Description
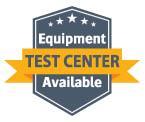
Bulk bag unloading station - EASYFLOW OPERATOR SAFETY
BULK BAG GLOVE BOX
Total containment and operator safety
The bulk bag unloader station equipped with a glove box allows operators to handle toxic products without coming into contact with them. Thanks to the bulk bag glove box, the operator can easily access the bulk bag spout to untie it and allow the material to be emptied with no risk of direct exposure.
Rate: 10 bulk bags/hr.
Capacity: 2 tons/bulk bag
Objectives: dust containment & flexibility of bulk bag dimensions
The bulk bags unloading station equipped with a glove box allows safe toxic material handling by containing dust and avoiding direct operator exposure.
The Palamatic Process dust-tight bulk bag emptying station is the ideal solution for the handling of toxic chemicals and contaminants. The stations can be fabricated in painted carbon steel, hot-dip galvanized steel, 304L stainless steel, or 316L stainless steel. There are three main designs in order to facilitate the installation of the bulk bag on the discharge station: a forklift truck, an electric hoist, or a low structure.
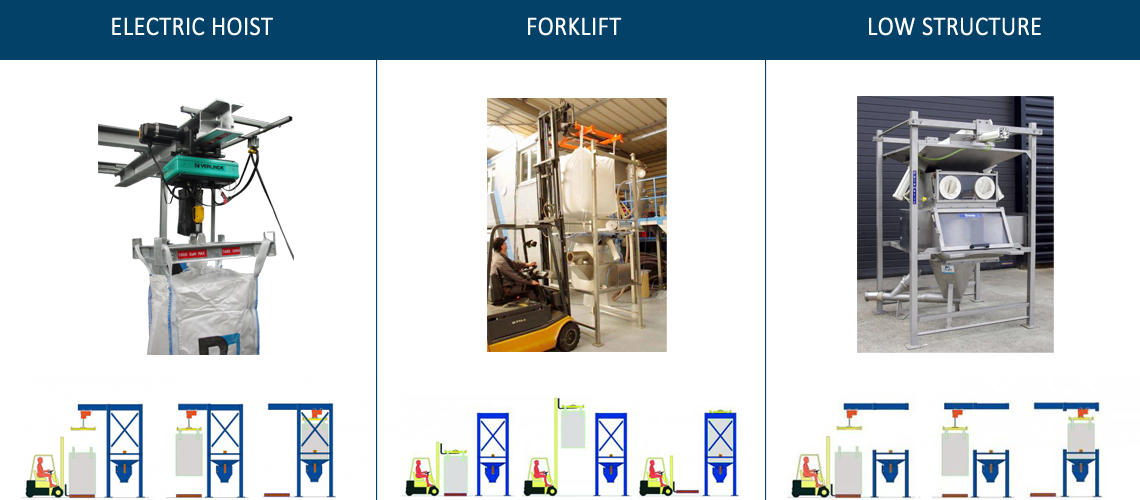
Customized bulk bag emptying stations: flow and containment
The Palamatic Process engineering office can offer you custom solutions adapted to your process requirements after a careful review of your specifications.
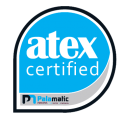
Built-in features:
• Automatic cutting of bulk bags
• Total material containment
• Extraction of difficult bulk solids
• Reduced installation height
• Operator safety and healthy work environment
• Empty bulk bag compactor
• Hazardous area rated
-
Rate2
-
Automation1
Equipment advantages
- Material containment and protection of the operator
- Flow control
- Flow aid
- Connection to dust filtration equipment
Media
View our equipment in photos
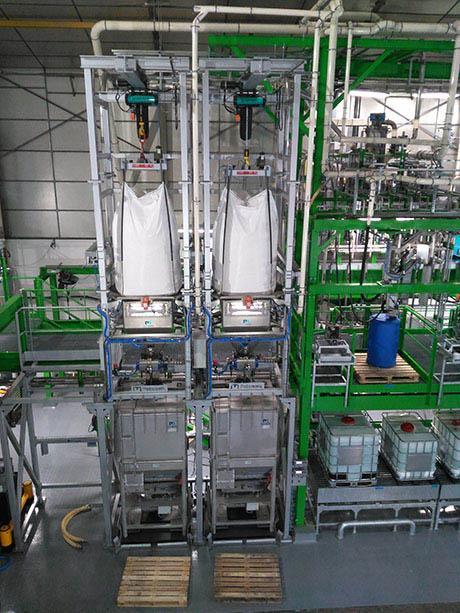
Dust tight big bag discharger
The contents of the 3 bulk bag unloading systems are reconditioned in stainless steel containers.
