SmashR® : l’émotteur intelligent pour casser les blocs et masser automatiquement vos big bags

In industries that handle powders or bulk products, prolonged storage or transport can cause the formation of compact blocks inside flexible containers (big bags). This not only impedes the flow of materials, but also compromises dosing performance and overall production yield. To address this issue, Palamatic Process has developed SmashR®, an innovative and automated crushing device capable of effectively breaking up clumps thanks to an intelligent motorised massaging unit.
Equipped with a motorised conveyor on a lifting table, a barcode reader and automated cycle management according to the type of big bag, this solution offers a high level of customisation, traceability and performance. It guarantees the fluidity of powders and maintains the quality of downstream processes, without manual intervention.
In this article, we take a closer look at how the tool works, its concrete advantages, and the answers to frequently asked questions about this innovative equipment.
1. The SmashR®: an automated breaking and mechanical stress station
Equipment structure: lifting table, motorised conveyor, receiving hopper
Our equipment is a complete industrial solution, designed to be integrated upstream of a drainage station or dosing station. It consists of several robust and complementary mechanical components:
- A motorised conveyor: this allows the automatic transport of bags intended for solid bulk to the treatment area without manual intervention, thus ensuring a smooth and continuous feed.
- A hydraulic lifting table: this precisely adjusts the height of the packaging to position the area to be massaged at the level of the massage heads. It adapts to different bag sizes.
- Motorised rubbing arms: these lateral cylinders exert targeted pressure on the sides of the flexible storage format, to break up the internal clumps without perforating the bag.
- An optional receiving hopper (at the outlet) allows the process to continue towards a transfer screw, a sieve or a dosing module.
This modular and automated structure guarantees reproducible, secure and ergonomic processing, even with heavy or difficult-to-handle big bags.
How block massaging and breaking works
The operating principle is based on an automatic pressure cycle, programmed according to the type of big bag and the nature of the product. Once the bag has been loaded via the conveyor, the lifting table positions the bag at the optimal height. The motorised arms then massage the sides at regular intervals according to a defined sequence.
This controlled pressure movement detaches the compact blocks formed inside the bag, thus releasing the material and preparing the bag for smooth and smooth emptying.
Our machine can also operate in cyclic mode or intelligent mode, with dynamic adjustment of the pressure exerted according to the resistance encountered. Everything is controlled via a touch screen and a user-friendly interface integrating personalised settings.
2. An intelligent package tailored to each customer
Automatic management of massage cycles according to the characteristics of the high-capacity industrial packaging
Each product handled has its own specific characteristics: some form crumbly lumps, others very compact blocks, while the grain size or humidity can vary considerably. This is why our lump breaking unit incorporates a logic of intelligent management of massage cycles.
Thanks to a programmable logic controller, the equipment automatically adjusts:
- the intensity of the pressure of the motorised arms,
- the duration of the massage,
- the number of cycles necessary before authorising emptying,
- the vertical position of the pressure via the lifting table.
These settings are adjusted according to the type of big bag detected, thus ensuring personalised treatment for each product reference, without the need for human intervention. The result: fewer errors, better material flow and increased productivity.
Recipe programming by barcode reader
It incorporates a barcode reader that plays a central role in the traceability and automation of the process. When an FIBC arrives on the conveyor, the reader immediately identifies the product reference and triggers the appropriate massage recipe.
Each recipe contains the following parameters:
- cycle time,
- cylinder force,
- massage height range,
- type of product (fine powder, granules, hygroscopic, etc.).
This optical scanning avoids any manual input, makes the operation more reliable and allows for instant adaptation even in the case of multi-reference production. In the event of a modification, an authorised operator can reissue the recipe via the Pal'Touch® HMI.
How does the automatic management of massage cycles work?
Our material preparation system uses a PLC connected to a barcode reader to trigger a massage cycle adapted to the FIBC detected. Once the code has been read, the system automatically loads the corresponding recipe (intensity, duration, frequency, position). This operation guarantees homogeneous treatment, adapted to the product, without manual intervention, and limits human error.
