IBC container discharge: why do industrial sectors choose IBCs for powders and bulk materials ?
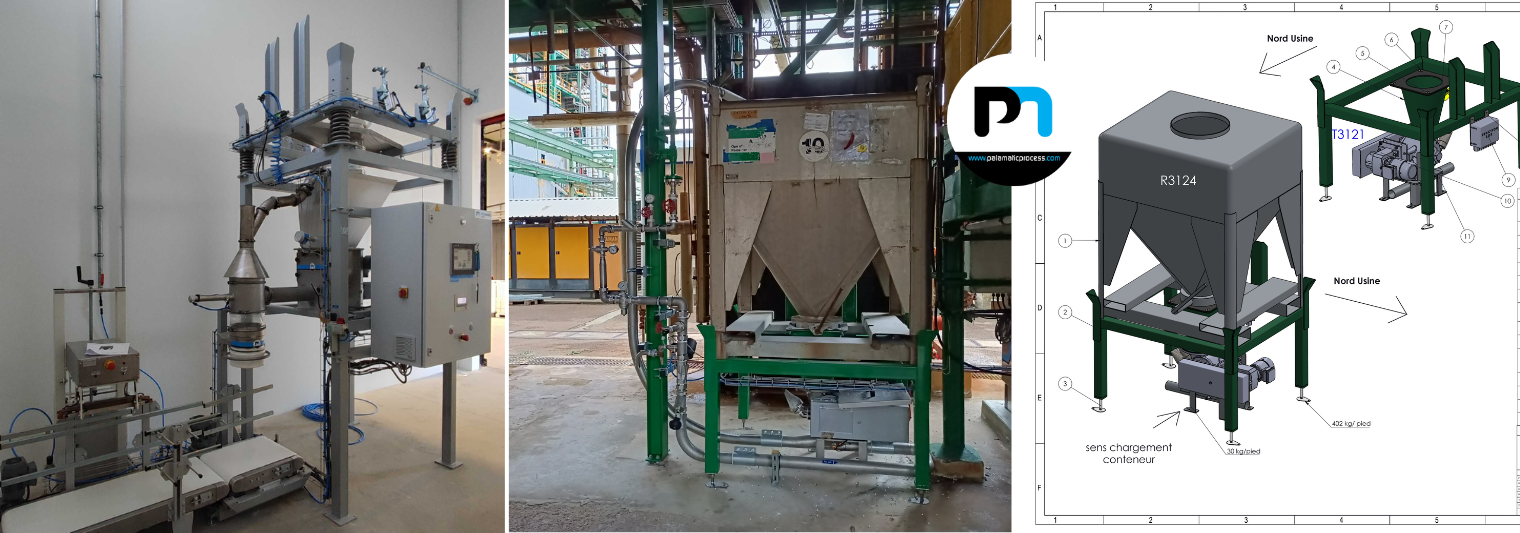
In industries handling powders and granular bulk materials, choosing the appropriate container is critical for ensuring smooth product flow, minimising waste, and safeguarding operator health. Bulk bags, drums, sacks, octabins, and IBCs all have their place depending on requirements for containment, hygiene, and ergonomics.
IBC containers (Intermediate Bulk Containers) are increasingly selected by UK manufacturers due to their ability to reduce dust emissions, facilitate clean transfers, and accommodate flexible dosing. Why are IBCs replacing traditional storage formats in so many facilities? This article explores their advantages in controlled discharge, product safety, and operational efficiency.
1.Comparing storage and discharge solutions for bulk powders
Various bulk storage and discharge solutions are used across the industry, each with its own strengths and limitations depending on the product type, hygiene requirements, and process scale. Here’s how bulk bags, drums, octabins, and IBCs compare in typical powder handling environments.
1.1. Bulk bags: an economical but limited solution
Bulk bags are a popular low-cost choice for transporting and storing powders. However, they can cause problems such as bridging, clumping, and inconsistent flow. Opening them often leads to significant dust release, and they typically require hoists or forklifts for safe handling. Their one-way use also increases waste and logistics burden.
1.2. Drums and sacks: suitable for small batches
Drums and sacks are commonly used in laboratory settings or for smaller production volumes. While they’re easy to move, they require frequent manual handling, which increases the risk of product contamination. They also contribute to higher packaging waste compared to bulk containers.
1.3. Octabins: balancing volume and protection
Octabins offer better rigidity and protection than bulk bags and are suitable for large volumes. However, they often require additional equipment to manage discharge effectively. For more advanced systems, see Palamatic Process powder discharge solutions.
1.4. IBCs: optimised for safe and contained discharge
IBC containers combine hygiene, safety, and flow control in a reusable format. Their rigid structure prevents bridging and allows controlled discharge with minimal dust. Unlike bulk bags, IBCs support partial emptying, and their sealed systems limit exposure and contamination. They can also be cleaned via automated washing systems to ensure full traceability and product integrity.
