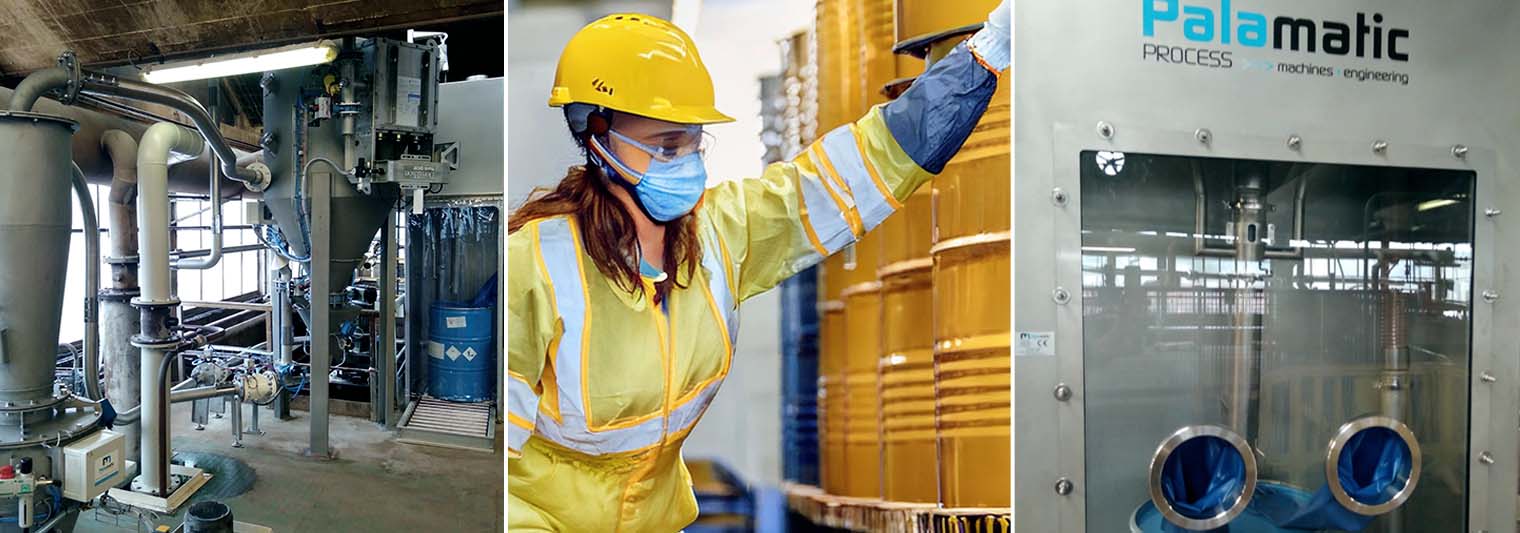
Containment of critical and toxic commodity powders (CRM) is essential to ensure worker safety and minimize environmental impact. Given the high risks associated with handling these substances, advanced containment technologies have been developed to isolate, filter and control the flow of these powders. These solutions ensure compliance with strict health, safety and environmental protection standards while ensuring efficient, high-quality production.
1. Containment fundamentals
The fundamental principles of Critical Raw Materials (CRM) powder containment are essential to ensure worker safety, environmental protection and product quality.
Physical isolation of hazardous substances
Physical isolation involves separating CRM powders from the outside environment and from workers, using containment equipment such as glove boxes, sealed enclosures or pneumatic transfer systems. This separation reduces worker exposure to hazardous substances and prevents contamination of the environment.
Air flow and pressure control
Air flow and pressure control are essential to maintain physical isolation and prevent CRM powders from dispersing into the environment. This can be achieved by using ventilation systems, dust extractors or differential pressure control equipment. The aim is to create a slight vacuum inside the containment equipment, so that contaminated air cannot escape to the outside.
Filtration and purification of contaminated air
Contaminated air filtration and purification is required to remove CRM powder particles from the air before it is released into the environment. This can be achieved by using high-efficiency filters, such as HEPA or ULPA filters, or air treatment systems, such as activated carbon filtration units or thermal oxidizers. These devices reduce emissions of CRM powders into the environment and comply with air quality regulations.
Safe management of waste and residues
Safe management of CRM powder waste and residues is essential to prevent environmental contamination and ensure traceability of materials. This may include temporary storage of waste in leak-proof containers, treatment of waste to reduce its toxicity or reactivity, and disposal of waste in accordance with applicable regulations. Proper waste management minimizes risks to human health and the environment, and promotes a circular economy.
