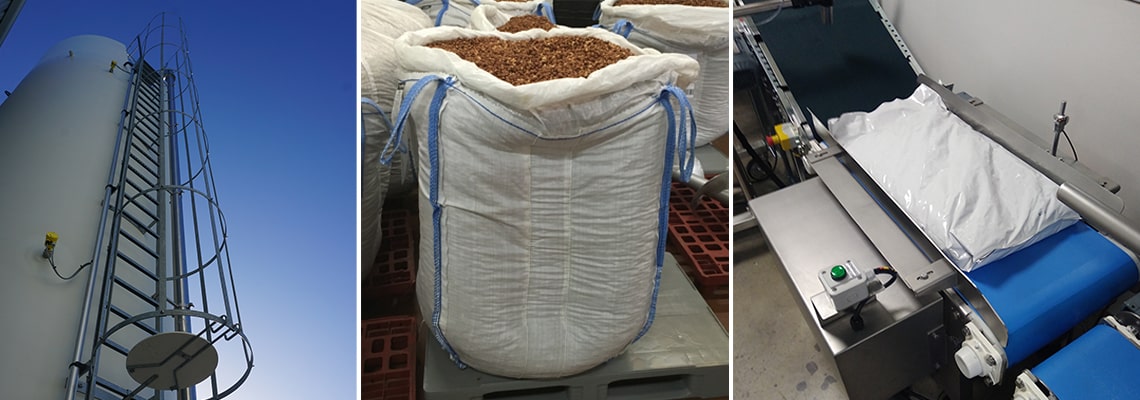
The consumption of ingredients in bulk often represents large volumes for manufacturers in the agri-food, chemical and pharmaceutical sectors, etc.
In order to minimize handling for operators, manufacturers should ask themselves what is the best storage method for my process? Several criteria are taken into account to define the right packaging.
1. The volumes processed
The total volume of powders handled is the major criterion to guide your choice of storage vessel.
4 main types of storage exist within the bulk material industry:
1- Small sacks
Usually packaged in 50 lbs. quantities, the sacks offer great flexibility in use and handling. The additional advantage of sacks is the quality of preservation offered by current bagging filling techniques.
The bags can be welded, sewn, with several bags, inner liners for handling in a white zone, packaging in a controlled atmosphere (nitrogen, neutral gas), etc. Packaging in sacks on a European pallet generally represents 1 ton of powder materials.
2- Big bags / gaylords
Increasingly used in the food and chemical industries, big bag packaging offers production operators a certain autonomy. The installation of big bags on stations specially designed for their unloading must provide a buffer of at least 30 minutes.
Big bags, in addition to minimizing handling operations, offer excellent powder preservation quality with many options available (internal bag, neutral gas, variable volume, stacking, internal partitioning, etc.).
One point to consider is the flow characteristics of the powders packaged in bulk bags. Some powders cannot withstand this type conditioning, which can promote the creation of lumps or agglomerates.
3- Bulk silos / powders
For industrial sites that consume significant raw materials, silo storage is essential. Industrial bakeries, extruders or cement manufacturers set up several silos on their sites for the storage of flour, plastic granules, cement, carbonate, silica, etc. Storage in silos offers a very large capacity from 60 m³ and up to more than 200 m³. The silos are loaded by blower truck or directly via the production lines. The silos offer many options which allow the storage of food products (manufacture, food resin, stainless steel manufacture, controlled atmosphere, dehumidification, etc.).
As with bulk bags, products stored in silos must be compatible with storage under load. The product column compresses the powders and amplifies the deaeration of the products. These stresses can cause caking and a significant difficulty in extraction.
Contact our storage experts to define the possible fluidization, vibration and air cannon options!
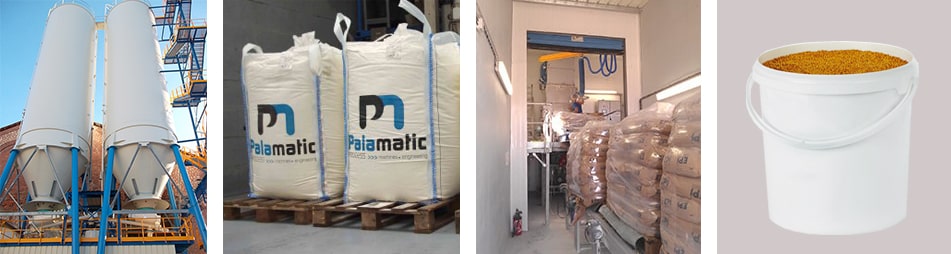
4- Custom / made-to-measure packaging
For your specific process and manufacturing recipes, suppliers can provide custom-made packaging for your powders. The packaging is produced in buckets or drums at a desired weight. This solution offers a perfect match between the volumes required in your processes and handling for weighing operators. This point to consider with contract packaging is the high cost of these made-to-measure containers, and the flexibility of supplier sourcing.
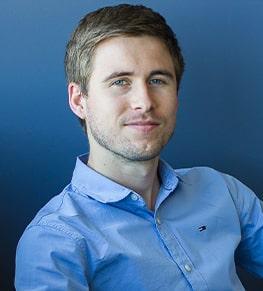
Do you need additional information?
I can help you and support you in your project.
Guillaume, expert in powders
2. Lot management
When you use powders packaged in sacks, it is much easier to ensure the management of production batches by the traceability of the packages.
The opposite case arises with silo packaging. Silo packaging does not allow precise monitoring of production batches. In applications requiring one, it will be essential to provide 2 silos in order not to cross delivery of materials and to guarantee complete emptying of the silos.
Big bags are perfectly compatible with batch management. Identification labels are always present on the big bags and “document holder” pockets are also possible.
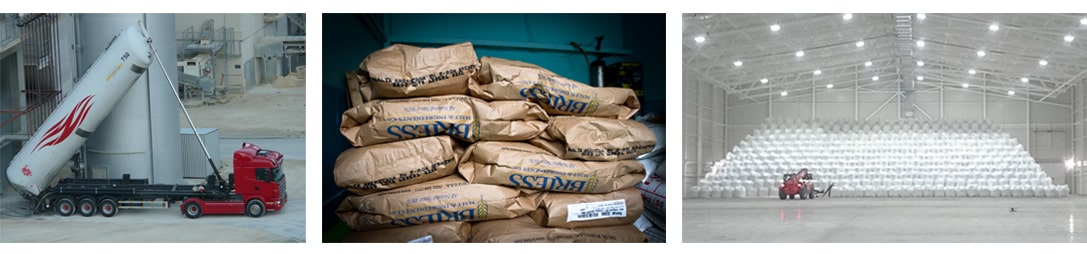
3. Handling my powders
Choosing your type of bulk packaging requires analyzing the handling method to be implemented according to the nature of your powders.
The powder bags require a high level of handling and treatment to contain any emission of dust. The bag dump stations are necessary to provide an ergonomic operator workstation. The treatment of empty sacks should also be taken into account. Spent sack solutions exist such as our sack compactors.
For big bags, handling structures are essential to provide a quality unloading process of powders. Manufacturers using big bags must be equipped with safe and efficient unloading stations. The use of electric hoist, forklift for heavy loads is to be expected.
Handling powders stored in silos does not require any intervention from the operators but a high level of equipment. The infrastructure must be equipped with a truck unloading dock for the silos.
4. The flexibility of my suppliers
Before selecting the type of bulk packaging suitable for your materials, contact your supplier to find out in what form he can deliver your raw materials: delivery by bulk truck, tanker truck, bulk bags, bags, containers, etc.