Today, the electric vehicle market is experiencing new growth in many countries. This expansion generates a demand for increased production, which integrates chemical materials that are often critical, highly toxic and dangerous for the environment and human health.
In addition to plastic, solvents and electronic components; metals (such as copper, nickel, lithium and cobalt) are used in the composition of the active part of battery cells.
As a result, recycling electric vehicle batteries is both an ecological and a strategic necessity. The treatment of hazardous waste and recycling various materials must preserve the resources necessary for ecological transformation.
Recycling activities have serious environmental benefits: first, they reduce carbon emissions by one ton of CO2 equivalent per ton of batteries recycled and second, they avoid the extraction of virgin metals and mining activities that have critical impacts on biodiversity and water resources.
1. What is black mass?
Batteries: alkaline batteries, lithium batteries, saline batteries (rechargeable or not), must be sorted, dismantled, crushed and separated once used. Plastics and metals will be separated and then crushed, ready to be recycled in other processes.
Black mass is an active powder containing a mixture of cathode and anode materials. It is made up of many metals such as copper, manganese, cadmium, lithium, cobalt, etc., and contains recoverable metal oxides. The objective is to separate each metal from this mass and remove toxins from the material to avoid contaminating the metals. The purer the metal, the better it can be recycled.
2 Techniques:
- Pyrometallurgy (or thermal industry) - This technique is suitable for the majority of batteries and accumulators.
- Hydrometallurgy - Saline, alkaline, zinc-air and lithium batteries are concerned in this process, making it possible to upgrade zinc and manganese.
2. The role of black mass in the battery recycling process
Battery recycling allows the use of secondary raw materials obtained from waste, which in some cases can be reintroduced into the production process or used to manufacture other products.
The ideal is closed-loop recycling (upcycling), which represents a true circular economy.
These different transformation phases involve the handling and processing of many toxic powder products making up the blackmass.
The black mass is generally stored in bulk bags. Bulk bag unloading solutions should be considered to empty super sacks safely and to supply, for example, a powder storage hopper or other production equipment.
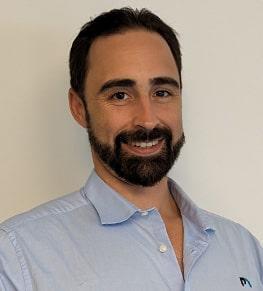
Do you have a black mass handling project?
I am available to discuss the subject.
Tarik, powder expert
3. The technical characteristics of black mass
Black mass is a highly toxic powder (CMR risk). Equipment dealing with black mass on a production line must be adapted to this difficult material as the particles are very fine and volatile. When it comes to unloading, transferring and loading black mass, the equipment must be designed to avoid any dust emissions into the atmosphere to protect operators against the risk of contamination. The containment of the installation is therefore of great importance in the treatment of this toxic powder. Equipment such as industrial dust collection systems or confined bulk bag emptying stations are often recommended. For example, the installation of a glove box allows the operator to open the bulk bag in complete safety without coming into contact with toxic CMR products. The glove box will allow the user to undo the discharge spout of the bulk bag for unloading of the bulk material.
When dry black mass does not flow easily down an angled slope, it can also present discharge problems inside a hopper, for example. Flow aid equipment can then be used, such as flat-bottomed bridging devices, providing the mechanical effort necessary to move the material.
The solid particles are not homogeneous with regard to the shape of the crystals. The metal oxides and the graphite are rather spherical particles while the particles of pure metal resemble a flat surface. As a result, the heaviest particles settle faster than the others. Graphite particles tend to agglomerate on the surface of the liquid inside a stirred tank, for example.
4. Pulping process
The black mass is often transferred from a hopper to a repulping tank in "continuous feed" mode. A device for measuring the weight and/or the flow rate of this black mass is often included with the dosing system, which is located upstream of the pulping tank (at the outlet of the pneumatic transfer cyclone).
The particles are generally hydrophobic and appear dry even after light mixing with water. However, there can still be clogging issues when the black mass gets wet. It is important that this powder is not in contact with humidity to avoid any risk of clogging before the pulping phase.
A liquid (water or equivalent) is continuously added to the top of the pulping tank, and the flow rate is automatically adjusted to control the solids content. The sludge then overflows by gravity into a reactor placed under the repulping tank.