Description
Big bag conditioner - Crushing of big bags to break up the build-up of the product
The SmashR® Conv big bag emptying station gives operators autonomy in decompacting powders stored in big bags. In its automatic version it controls massaging cycles, cycle times and the evacuation of the conditioned big bag without the need for repetitive operator intervention.
It optimizes production times and automates the crushing of lumps contained in big bags.
"Standard" cycle
- The big bag is fed onto the conveyor
- Cycle starts automatically
- The gates exert 4 upwards pressure on the big bag.
- Table rotates 90°
- The wings exert 4 upwards pressure on the big bag.
- Table rotates 90°
- The cycle is complete, and the big bag is automatically discharged.
The number of presses and table turns is adjustable.
Duration of "standard" cycle: 5 min.
Output: approx. 12 big bags/hr
Force: > 15T / > 150 kN
Objectives: Decompact big bags
Equipment advantages
- Breaks up powder lumps, facilitating complete big bag emptying.
- Clean process: the powder is decompacted directly in the big bag.
- Uses pivoting wings to reach the core of the product without damaging the big bag.
- Adapts to big bag volumes and powder hardness
Media
View our equipment in videos
Big bag conditioner SmashR
Big bag decompactor for easy emptying of your product.
Control screen of big bag conditioner SmashR®
Bulk bag massager
View our equipment in photos
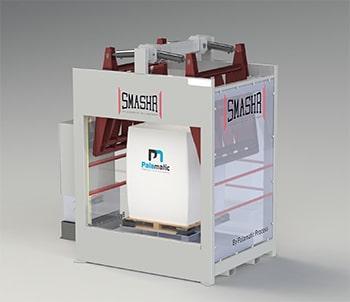
Big bag crusher
The big bag or FIBC conditioner is the ideal solution for breaking up the mass of your products.
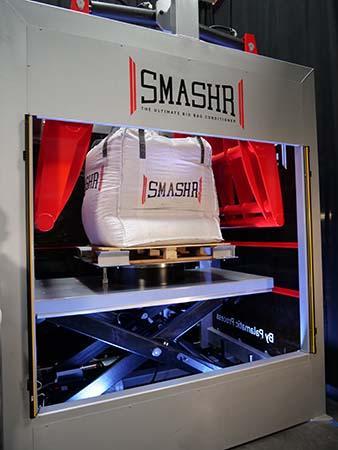
Easily unload big bags
SmashR® facilitates the flow of your product and allows for easy emptying of your FIBCs.
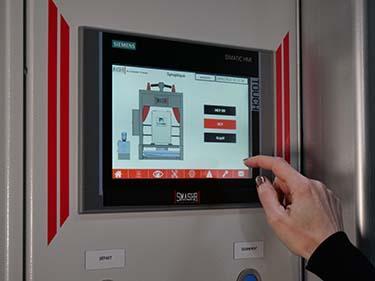
Remote control SmashR®
The SmashR® machine is controlled remotely via a dedicated PLC.
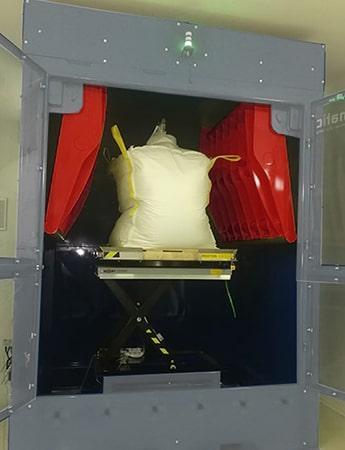
Decompacting the big bags
SmashR® the ultimate big bag conditioner decompacts your big bags throughout your production process thanks to its hydraulic massage system.
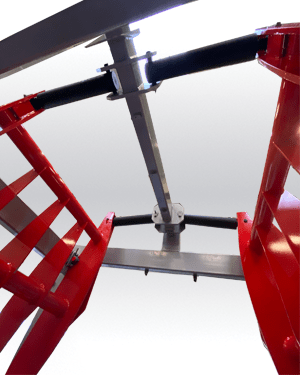
FIBC decompactor SmashR®
Decompaction of FIBCs using the hydraulic cylinders of the SmashR® massage cage.