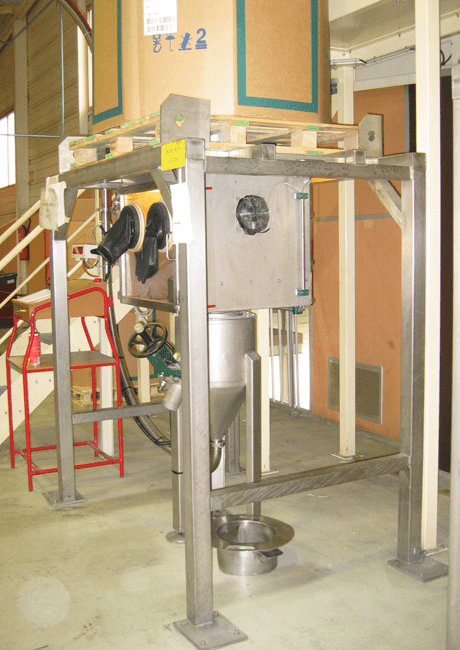
Big bag discharging - Glove box
Liquid formulation:
- 3 big bag dischargers for 7 types of bulk materials.
- 3 re-packing and un-packing stations for stainless steel containers.
- 2 pneumatic conveyors feeding 2 reactors.
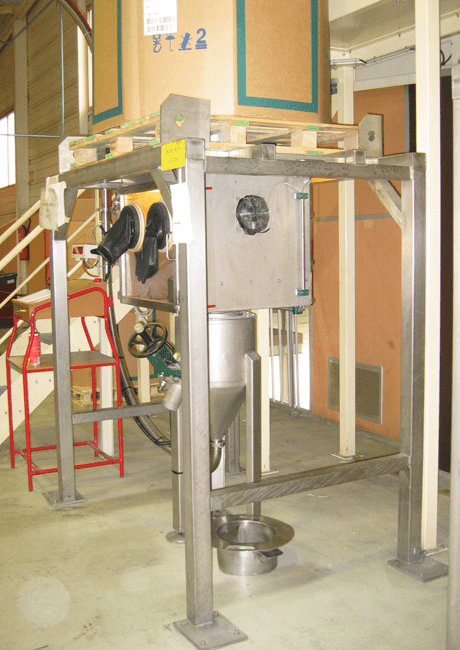
Bulk bag discharging - Glove box
The customer's requirements for this process specifically relate to containment during deconditioning.
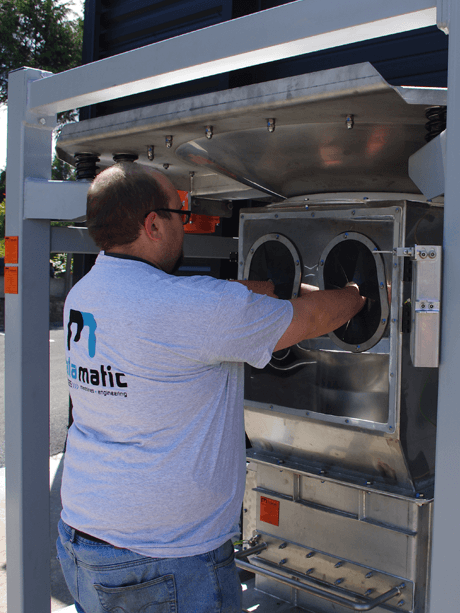
Jumbo bag - Dust containment enclosure
The dust containment enclosure prevents the operator from coming into contact with the discharged bulk material while maintaining a good visibility.

Big bag discharger glove box
This installation includes 3 big bag discharging stations for 7 types of materials
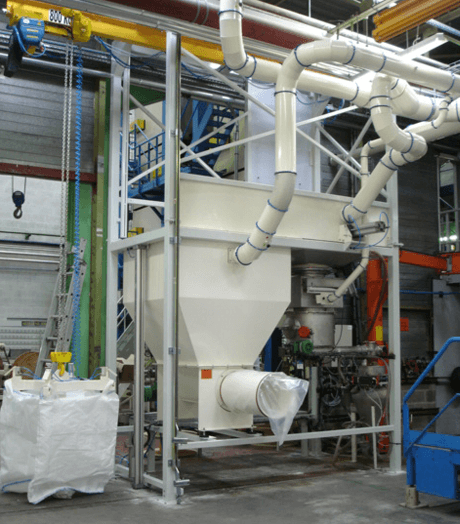
Big bag discharging system - Glove box
Big bag discharging system - Glove box. Electric hoist loading. A big bag compactor is integrated into the emptying system.