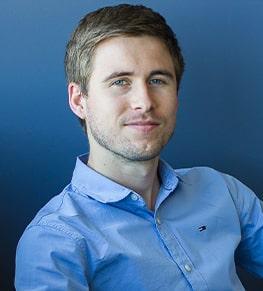
Working on a powder dosing or transfer project ?
I’m available to help you evaluate your needs and find the best solution.
Guillaume, expert in powder handling solutions
3. Automation, traceability and operator safety
Integrated automation and time saving
Our compaction removal solution is designed to operate completely autonomously. Thanks to its integrated automation, the entire cycle - from the identification of the flexible bag to the end of the massage - is carried out without human intervention. The station is fully integrated into a modern industrial logic:
- Automatic detection of the flexible container at the entrance via a motorised conveyor.
- Reading of the barcode and automatic loading of the recipe.
- Massage cycle activated according to the programmed settings.
- Visual signal at the end of the treatment and transfer to the unloading station.
This automation saves a significant amount of time, reduces the risk of human error and frees operators from tedious and repetitive tasks. It is thus part of a logic of rationalisation of flows, with increased machine availability.
Operator safety: confined operation, without contact with the product
One of the major advantages of our technical solutions is that they eliminate manual interventions that are often dangerous, such as tapping or directly handling the bags to break up clumps.
The closed structure of the station, combined with position and safety sensors, prevents any contact between the operator and the motorised arms during the cycle. The big bag remains confined, and access is blocked until the treatment is completely finished.
Furthermore, by eliminating manual handling, the device limits the risk of musculoskeletal disorders (MSDs) and dust inhalation when bags are opened prematurely, and ensures a clean and safe working environment.
Why integrate a barcode reader into a powder handling process?
The barcode reader allows the type of big bag to be identified automatically and the appropriate loading recipe to be applied. It guarantees traceability, avoids manual parameterisation errors, speeds up batch changes and allows for uninterrupted multi-reference production. It is an indispensable tool for automating and improving the reliability of the workstation.
4. Integration into a complete flexible load handling line
Compatibility with downstream emptying or dosing systems
It has been designed to be inserted directly upstream of an FIBC cleaning, weight dosing or pneumatic transfer station. Once the massage cycle is complete, the chute bag is conveyed to the next station via a motorised or gravity roller conveyor, depending on the installation.
It can thus feed without interruption:
- a buffer hopper equipped with a controlled flow device with a sealed sleeve,
- a screw or belt feeder to regulate the flow,
- or even a sifter to ensure material safety before bagging.
This fluid interconnection makes our solution perfectly compatible with Palamatic Process automated lines, whether for filling, dosing, transfer or packaging.
Synchronisation with emptying or transfer stations
The SmashR® station can be synchronised with the rest of the line thanks to its automated device. It exchanges in real time with:
- the emptying station (availability signal, end of cycle),
- the dosing system (authorisation to feed after lump breaking),
- the centralised control via Pal'Touch® (recipe monitoring, performance indicators).
This optimises the management of material flows without overloading or shortages, and each big bag that is processed is then emptied immediately, without the need for intermediate handling.
This approach guarantees the continuity of the process and maximum productivity, integrating lump breaking as an invisible but essential stage of the line.
Is the SmashR® suitable for reinforced textile bags of different sizes?
Yes, it can be adapted to different flexible container formats thanks to its adjustable lifting platform and variable amplitude massage arms. It can handle big bags from 500 to 1500 kg, with one or four handles. Recipe management allows the correct parameters to be loaded automatically according to the format detected via the barcode.
Conclusion
In an industrial environment where the regularity of flows and the safety of operators are major issues, the device is the ideal solution for handling big bags containing compacted products. Thanks to its automated lateral massage technology, intelligent cycle management and simple integration into complete handling lines, it guarantees smooth flow, without blockages, without manual intervention and with total traceability.
Whether you are handling fine powders, hygroscopic granules or products with a high tendency to form lumps, it provides a robust solution that allows you to maintain your throughput rates, improve the quality of your dosages and reduce your maintenance costs.
Designed to adapt to your industrial constraints, our lump breakers can be integrated as a customised solution into your existing installations, or into a Palamatic Process turnkey line.