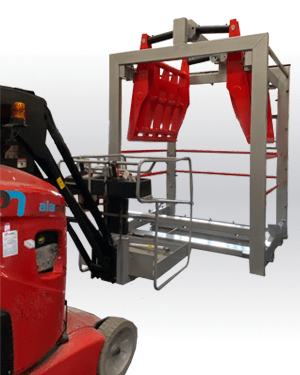
Big bag conditioner
The big bag conditioner optimises discharging for your production operators.
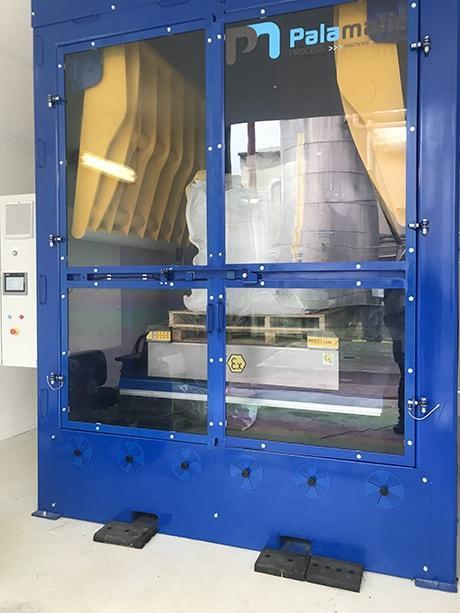
Big bag crusher
Crusher for big bags, the arms are operated by hydraulic cylinders.
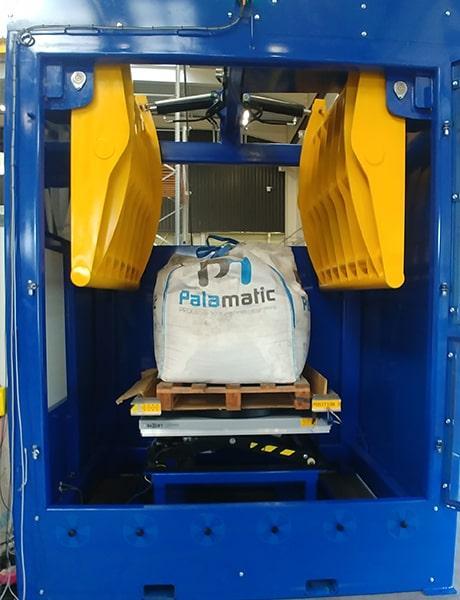
Side puncher - Big bag unloader
The punching system is used to prepare the bulk bags before emptying.
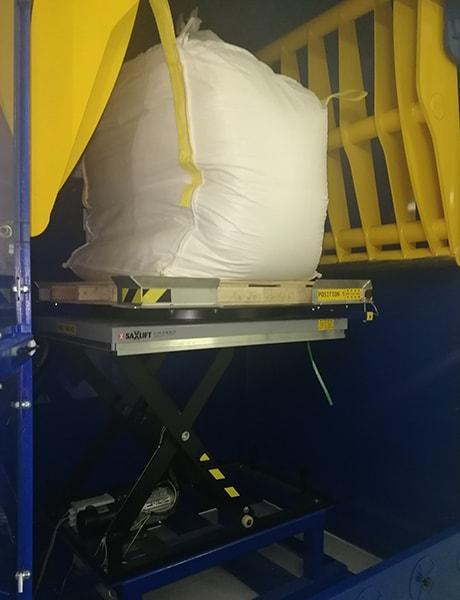
Big bag conditioner
The crusher optimises discharging of your bulk products.
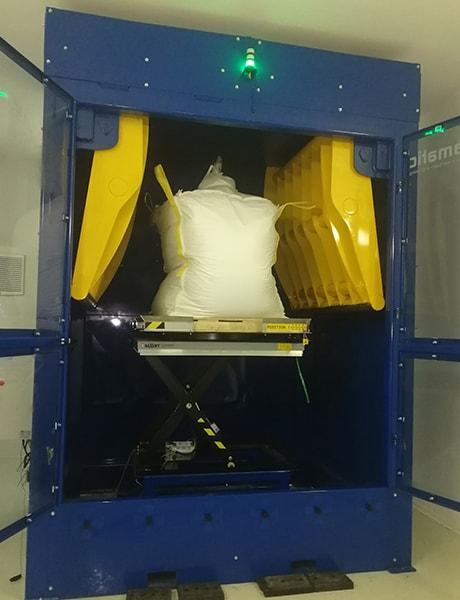
Big bag preparation
The punchers are operated by hydraulic cylinders.