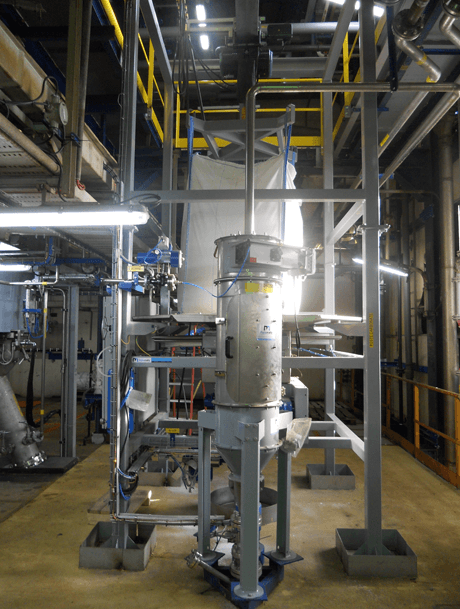
Industrial dust collection powder handling
This machine is designed for the manual opening of all types of big bags, limiting dust emissions as much as possible and facilitating the flow of the bulk material. The big bag is installed using an electric hoist.
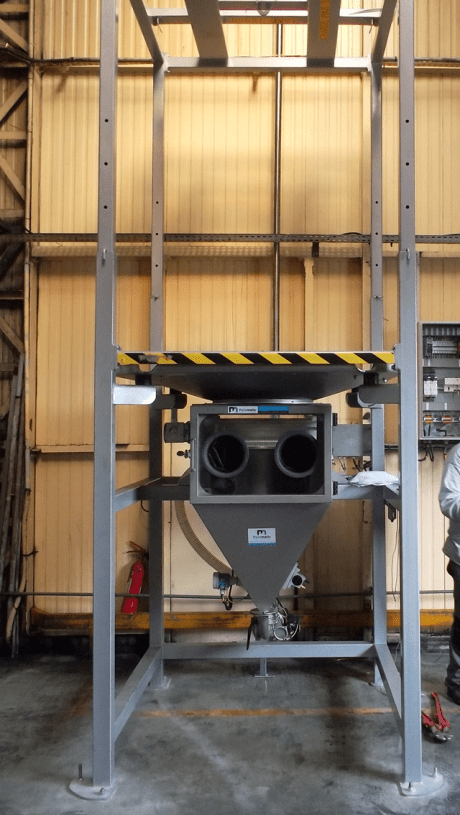
Big bag unloader
The dust containment enclosure with its dust-tight door provides safe and ergonomic access to the big bag discharge spout.
Features
Technical specification
Rate | 10 bulk bags/h. |
---|---|
Manufacturing materials | Painted steel, 304L stainless steel, 306L |
Finishing touches | RAL 9006, micro-blasted, electropolishing |
Installed power | 0.1 kW (depending on option) |
Compressed air consumption | |
Operating pressure | 6 bar |
Required dust removal rate | 1,000 m³/h. |
Maximum size of big bags (length x width x height) | 1,200 * 1,200 * 2,400 mm |
Entrance | |
TOR input | Depending on the option |
TOR output |
Depending on the option |
Integrated systems:
- Low structure
- Lump breaker (optional)
- Connecting tube
- Bulk bag/glove box
- Vibrating motor
- Bulk bag removal tray
Options
Case studies
CASE STUDIES WITH THIS EQUIPMENT
Gelatin for capsules
Processed materials: pork gelatin, fish gelatin, bovine gelatin, for capsules coating gelatin for capsules - Gelatin for capsules - This company acting in the pharmaceutical sector is one of the world...Fine chemical
Black mass treatment process
Treated powder: black mass - Black mass treatment process - Process to unload the black mass from bulk bags, precisely dose and repulp it with water, without clogging reactions or dust emissions from...Energy
Bucket filling line
Material: Graphite - Bucket filling line - Turnkey solution for bulk bag emptying, total containment and rapid filling of buckets with graphite powder.Chemical