1. What is powder qualification?
The qualification of powders concerns all manufacturers producing and handling dry materials in the form of finished products or raw materials.
In many manufacturing processes involving the handling and production of powders and bulk solids, careful analysis of raw materials is an essential step for obtaining the desired end results.
Handling powders can be difficult, especially during processing and storage stages. Many factors influence the flow of powders such as: particle size, shape, chemical structure, temperature, electrostatic charge, surface morphology, gas absorption, atmospheric humidity and particle size distribution (otherwise known as "PSD"). However, the proper function of an industrial process depends mainly on the behavior of the powders, and in particular on its flow characteristics.
To be able to study the powder medium properly, it is necessary to know the characteristics of the particles, as well as the powder as a whole. The particles are generally not spherical but often come in various shapes.
To characterize the size and shape of non-spherical particles, two concepts are used:
- The equivalent diameter which corresponds to the diameter of a sphere which has the same characteristic as the particle.
- The sphericity factor (Ψv) which is the ratio between the surface of the sphere having the same volume as the particle, compared to the surface of the particle
In general, the size of the particles present in a powder is dispersed. The particle size analysis of the powder makes it possible to define average parameters representative of the entire particle size distribution.
Particle morphology: depending on the shape of the particles, they will have either good or poor flow properties. For particles with a shape that moves away from the sphere, that is to say for elongated shapes such as rods or needles, the flow will be poor.
The history of the powder (how it was handled, stored and transported) can have an impact on its flow characteristics. Depending on the way the powder was handled, it will be in a certain state of organization and will therefore present a certain cohesiveness (deaeration, particle size segmentation, moisture absorption, etc.).
2. Why carry out tests on your powders?
Our test laboratory allows us to perform flow analysis on your materials which can determine the performance of your powders. Along with this analysis, our test center contains many configurations of equipment that will help determine the final solution of your production process. These tests make it possible to define minimum flow diameters, angle of the silos/hoppers, surface condition, placement of flow aid, etc.
Examples of flow types:
A - Mass flow
All the material in the silo is moving, but not necessarily at the same speed.
• No dead zone
• Distribution of residence times (first in - first out), FIFO.
• Low segregation
• Lower storage capacity (high storage silo angle)
• Less abrasion resistance of storage equipment
B - Core flow
Movement of a central core only
• Presence of dead zone
• Distribution of residence times (first in - last out, no management of loading batches)
• Strong segregation
• Greater storage capacity (low angle of the storage silo)
• Storage equipment more resistant to abrasion
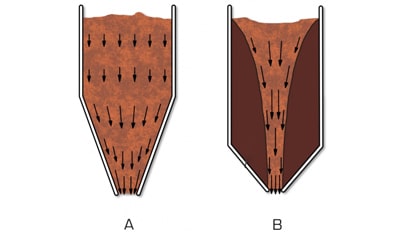
3. Our solutions to check the conformity of your powders
We are capable of measuring the flowability and grain size to verify the conformity of your powders.
Palamatic Process, with its expertise in the field of bulk solids and powders, supports manufacturers in the particle size characterization of the materials used in their production.
One example of our support is our laboratory equipment that can perform tests on your powders under real production conditions. Our laboratory performs several measurements on the powder samples in order to quantify, classify, control and compare the type of flow of the powders.
Examples of tests include: particle size, angle of repose, slope angle, measurement of packed and unpacked densities (Hausner index), powder dispersion measurement test, etc.
Methods for evaluating the flow characteristics of powders:
- Angle of repose
- Settlement tests: Hausner index, dynamic settlement tests, dynamic compression tests,
- Comparison of settlement tests
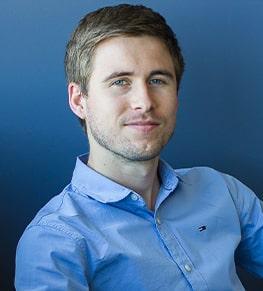
If your require further assistance,
I am at your entire disposal.
Guillaume, expert in powders
4. What equipment?
The overall behavior of a powder is determined by how the particles interact with each other, how the powder interacts with the environment (i.e., humidity) and finally the process in which it is handled. The nature as well as the importance of these interactions depend on many parameters, such as:
• Characteristics of the particle: morphology, size, particle size distribution, etc.
