Handling and processing of rare earths: what industrial solutions for controlled production?
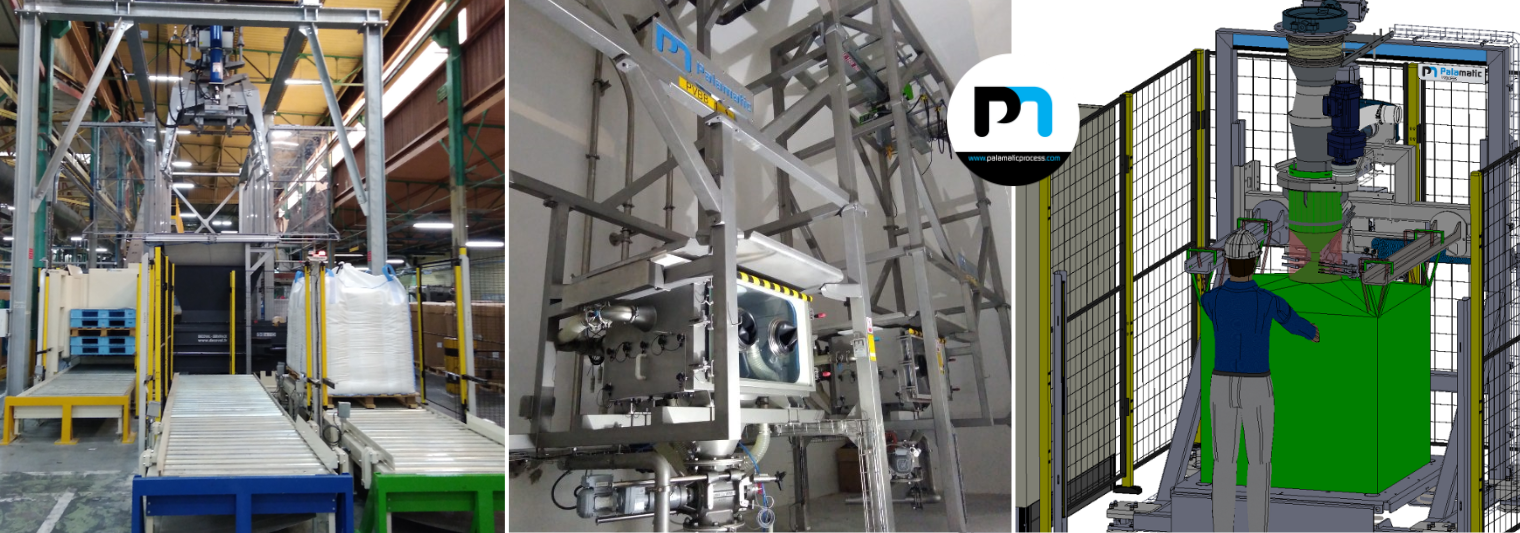
- 1. What technical constraints do rare earths pose in an industrial environment?
- 2. Drainage and transfer solutions for rare earths
- 3. Sieving, grinding and mixing: critical stages for rare earth powders
- 4. Dosing, weighing and packaging in sensitive environments
- 5. Containment, safety and traceability: at the heart of the sector's requirements
- 6. Conclusion
Rare earths, although inconspicuous to the general public, are omnipresent in modern technologies: permanent magnets, electric vehicle motors, batteries, wind turbines, electronic components, etc. These strategic materials are essential to the energy and digital transition.
However, their industrial processing poses many technical challenges: fine powders, hygroscopic, sometimes toxic or abrasive, requiring a high level of safety and precision.
Palamatic Process designs industrial equipment that allows rare earths to be handled, dosed, sieved, mixed and packaged under the best conditions.
This article will guide you through the specificities of these sensitive materials and the technical solutions for controlling their processing, from the big bag to the final product.
1. What technical constraints do rare earths pose in an industrial environment?
Fine, hygroscopic and abrasive powders: a real process challenge
Rare earths, often transformed into oxides or alloys, have complex characteristics: very fine grain size, hygroscopic behaviour, abrasiveness, tendency to agglomerate, etc. These properties complicate the transfer, dosing and sieving stages.
It is essential to use lines designed to guarantee smooth flow, dosing stability and protection against dust.
ATEX risks and personnel safety during handling
The dust generated can create explosive atmospheres in ATEX zones.
The equipment must be certified by and integrated into a confined process, with localised extraction, easy cleaning and explosion-proof systems.
Palamatic Process designs its machines to meet these requirements: leak-proof valves, de-bunging devices, secure transfer lines and specific filtration.
