Description
The PalDrum®04 drum filling station with rotating pallet provides semi-automated, high-accuracy filling with twin-screw dosing technology.
The Palamatic Process D14 twin-screw feeder provides high flow rate and fine precision due to the dual dosing screws. Each auger is driven by an independent motor allowing individualized control and automation. To ensure dosing regularity and maximum precision, the dual screw feeder makes use of an integrated agitator to provide smooth bulk material flow.
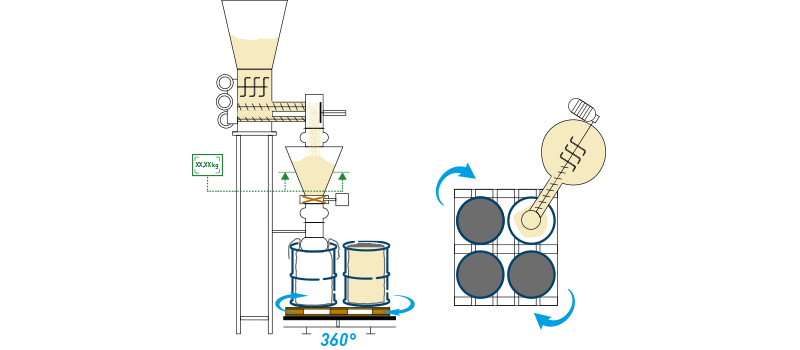
The double jacketed filling head allows for efficient material filling and connection to your dust collection system. Automated height adjustment of the fill head framework helps improve operator safety, and increase drum-per-hour fill rates, relative to manual operation.
The semi-automated pallet table allows an operator to load four, empty 200 litres drums at a time. A pre-weighed GIW (loss in weight) hopper prepares the material to be dosed into the drum. Once the first drum is filled, the operator signals the touch screen PLC to commence to the second position on the pallet.
The Palamatic pre-weigh drum filling scale system provides consistent fill weights in applications where mid- to high-volume throughput requirements are required. While a drum is being filled, the filling system is simultaneously reloading the buffer hopper and pre-weighing material in preparation for discharge and filling into the next drum. The Palamatic Process pre-weigh systems is accurate to +/- 0.5% of the total filled drum weight (better accuracy possible in some applications).
For drums with an inner liner, the inflatable seal deflates releasing the dust tight connection to the drum. The pallet turns 90° to the second drum position. The operator places the inner liner around the inflatable seal and signals the control panel to resume the filling operation. The seal inflates to make a secure and dust tight connection.
The different possible configurations of the PalDrum®04 model:
Ref. | Integrated Equipment |
Functions | Advantages | |
---|---|---|---|---|
Choice 1 | I | Inflatable seal | Secure connection to inner liner | Maximum confinement |
C | Cover lid | Dust containment of open drums | Ergonomic design, various drum sizes | |
Choice 2 | Loss | Loss in weight | Accurate preparation of the material | Accelerated rate (dosing in hidden time) / may requite double check weighing |
Gain | Gain in weight | Weighing of the entire container and contents | Commercial weighing, traceability | |
Pallet turn table | MT | Motorized turntable | Semi-automatic placement of drums under the filling head | Safe orientation of drums on their pallet. |
Our PalDrum®04 packaging machine is configurable by modulating the possible basic equipment: choix 1 + choice 2.
Exemple of possible reference: PalDrum®04-I-MT-Loss
Description of choices:
Choice 2, 2 weighing modes:
As with all PalDrum® stations, the weighing technology can be selected according to your throughput.:
- Gain-in-weight: for weighing drums during filling (IPFA commercial weighing certification)
- Loss-in-weight: for weighing your products upstream and checking the weight after packaging on a secondary conveyor (IPFA commercial weighing certification)
For manufacturing processes that require a safe and secure filling procedure with the drums already on the pallet, the PalDrum®04 drum filling system offers all the necessary modular configurations, primarily:
- Semi-automatic turn table system
- Dust control by inflatable seal or pneumatic drum cover
- Automatic weighing and dosing
- Digital weight display
- Labeling (optional)
-
Automation5
-
Rate5
-
Dosage accuracy4
Equipment advantages
- Optimized safety:
- Drums never leave the pallet
- Security light barriers at operator working position - Semi-automated drum positioning
- Accurate material dosing by weight
- Adaptable to various drum types and connections
Media
View our equipment in photos
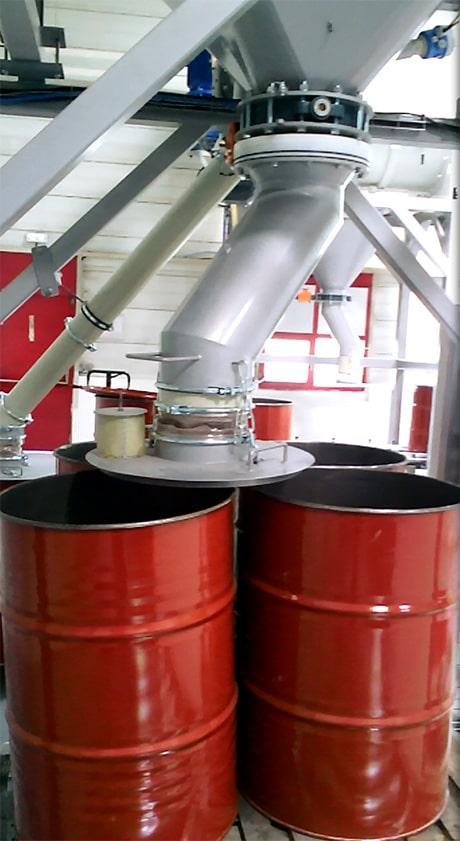
Rotating flange for filling on pallet
Fake lid to ensure a tight filling of the barrel.