• The characteristics of the surrounding air: humidity, temperature, aeration rate.
• Characteristics of the handling process: surface state of the walls, handling of the powder, pressure.
If these parameters dominate the force of gravity the powder will exhibit a cohesive behavior and present irregular movement or none at all. To assess the materials flow, there are different methods.
1 - Rheometer to test the flow of powders
The powder flow device provides simple and fast analysis of flow behavior in industrial processing equipment. The rheometer makes it possible, for example, to evaluate the capacity of discharging powders placed in storage containers.
Several test choices can be pre-programmed: flow function, wall friction or bulk density.
Examples of output data:
- Clean index of powder flow
- Arches dimensions
- Rathole diameter
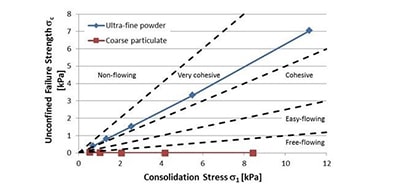
2 - Control sieves for particle size analysis
The Palamatic Process lab sieves make it possible to determine the distribution curve and particle size of the powder.
The Palamatic Process lab sieve produces a 3-dimensional sifting movement so that the results are quickly available and reproducible. The powder falls vertically and is distributed in a circular motion over the entire surface of the sieve. Our software enables computerized assessment of particle size analysis with quick and easy data reading.
5. Parameters to be taken into account
Other external parameters must be taken into account:
- Wall surface: in the same way that particles interact with each other, these particles can also interact with the walls of your storage vessel
- Humidity: the humidity of the environment can impact the flowability of a powder
- Temperature: the temperature impacts the flowability of a powder
Parameters governing the flow of powder contained in a silo:
• The nature and physical properties of the powder
• The half-opening angle of the silo
• The roughness of the wall
• Internal pressure in the silo
• The size of the discharge outlet
• Mass flow requires a low angle and smooth walls
• The transition between flow / non-flow conditions depends on the size of the opening.
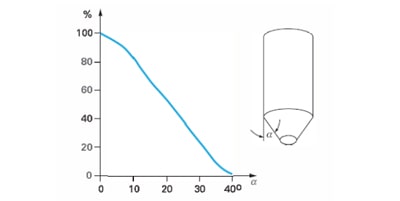
According to Ter Borg: probability of occurrence of mass flow as a function of the angle of the silo
Jenike's test, initially developed for sizing silos, quantifies the flow properties of a powder. This method consists in determining the tangential stress τR to be applied to an initially consolidated stack of powder, subjected to a normal stress σN, in order to “break” this stack. The torque (σN, τR) is called the breaking point.
The determination of several rupture points makes it possible to define the place of flow, which corresponds to all the rupture points. This flow place makes it possible to determine the flow function, an intrinsic parameter of the powder, allowing its flowability to be quantified. Since a breaking point (σN, τR) is dependent on the initial state of consolidation of the powder, it must be ensured that this state is the same for each measurement in order to obtain usable results.
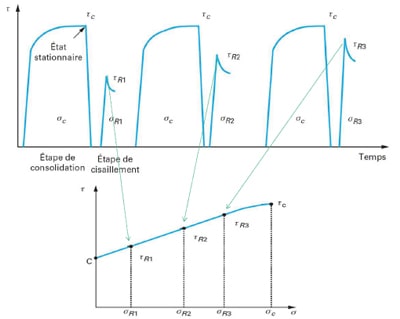
Measurement protocol: determination of the place of flow by the Jenike shear test
6. Solutions / results
The analysis of powders makes it possible to adapt the various equipment making up the production line.
Therefore, we can offer you different pneumatic transfer technologies (aspirated or pushed, dense or diluted phase) or vibration solutions, adapted to your products and process, to facilitate the flow of powder and bulk products during the storage and transfer phases.
We can help you determine the right type of equipment for your production goals. Different technologies are available: Fluidification plates and nozzles, Vibro-aerators, Air Cannons, Pneumatic and Combined Impacts, Pneumatic Vibrators…
Contact our team of professionals to find the right solution for you!