The fundamental principles of CRM powder containment aim to ensure worker safety, environmental protection and product quality by isolating hazardous substances, controlling air flows and pressures, filtering and purifying contaminated air, and safely managing waste and residues.
2. Primary and secondary containment systems
When it comes to containing CRM powders and toxic substances, there are generally two levels of containment: primary and secondary.
Primary containment
Primary containment refers to equipment and devices that are in direct contact with CRM powders. This equipment is designed to contain hazardous substances and prevent their dispersion into the working environment. Examples of primary containment equipment include reactors, mixers, pneumatic transfer systems, glove boxes and sealed enclosures. Such equipment is usually fitted with filtration and differential pressure control devices to ensure optimum isolation of CRM powders.
Secondary containment
Secondary containment encompasses the overall working environment in which primary containment equipment is installed and operated. The aim is to create an additional barrier to prevent the dispersion of CRM powders in the event of primary containment failure, or during maintenance and cleaning operations. Examples of secondary containment measures include clean rooms, controlled atmosphere zones, ventilation systems and personal protective equipment (PPE) for workers. Secondary containment aims to ensure worker safety, environmental protection and product quality by controlling air flows, pressures and contamination levels throughout the working environment.
Primary and secondary containment are two complementary levels of protection designed to ensure worker safety, environmental protection and product quality when handling CRM powders. Primary containment concerns equipment in direct contact with the powders, while secondary containment encompasses the overall working environment.
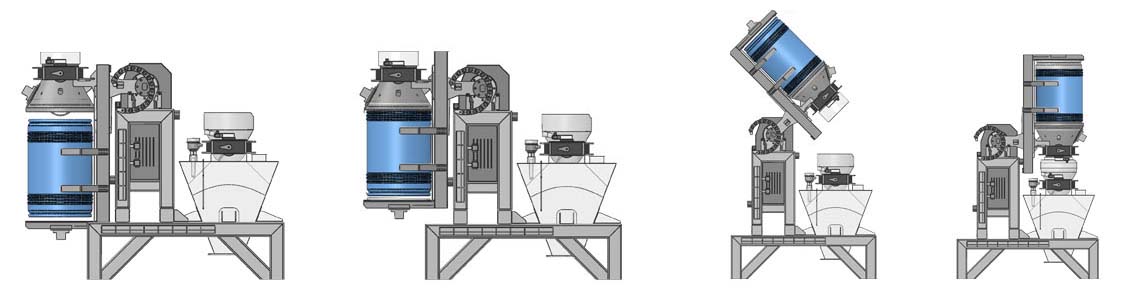
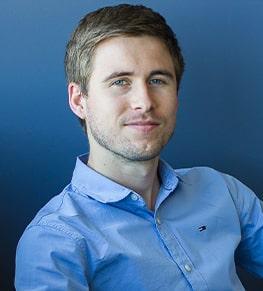
Do you have a project? I am available to advise you and support you in your study.
Guillaume, CRM powder and toxic substances expert.
3. Recent technological innovations
Indeed, the field of containment has seen a number of recent innovations aimed at improving the safety, efficiency and quality of production processes involving hazardous or sensitive substances.
High-efficiency pneumatic transfer systems
These systems transfer powders faster and more efficiently, reducing product loss and energy consumption. They can also be fitted with automatic cleaning devices to prevent blockages and ensure continuous operation.
Advanced gloveboxes with precise atmospheric control
This equipment provides a confined, controlled working environment for operators, maintaining precise levels of humidity, temperature and oxygen or nitrogen concentration. They can be used for handling environmentally sensitive substances or for applications requiring increased protection against contamination.
Nanometric filtration technologies
These technologies filter out fine and ultra-fine particles with high efficiency, using state-of-the-art membranes or filtering materials. They can be integrated into containment equipment to reduce dust emissions and protect operators and the environment.
Automated cleaning-in-place (CIP) systems
These systems enable automated cleaning and disinfection of containment equipment, without dismantling or manual intervention. They reduce downtime, improve cleaning quality and repeatability, and minimize the risk of cross-contamination.
Real-time sensors and monitoring systems
These technologies enable continuous monitoring of critical production process parameters, such as dust concentration, temperature, humidity or pressure. They can be used to detect anomalies, prevent failures and optimize the performance of containment equipment.
These recent innovations in the field of containment help to improve the safety, efficiency and quality of production processes involving hazardous or sensitive substances, while meeting the evolving needs of industries and complying with current regulations.
Case study: Contained discharge of drums