Some rare earths or their derivatives can be toxic or reactive.
It is therefore essential to ensure strict containment at each stage: emptying containers, sieving, dosing, mixing, filling.
Palamatic Process offers solutions with glove boxes, BFM® sleeves, containment chambers, inflatable seals or pressurisation for controlled atmospheres.
2. Discharge and transfer solutions for rare earths
Containment big bag and bag emptying stations (Sacktip®, FlowMatic®)
The Sacktip® SE and FlowMatic® stations enable the safe emptying of bags or big bags containing rare earths.
Equipped with integrated dust extraction, containment systems, bag compactors and watertight connections, they guarantee clean, compliant and ergonomic handling.
Pneumatic or mechanical transfer: how to choose the right technology?
Depending on the distance, the flow rate and the nature of the powders, the transfer can be:
- Mechanical: tubular screw or trough screw, suitable for abrasive products.
- Pneumatic: dense phase or vacuum, for confined environments.
Palamatic Process offers hybrid systems to adapt the technology to the customer's needs.
What is the use of nitrogen transfer in the handling of sensitive rare earths?
Some powders react to air or moisture. Nitrogen transfer protects the product from oxidation or degradation, while reducing the risk of explosion.
Palamatic offers sealed inerted loop lines with sensors and safety valves.
3. Sieving, grinding and mixing: critical steps for rare earth powders
Safety screening and quality control of metal powders
The vibrating screens make the line safe by eliminating foreign bodies, agglomerates and contaminants.
The EasyClean or containment models allow for quick cleaning and perfect sealing.
Grinding and deagglomeration: controlling the granulometry of the oxides
The double-shaft lump breakers (EC) and pin mills (UM) enable control of the particle size of the oxides without denaturing the material.
ATEX options or options with suction can be integrated.
Which mixing equipment should be chosen for rare earths?
Depending on the fineness of the mixture, the batch volume and the nature of the components:
- blade/blade mixer (MRS): fast, homogeneous.
- conical mixer: gentle, for sensitive formulations.
- vertical mixer: compact and hygienic.
All controlled by Pal'Touch® to guarantee traceability and reproducibility.
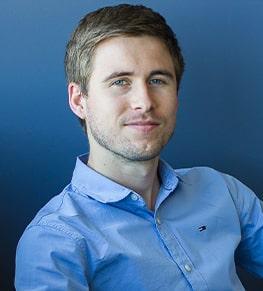
Looking for a safe and compliant solution for handling rare earth powders ?
I am available to support your project with tailored, regulation-ready systems.
Guillaume, expert in rare earth material handling and automated process lines
4. Dosing, weighing and packaging in sensitive environments
Screw or weight feeders for a precise and continuous process
Palamatic offers volumetric and weight feeders (loss in weight) for reliable dosing.
The screws are interchangeable depending on the behaviour of the powders. Automation via Pal'Touch® allows for precise and connected control.
Filling of big bags, drums and bags with reinforced containment
The FlowMatic® and PalSack® filling stations enable rare earths to be packaged in closed containers with maximum sealing.
Available options: vibrating table, integrated weighing, bag sealer, dust removal, traceability.
How can the traceability and compliance of rare earth batches be ensured?
Pal'Touch® manages recipes, process parameters and batch histories.
The addition of connected scales, printers or ERP interfaces guarantees regulatory compliance and end-to-end traceability.
5. Containment, safety and traceability: at the heart of the sector's requirements
ATEX equipment and confined processes for sensitive or toxic products
The integration of ATEX-certified equipment and containment systems is essential to secure the processes.
Palamatic Process masters the architecture of these complex lines, integrating each critical point: de-bunchers, watertight connections, gloves boxes, centralised extraction.
Automated line control (Pal'Touch®) to minimise human error
Pal'Touch® centralises line control, enables the automation of manufacturing sequences and ensures enhanced quality control.
It guarantees productivity, safety and product consistency.
Conclusion
Rare earths are key resources for the industries of the future.
Processing them requires perfect control of the stages of handling, dosing, mixing and packaging.
Palamatic Process offers tailor-made solutions to meet these challenges, with equipment designed for the most demanding environments: fine, toxic, abrasive, ATEX, confined or nitrogen-filled powders.
Thanks to its experience, its test centre and its personalised project approach, Palamatic Process supports manufacturers in the rare earths industry to secure their production, guarantee the quality of their products and strengthen their industrial sovereignty.
📞 Do you work in the processing or recovery of rare earths?
Contact our experts to design a customised, high-performance and secure production line together.