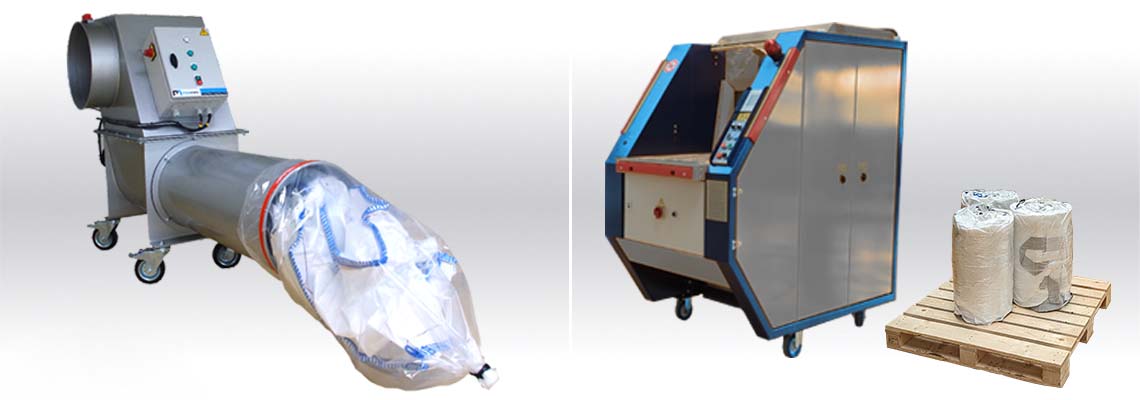
In industrial production lines, the use of sacks and big bags for packaging ingredients is very common.
Once emptied in the process, these containers must be “managed” in order to reduce storage space and maintain a clean workspace.
1. Main functions of an industrial compactor
Once emptied of their contents, big bags and smaller bags can take up a lot of space and generate dust in your work environment. Using an industrial FIBC compactor makes it possible to reduce the volume of container waste and guarantee a healthy working atmosphere.
Designed with a smaller footprint and mobility, Palamatic Process compaction equipment lowers production costs because operator intervention is considerably reduced.
Furthermore, thanks to a reduced volume of container waste, the expenses related to storage and transport are much lower.
Reducing the volume of this waste and containing it in a plastic bag improves hygienic conditions on production sites. The working environment is not contaminated by powder residues that could remain present in the big bags and sacks.
2. Comparative table of performance and design differences
Screw compactor | Roller compactor | ||
---|---|---|---|
Type of technology | Auger-type compactor | Band and roller compaction | |
Number of compacted big bag | 5 to 7 per meter of plastic sleeve | 4 to 6 per roll | |
Waste container dimension | Length | 1,000 mm | 600 mm |
Diameter | 700 mm | 400 mm | |
Modular | Yes, but fixed diameter | Yes, but fixed length | |
Big bag introduction | Hinged access door for full opening to bulk bag hopper |
Opening on the front face of the compactor |
|
Dust management at compactor inlet |
Partial |
Partial |
|
Full containment of compacted big bag |
Yes, in closed plastic bag |
Partially, lengthwise only |
|
Mobile design | Yes, on wheels or with forklift | Yes, on wheels | |
Integration into a big bag unloading station? | Yes | No | |
Control system | Integrated and embedded | Integrated and embedded | |
Power requirements | Electric, 600V | Electric, 600V |
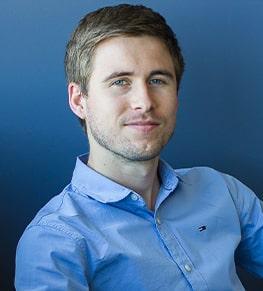
Looking for a big bag handling system? I am
available to advise you in your study.
Guillaume, powder expert
3. Advantages and disadvantages of screw and roller compactors
The advantage of a screw compactor is that it can be directly integrated into a big bag or bag dump station.
The dust-tight design of the plastic sleeve containing the compacted FIBCs is 100% guaranteed.
The volume compacted in the polyethylene sheath is a little greater for a screw compactor: 5 to 7 big bags against 4 to 6 for a roller compactor.
The roller compactor can be used to compact other containers other than big bags or sacks, such as: cardboard packaging, plastic films, etc. Unlike the screw compactor, the dust containment of the rollers is not guaranteed, therefore it is not suitable for packaging that has contained highly toxic products.
The initial volume to compacted volume compaction ratio is greater in the case of the roller compactor.
Contact our sales department to discover all our handling solutions for super sacks and big bags.