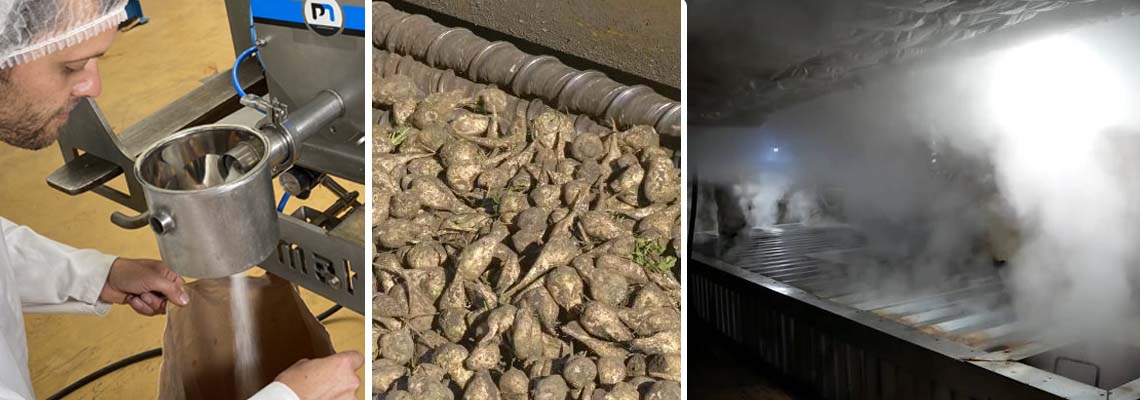
The raw material used by sugar refineries and confectionary manufacturers for the production of sugar (white sugar, brown sugar, sugar cubes, powdered sugar) and molasses will be either sugar cane or sugar beets.
The sugar industry is seasonal in large part due to the timing of the beet harvest taking place during the fall season (September/ October to January). This requires rapid processing of the beets in order to preserve the quality of the sugar. The rest of the year is mainly for cleaning, upkeep and maintenance of the production equipment.
The sugar manufacturing is a heavy industry with occupational hazards. Here we will detail the 5 major risks present in this sector of activity.
1. Machine Hazards
Given the seasonal nature of this industry, the machines dedicated to the sugar extraction or separation process operate continuously (24 hours a day, 7 days a week) throughout the year.
The grinding and cleaning equipment can often generate noise that can exceed 100 dB. This level of noise can be harmful to the health and safety of your operators by causing damage to the hearing system, general discomfort, lack of concentration or be a source of stress.
The industrial equipment used to produce sugar can be the cause of serious accidents (cuts, lacerations, crushing of hands and arms, rolling up of clothing, hair, etc.) due to moving or rotating parts (i.e., centrifuges). In addition, material blockages, jams, adjustments or even cleaning under conveyors with difficult access to dangerous areas, are often the cause of work-related accidents.
2. Biological risks related to dust emission
The accumulation of dust can occur in multiple places and cover equipment surfaces, ducts, work floor, walls of silos, cable trays, pipes, industrial equipment (conveyors, transporters, bagging, filling silos, etc.) but can also spread more widely in the air. Sugar dust can particularly finds its place in nooks and confined places which are difficult to access for cleaning and maintenance necessary for sugar production.
Dust emissions from sugar factories expose workers to biological agents responsible for infectious diseases. This can also cause severe allergic reactions due to their allergenic nature, due to sugar cane molds present at production sites.
3. Combustible Dust Fire and Explosion Hazards
The sugar industry deals with combustible dusts that have the potential to explode or burn.
This is particularly the case for sugar, in dry powder form or the dust waste generated (pulp and bagasse). There is a history of sugar dust causing explosions at production facilities following the heating, sieving, transfer, loading or storage processes in silos. Tragically, in some instances the consequences of these explosions have been fatal.
Some sources of ignition are inside machines or in moving mechanical parts (elevators, hot motor surfaces, presence of foreign bodies generating friction between two parts, etc.) or occur due to faulty electrical equipment. Storing ethanol-based or beet-based alcohol from the fermentation of canned juice or molasses can also cause serious fires or explosions.
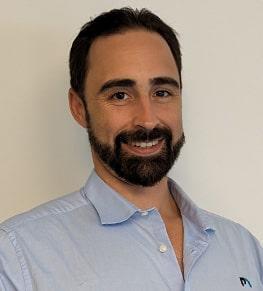
Do you produce sugar and have a handling
project? I am available to discuss the subject.
Tarik, powder expert
An assessment of explosive risks in the sugar industry is therefore essential to better anticipate and prevent them.
4. Chemical and thermal risks
The various sugar manufacturing processes use high temperatures that can cause burns or respiratory problems. The process of cleaning, clarifying, bleaching or disinfecting procedures on equipment, use chemicals – detergents, disinfectants, strippers, etc. – causing significant risks to the health of workers. These include, for example, poisoning, eye or skin burns, allergic reactions, asthma and even carcinogenic risks.
Among the substances responsible for these disorders: phosphoric acid, milk of lime, sodium sulfoxylate, etc.
5. Physical risks
All industries – agri-food, chemicals, construction, energy, etc. – involve physical risks for operators which are linked to the use of additional machines and devices, the layout of workstations or the work environment.
The handling operations are important and require repetitive motions during the packaging of sugar, which can cause occupational injuries in the joints or musculoskeletal disorders (MSDs).
The same applies to the cleaning and disinfection prodedures of the machines and work area, which involve uncomfortable postures or stress on certain limbs (squatting, kneeling, arms outstretched / in the air).
The grinding and grating processes also present dangers in terms of cuts and abrasions with the risk of secondary infection (paronychia).
Finally, the floors and stairs are often wet or slippery in refineries/sugar factories due to liquid spills, the presence of dirt, etc. Workers are therefore exposed to the risk of falls which can be the cause of cuts and sprains.
In order to reduce these occupational risks present in the sugar industry, various preventive measures must be adopted by manufacturers in the sector.
Palamatic has drawn up a general list of preventive measures to be applied in the sugar industry: compliance with health and safety, control of dust emissions, types of suitable equipment, prevention of fires and explosions, ergonomics of personal work places, etc.