Description
The PalBox®02 packing station provides filling of bags or boxes via a precision vibrating feeder
Designed to handle fragile products, in sheet or granular form, the material dosing is handled by vibration to respect delicate materials and friable products.
The quantity by weight accuracy is ensured by a variation of the vibration amplitudes and a quick-closing valve. The dosing accuracy is +/- 5 grams.
-
Rate4
-
Fragile material5
-
Automation5
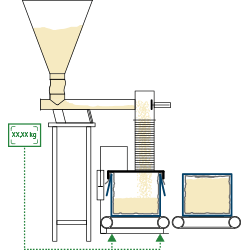
PalBox®02-C-Gross
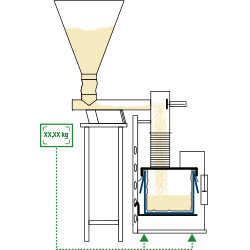
PalBox®02-P-Gross
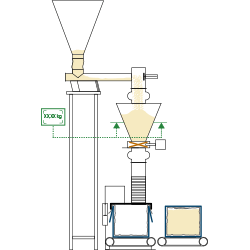
PalBox®02-C-Net
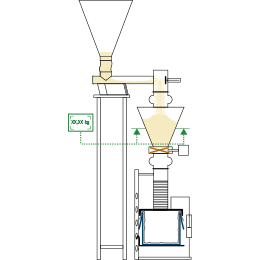
PalBox®02-P-Net
Possible configurations of the PalBox®02 model:
Ref. | Possible equipment | Functions | Advantages | |
---|---|---|---|---|
Choice 1 | P | Tray support | Holds bag during filling | Hygiene, height adjustment for adaptability to carton format |
C | Evacuation conveyor | Holding and evacuation of the cardboard during packaging | Ergonomics, increased cadence | |
Choice 2 | Net | Net weighing | Prepares the correct amount to be packed | Accelerated rate (product prepared in hidden time) / may require double weighing |
Gross | Gross weighing | Weighing of the entire container and contents | Commercial weighing, traceability |
Our PalBox®02 packaging machine can be configured by modulating the possible basic equipment: choice 1 + choice 2.
Example of possible reference: PalBox®02-P-Net
Hygienic design
The entire box filler assembly is made of stainless steel and is designed to limit areas of retention. The vibrating feeder technology also offers an optimal solution for cleaning phases. The vibrating corridor is extremely easy and quick to clean.
Applications
The integration of the PalBox®02 filler is ideal for food-processing applications (spices, tea, capsules, sweets, confectionery, etc.) or chemical applications for friction-sensitive powders (explosive powders, compressible powders, etc.).
Packaging / cartoning rate
Depending on your production goals, the PalBox®02 packaging station is available in several configurations to achieve high filling rates (up to 200 boxes/hour) depending on the size of the bags and the type of products.
One configuration that makes it possible to achieve high flow rates is the installation of an intermediate weighing hopper to prepare the correct amount to be packed in hidden time. This net weighing configuration, however, requires a subsequent weight control on the packaged cartons.
Furthermore, the higher packaging throughput can be increased by installing belt conveyors or motorized roller conveyors to help manage box handling and transfer.
The ergonomics of the packaging stations is studied by our design office to offer packaging operators efficient and comfortable stations.
Equipment advantages
- Semi-automatic packaging
- High filling rates
- Guaranteed dust-tight design
- Guarantee of batch traceability
- Overall management
- Dosing precision
Media
View our equipment in photos
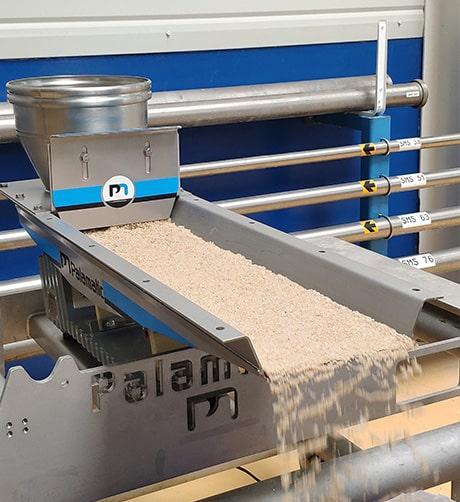
Vibrating feeder suitable for fragile products
The vibrating feeder allows the dosing of powders and granular materials.