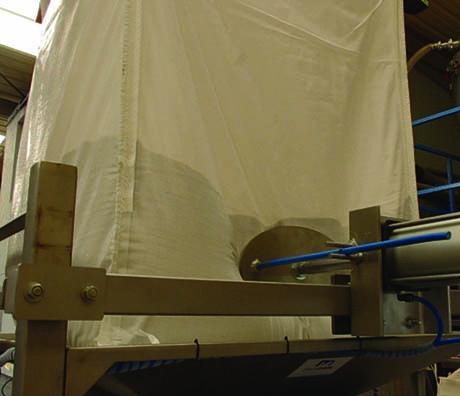
Side puncher - Jumbo bag discharging
Prepare and break the blocks of bulk material before unpacking.
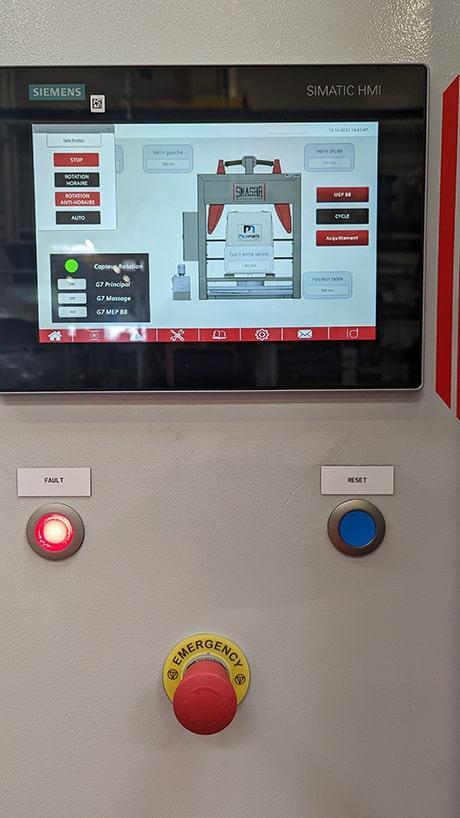
Touch-screen control panel
The operator selects the desired operating mode from several pre-set modes. Each mode is configurable.
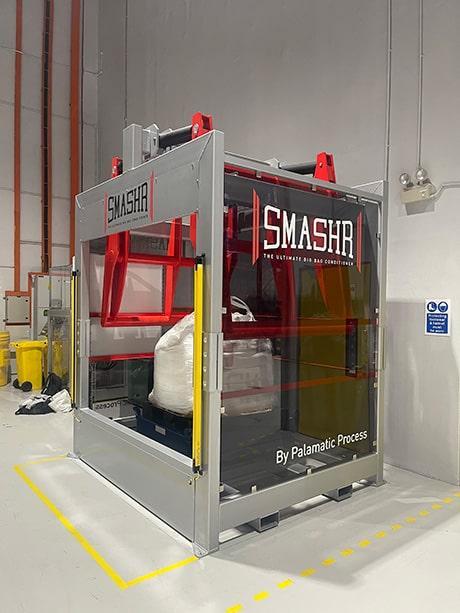
Big bag conditioner
The massaging station comprises 2 pairs of hydraulic cylinders, enabling simultaneous massaging of 2 opposite sides of the big bag via the flaps.
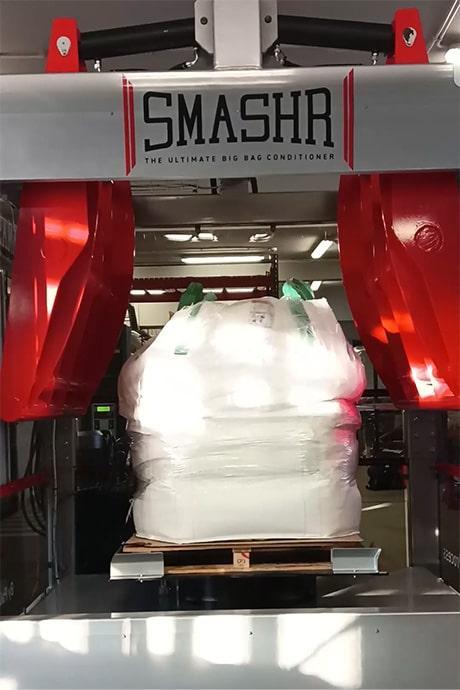
Big bag unpacker
The massage station consists of 2 pairs of hydraulic cylinders, allowing simultaneous massage via the flaps on 2 opposite sides of the big bag.