2. Key benefits of using IBCs for powder and bulk material handling
2.1. Cleaner and safer discharge
Discharging powders often results in dust generation and material loss, which can pose health and safety risks. IBC containers are designed to reduce this through sealed discharge systems and dust extraction options. The result is a cleaner workspace and safer working conditions for operators.
2.2. Greater flexibility with raw materials
Unlike bulk bags or octabins, IBCs enable partial discharge, allowing for precise dosing and better stock control. This makes them highly versatile in batch processes, reducing product waste and downtime during changeovers. Their sealed environment also helps prevent cross-contamination when switching between different materials.
2.3. Operator-friendly design and ergonomics
IBC systems are designed with ergonomics in mind. Their structure allows for easier handling compared to bulk bags, and many systems include automated discharge solutions that reduce the need for manual intervention. This helps improve efficiency and operator wellbeing.
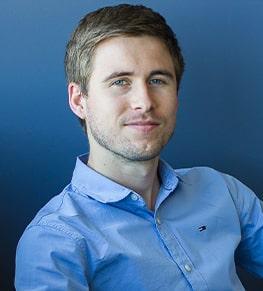
Considering a project involving IBC container discharge ?
I’m available to provide tailored advice and support throughout your process.
Guillaume, expert in IBC handling and discharge
3. How to fill an IBC container ?
3.1. Gravity filling
Gravity filling is the most straightforward method. The IBC is placed under a silo or hopper, allowing product to flow freely by gravity. While economical, this setup may lead to dust emissions if it lacks proper containment or dust extraction systems.
3.2. Manual sealed system
A manual sealed filling system offers better dust control. It typically uses a movable cover or inflatable seal that encloses the container’s inlet during filling. Though semi-automated, it significantly reduces contamination risks. See Palamatic's sealed powder transfer systems for more details.
3.3. Fully sealed filling system
For hazardous, volatile, or sensitive powders, a fully sealed system is preferred. An inflatable seal creates an airtight barrier, and pressure balancing ensures smooth product flow without introducing external air. This method is ideal in pharmaceutical and food-grade environments requiring maximum containment.
4. How to discharge an IBC container ?
4.1. Gravity discharge
The simplest method is gravity discharge, where the IBC is positioned above a hopper or feeder. The outlet valve is opened, allowing the material to flow downward naturally. While cost-effective, this setup can release dust if not paired with a sealed connection.
4.2. Tulip seal connection
A tulip seal system forms a tight, dust-free connection between the IBC and the discharge station. It is ideal for sensitive applications where product integrity and air quality are key. This approach is commonly used in Palamatic’s bulk handling systems.
4.3. Flow-assist discharge system
When dealing with bridging, cohesive, or sticky materials, flow-assist systems are essential. These use vibration or mechanical agitation to maintain a consistent discharge rate and prevent blockages. They are ideal for fine powders or dense granules.
4.4. Split butterfly valve solution
A split butterfly valve offers a contained and hygienic discharge. One half is fixed to the IBC, the other to the discharge station. Once joined, they form a sealed transfer point that protects the product and environment—commonly used in high-care sectors such as pharmaceuticals and food processing.
5. Frequently Asked Questions
5.1. Are IBCs more expensive than bulk bags?
Yes, IBC containers have a higher initial cost than single-use bulk bags. However, they are reusable, more hygienic, and designed for clean and controlled discharge. Over time, they provide a more cost-effective and sustainable solution.
5.2. How do I ensure a dust-free discharge?
The most effective way is to pair the IBC with a tulip seal or split butterfly valve, and include dust extraction or air filtration if required. For detailed guidance, explore Palamatic's powder discharge solutions.
5.3. Can discharge be automated?
Absolutely. Automated IBC discharge systems can manage flow rate, monitor fill levels, and trigger valve control. These systems enhance safety and reduce manual handling while improving process reliability.
5.4. What is the capacity of an IBC?
Standard IBCs range from 500 to 1,500 litres, but capacities can be tailored to meet specific needs. The optimal size depends on batch size, storage constraints, and flow properties of the material.
5.5. Can one IBC be used for multiple products?
Yes—provided the IBC is thoroughly cleaned between uses. Automated washing stations and smooth internal finishes help avoid cross-contamination. See Palamatic’s hygienic IBC handling solutions for more information.
Conclusion
IBC containers offer a robust, hygienic, and efficient solution for handling powders and bulk materials. Their sealed design ensures safe discharge, minimises dust emissions, and improves process traceability—making them ideal for high-performance manufacturing environments.
Palamatic Process provides a range of solutions to suit your operational needs:
- IBCFlow® 01: a simple, manual discharge station for standard use.
- IBCFlow® 02: a semi-automated solution with advanced control systems.
- Bespoke systems: designed and built to match your industry-specific challenges.
Get in touch today for a personalised consultation and explore how our IBC discharge solutions can streamline your powder handling operations.