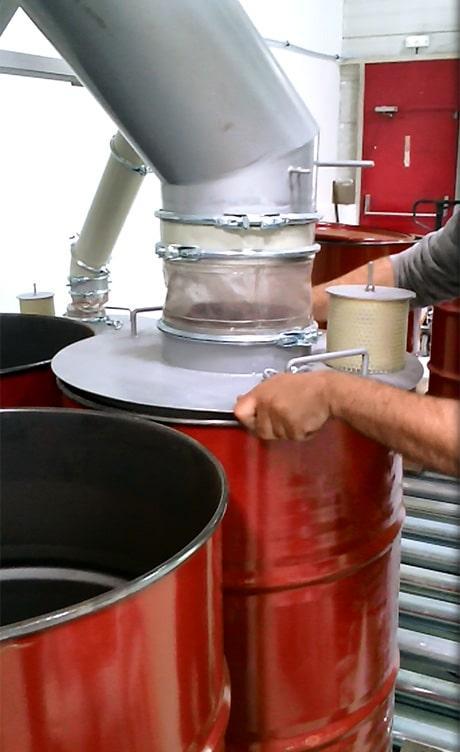
Positioning of the lid on the drum
The operator manually connects the drum/bucket to the filling opening.
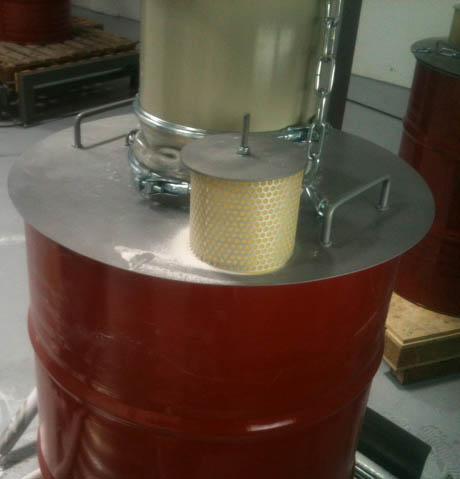
Containment of the filling station
Filling head on drums for confined filling.
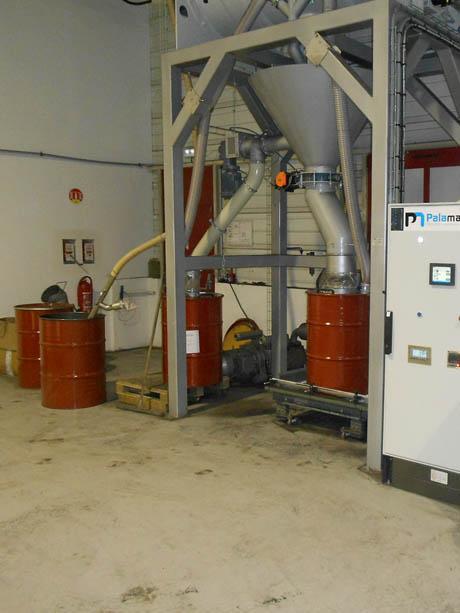
Filling of drums
Industrial line for automatic packaging of drums.
Features
Technical specification
Rate | 40 to 60 drums per hour |
---|---|
Capacity220 kg | 220 kg/drum |
Materials of construction | Painted steel, 304 or 316 Stainless Steel |
Accuracy | Possibility of +/-0,5% |
Theoretical Power consumption | 7.5 à 10 kW |
Dust removal rate | 200 m³/hr |
Mode opératoire :
- The material is prepared in the dual dosing screw feeder (operation can be done in parallel with drum preparation to improve global flow rate of PalDrum® 04)
- The operator connects the inner liner to the inflatable clamping seal, or, for drums with no liner a pneumatic cylinder with cover lid is lowered onto a resting position over the drum for dust containment.
- High flow auger (primary): The material is dosed into the buffer hopper on load cells.
- Precision auger (secondary): The material nears target weight causing the automatic switching from the high flow auger to precision auger for accuracy.
- Target weight is reached, dual screw feeder shuts off.
- The automatic butterfly valve releases the material into the drum below.
- The inflatable seal (or cover lid) releases its connection to the drum.
- The operator signals the control panel to prepare the next drum.
- The turn table rotates the pallet 90° to the second drum position and the next fill sequence repeats the cycle.
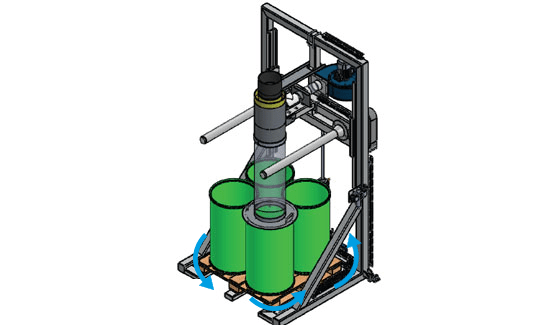
Pallet Turntable Technical Specifications:
- Capacity: 100 kg
- The rotation stroke is activated by air cylinder an electric motor
- Physical barriers are mounted at both ends of the stroke
- Four heavy duty urethane wheels support the turntable rotation
- The surface is a chain driven live roller conveyor
- Welded safety skirt is provided around the perimeter
- All steel heavy duty welded construction
- The complete 90-degree cycle rate is thirty seconds