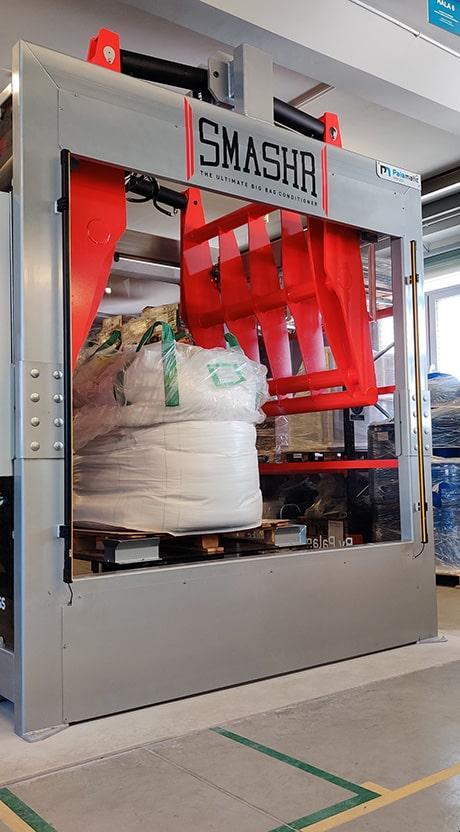
Big bag crusher
The big bag is massaged by hydraulic pushers, which break up the mass of the big bag when it is "in block" to facilitate emptying.
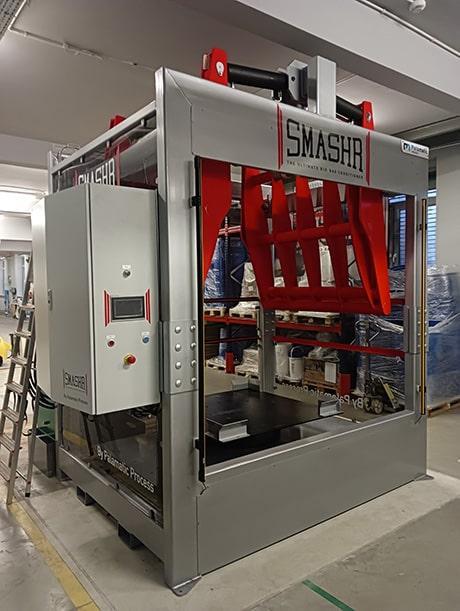
Big bag massaging station
For product preparation prior to unpacking.
Features
Technical specification
Rate |
12 big bags/hr |
---|---|
Force | >15t./>156 kN |
External dimensions of cage | 2,600 x 2,200 x 3,450 mm |
Maximum lift table load | 1,500 kg |
Carrier dimensions | 1,700 x 1,000 mm |
Maximum big bag height | 1,600 mm |
Raising cycle time | 25 seconds approx. |
Descent cycle time | 10 seconds approx. |
*If the big bag height is greater than 1,600mm, the SmashR® Fly is the appropriate model.
Operating mode :
1. The big bag is conveyed by conveyor.
2. The decompaction mode has been pre-selected, taking into account:
- Big bag height
- Number of massage cycles
- Number of times the table is raised/lowered
- Once the operating mode has been selected, the operator launches the cycle from the control panel.
3. The massage cycle starts automatically.
4. Once the cycle is complete, the big bag is discharged onto the conveyor.
Options
Case studies
CASE STUDIES WITH THIS EQUIPMENT
Handling milk powder on production lines
Powder processed: milk powder Handling of milk powder on the production lineFood and Animal Feed
Handling of lithium, cadmium and oxide powders
Processed powders: lithium, cadmium and oxides Decompaction and emptying of big bags for battery manufactureEnergy
Optimising the handling and unloading of big bags to improve safety and production
Powders treated: hygroscopic powders such as metal sulphates Optimising the handling and unloading of big bags to improve safety and productionEnergy
Optimising automated bulk bag discharge for lithium powders
Powders handled: Lithium carbonate (Li₂CO₃), iron oxide (Fe₃O₄), lithium Optimising automated bulk bag discharge for lithium powdersEnergy