line integrates pneumatic transfer, vibrating screen, a storage buffer hopper and a bulk bag filling station.
- Line hygiene
- Integrated CIP cleaning
- Operator ergonomics
- Continuous transfer out of tower
Models
DairyBagging® 500 | DairyBagging® 1 000 | DairyBagging® 1 500 | DairyBagging® 2 000 | |
---|---|---|---|---|
Tower output flow rate | 500 kg/h | 1,000 kg/h | 1,500 kg/h | 2,000 kg/h |
Buffer hopper capacity | - | 500 | 1,000 | 1,000 |
Sieve model | 450 | 600 | 900 | 900 |
Diameter mm transfer piping | sms 51 | sms 63 | sms 76 | sms 88.9 |
Conditioning after atomization tower
The packaging of your product after the atomization tower is a key step in respecting the integrity of the produced material. Preventing material attrition, hygienic design or even homogenization of the production batch are the main functions that the DairyBagging® line incorporates.
Respect for the product
Preventing particle attrition of the material requires the use of a pneumatic transfer at slow conveying speeds. The main technology used is vacuum and dense phase conveying. The large radii of the elbows in the transfer piping ensure conveying continuity via a constant laminar regime of the transfer air.
Product qualification
At the outlet of the atomization tower and the fluidized bed, powder agglomerates (scrapings) can be released and sent to the packaging line. The DairyBagging® line, from Palamatic Process, integrates a completely sealed vibrating screen installed in line on the pneumatic transfer system. The powder agglomerates are sieved and purged intermittently when the reject valve is opened.
Bulk bag packaging
At the end of the DairyBagging® line, a bulk bag filler ensures a dust tight connection of the bulk bag to the product reception cyclo filter. Weigh cells integrated into the conditioning station are used to control the filling. When changing the FIBC, the accumulation of powder produced continuously by the atomization tower is stored in the cyclofilter, or an intermediate buffer hopper, depending on the options selected.
In certain applications, Palamatic can double the bulk bag filling station via a by-pass transfer of bag A or bag B. This alternative has the advantage of not requiring a buffer hopper and offering the operator less down time in the bulk bag filling production.
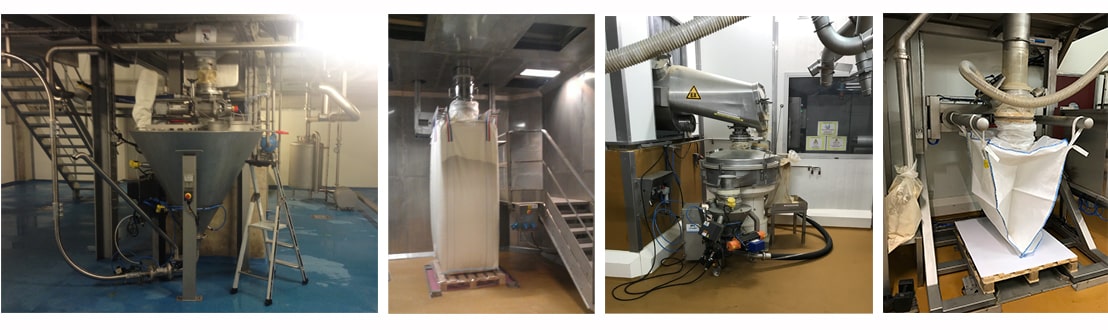
Homogenization of the production batch?
Some atomization processes require homogenization of the powder or the ingredient produced. In this application operating in "batch", a mixer is integrated on the transfer line. Mixer technology is typically a conical screw mixer compatible for frequent cleaning and hygienically design.
Need to lower the temperature of the atomized product?
At the end of the atomization tower, behind the separator cyclones, the packaging of the powder can still be problematic due to the higher temperature of the material. Some dairy products require controlled packaging temperatures to prevent future clogging issues. The DairyBagging® line offers an option by adding a thermal cooler directly integrated into the pneumatic transfer line.
Contact our experts to define the technologies specific to your application.
Clean In Place
All the equipment offered on the DairyBagging® packaging line is compatible with in-line cleaning using integrated nozzles and connection to your CIP network.
The Palamatic powder handling line is dedicated to manufacturers looking for the best current technologies to meet the specific constraints of your business. Contact our powder handling experts to design your production line.
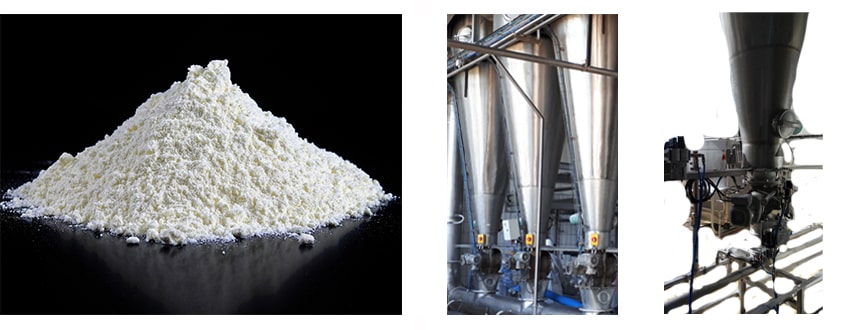
Discover the facilities of our customers who use the DairyBaggingline ® for the packaging of products out of the atomization tower.
All the equipment integrated into the process line for packaging products at the atomization tower outlet are available below.