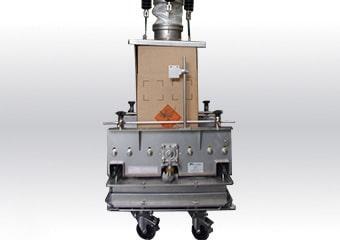
Carton packing station
The containment tray lays flat against the cardboard to ensure dust sealing and containment.
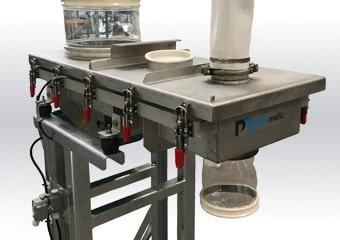
Assembly with vibration metering
Vibrating feeder for feeding fragile and brittle products to a packaging machine.
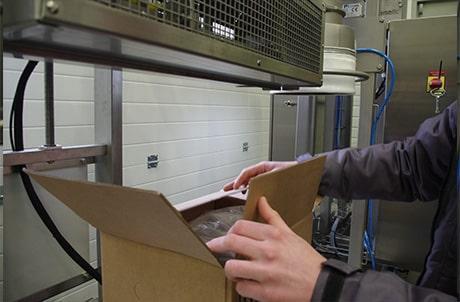
Box closing
Manual closing of the box after sealing of the inner bag.
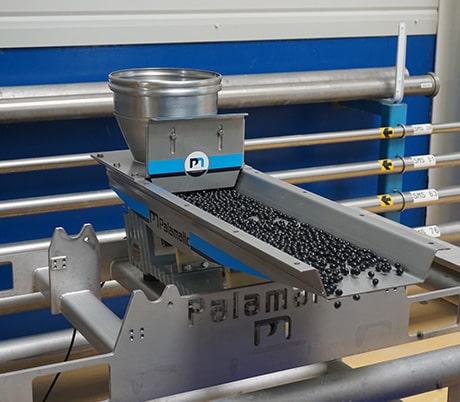
Vibrating feed system for gentle handling of fragile products
The vibration allows respect of the product (no moving parts in the vibrating feeder) for packaging lines that handle friable bulk materials.
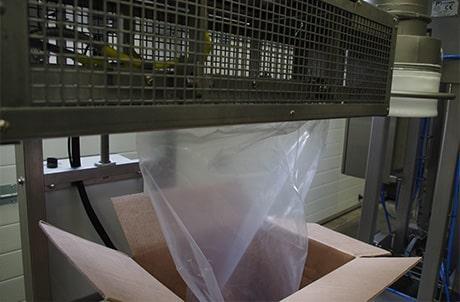
Bag sealing
Air-tight sealing of the inner bag using a thermal welder.
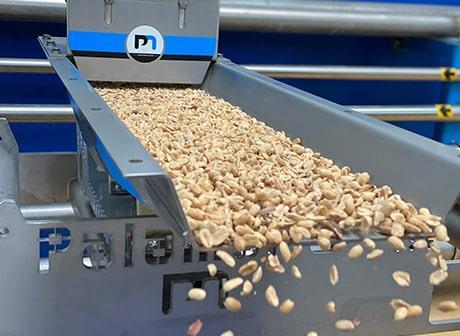
Industrial dosing for box filling
Metering peanuts on an industrial packaging line. The vibrating device allows the accurate transfer of fragile products.
Features
Technical specification
Containment
The handling of powders and bulk solids (granules, pellets, etc.) generally results in dust emissions. For the safety and cleanliness of the production facility, it is important to reduce and capture and dust or fine particulates.
The PalBox®02 bagging machine covers the cardboard with a telescopic containment tray. This pneumatically actuated lid is placed over the box to seal and contain dust during filling. A flexible sleeve prevents interference with load cells and weighing functions. In addition, nozzles for dust collection are provided in order to balance the volumes and ensure a healthy atmosphere for the operators.
Piloting and Controls
The Palamatic Process bagging machines of the PalBox® range all incorporate PLC’s and servo-control cabinets. All adjustment parameters are accessible via the control touch screen.
Production batch history is fully stored with all necessary data for good food traceability: batch number, set weight, packed weight, precision, operator, etc.
Our automation and industrial IT design office adapts to your specific constraints in addition to business standards.