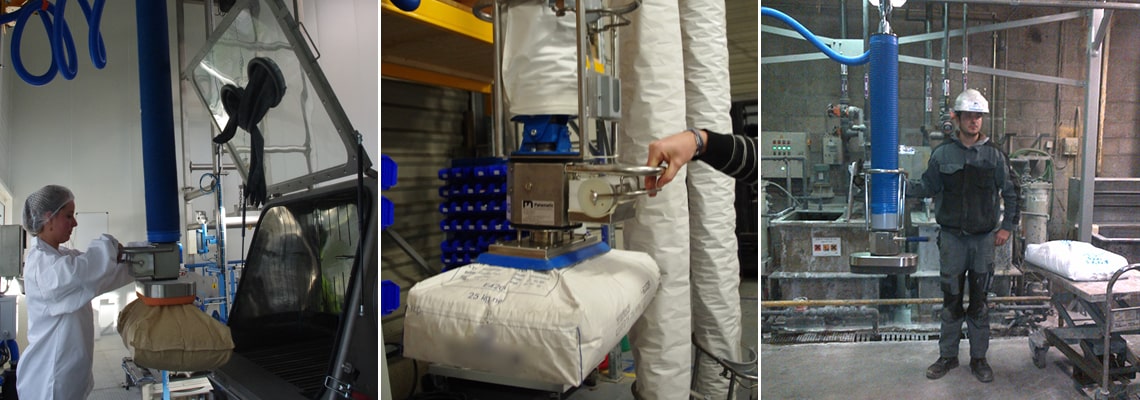
Improving safe work practices and reduce the chances of operator injuries from repetitive, heavy lifting.
Floor operators on a production line often face the daily challenge of lifting and loading heavy sacks of dry materials. Even when proper lifting techniques are used, the daily strain of lifting sacks of powders can take its toll on the human body over time. In November of 2020, the Bureau of Labor Statistics released the latest numbers in work place injuries for the 2019 calendar year. In that report the agency states, “Injuries and illnesses to manufacturing workers resulted in 32,470 DAFW cases of sprains, strains, or tears (28.0 percent); 16,790 cases of soreness or pain (14.5 percent); and 15,380 cases involving cuts, lacerations, or punctures (13.3 percent).”[1]
Repetitive, heavy lifting can sometimes result in these types of injuries to the neck, shoulders and lower back. These injuries can range in severity from minor strains to serious tears that require weeks, if not months of rehabilitation. Manually lifting and unloading heavy bags of powder and bulk solids is a common practice for many production facilities.
Bags of powder can vary in weight, but commonly fall between 25 – 75 lbs each. Manually depalletizing a stack of these bags everyday day will eventually result in operators suffering from strains and injuries. Considering the current economic climate of labor and material shortages, the last thing a manufacturer can afford is losing operators to work-related injuries. Furthermore, production facilities have an obligation to take every measure they can to protect their personal and minimize all risks of injury.
In order to prevent operator injury, employees should use smart lifting practices that will reduce the risk of muscle pulls, wrist injuries, elbow injuries, spinal injuries, back sprains and other injuries caused by lifting heavy objects.
[1] EMPLOYER-REPORTED WORKPLACE INJURIES AND ILLNESSES – 2019 https://stats.bls.gov/news.release/archives/osh_11042020.pdf
1. Prepare
Before you lift, think and plan out how it should be done:
- How heavy/awkward is the bag? Should I use mechanical means (e.g., a hand truck or sack vacuum lifter) or another person to help me with this lift?
- Where do I need to place the bag (e.g., bag dump station or sack tip tray)? Is the path clear of obstructions, stairs, and other interference?
- Do I need gloves or other personal protective equipment? Should another person help me with the bag or sack?
2. Lift
Stand close to the bag and keep your elbows and arms close to your body. Keep your back straight while lifting and bend at the knees. Try keeping the bag close and centered in front of you while looking up and ahead. Get a firm grip established and do not twist while lifting. Do not make fast or sudden movements; use a smooth motion while lifting. If the load is too heavy, find someone to help you with the lift.
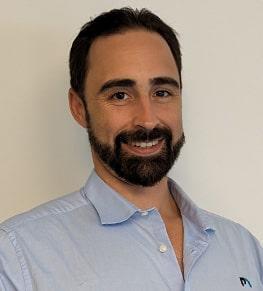
Do you need personal advice on sack lifting units?
I am at your disposal.
Tarik, powder expert
3. Carry
Do not twist your body; instead, pivot your feet in order to turn. Your hips, shoulders, toes, and knees should all face the same direction. Keep the load close to your body with your elbows close to your sides. If you get tired, set the bag down and rest for a few minutes. Don’t let yourself get so tired that you cannot properly set down or lift the bag or sack.
4. Release
Lower and place the bulk material bag down the same way you picked it up, just in reverse order. Bend with the knees, not with the hips. Keep your head up and do not twist your body. Keep the bag as close to the body as possible. Wait until the bag is secure to release your hold.
The Palamatic Process Solution – Reduce the Risk of Lifting Injuries
Our staff has extensive experience in bulk material handling solutions. One such solution is our Sack Manipulator Manis 160-1700. This bulk material handling equipment offers superior sack lifting capabilities with minimal worker effort. Operating off the principal of vacuum suction, the boot of the bag lifter can easily and gently adhere itself to paper, plastic and poly-woven sacks up to 175 lbs in weight. The vacuum lifter setup is rather simple and easy to use. A vacuum pump is connected to a hose mounted to a jib crane. At the end of the crane is an extendable and retractable lifting hose. A suction boot with simple controls completes the bulk handling systems and allows the operator to control the intensity of the vacuum for lifting and lowering the packages.
The vacuum sack handler can be modified to work best in your process line.
Examples of installations include:
- Rotating post on a mounted jib crane
- Inverted rotating post on jib crane (lower height requirements)
- Mounting for support structures (ceiling or support beams)
- Fixed columns to support lift equipment over a larger area
- Telescoping beams to reach areas with limited access
Vacuum lifting systems are designed to make repetitive lifting of heavy loads easy and ergonomic, eliminating strain and muscle fatigue. The lift and lower controls are simple enough to use with one hand, and almost all the weight of the load is carried by the suction of the vacuum pump. Industrial manipulators are easy to use, install and can prevent operator strain and injury with a minimal investment.
Since 1992, Palamatic Process has provided bulk process equipment to over 2000+ installations in more 30 countries. We offer knowledge and expertise in all manner of powder handling solutions.