Processed product: Fish meal
Packaging process optimization
Our client is one of the largest manufacturers of fish meal for the animal feed industry. They have a vertical manufacturing process from fishing to processing, storage and resale. They produce the fish meal in two formats: pellets and meal.
Objectives and challenges:
Our client wanted to optimize their big bag packaging process by increasing the production rate (50 big bags / hour). They were previously using a time consuming and labor-intensive filling method. The big bags were placed manually, by the operator, on the fill chute and held in place by a forklift.
The other challenges involved avoiding excessive levels of dust, preventing poor flow of the product and establishing better safety and ergonomics in their filling process.
Palamatic Process equipment:
Pre-dosing before filling
In order to achieve the desired rate of 50 big bags per hour, two filling stations were installed with each capable of 25 big bags per hour. Prior to filling, the quantity required for a full big bag is dosed into buffer hoppers.
Given the poor flow properties of fishmeal, which tends to have high fat content, two hoppers are positioned in parallel for each station. The work is done in hidden time: while one is filling up, the other is emptying.
Big bag packaging line
After the pre-dosing stage in the hopper, the line consists of a Flowmatic® 03 semi-automatic big bag filling station. The operation cycle is as follows:
- The operator positions the big bag manually
- After tight connection, the powder is emptied
- Closing is done automatically without operator intervention
- A rotating head achieves a centering point on the big bag, an aluminum clamp is placed using a magnetic clamp
- The big bag is released by an automatic hook system
- A conveyor belt automatically sends the big bags to the forklift collection point
- Quality monitoring is provided via the automatic big bag identification drop-off station
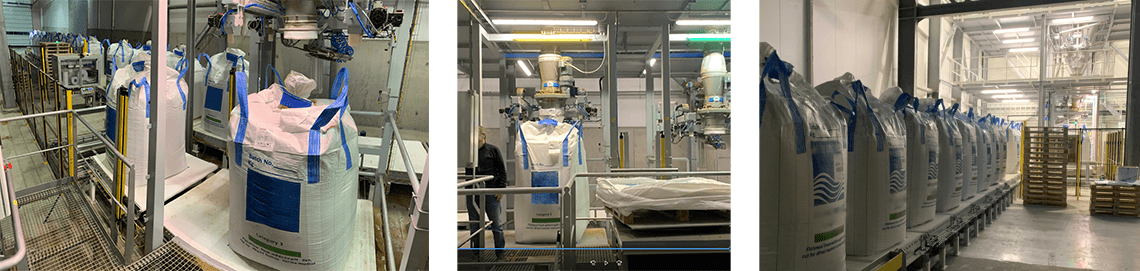
Dust collection system
A dust removal device is integrated with the big bag filling line to prevent the emanation of dust at the level of the weighing hoppers and the filling station. This system also can reclaim some of the material in the filters thanks to reverse pulse jet cleaning, which allows the fishmeal to fall back into the hopper.
Results:
The installation put in place made it possible to achieve the initial objectives, namely:
- Increase production rates
- Improve the safety and ergonomics of operator stations
- Avoid the dispersion of dust
Discover the installation in video: