A compound is a ready-to-use colored and/or additive pellet.
Compounding is an extrusion and granulation process that produces a plastic material whose characteristics are modified. The compounder formulates and manufactures the color and performance characteristics from a wide range of polymers and additives, and produces a compound adapted to the requirements of the finished product.
1. Formulation
The formulation must take into account several parameters during the development process before being produced in the form of powder or pellets.
Color, aesthetics and technical characteristics such as elasticity, rigidity, impact resistance, resistance to chemical substances, resistance to light and thermal variations, are parameters to be taken into account.
2. The extrusion process
The techniques used by compound manufacturers make it possible to offer two types of semi-finished products: powder (dry-blend) and pellets (compounds).
The dry-blend process consists of introducing the various components into a mixer at a previously determined temperature and paddle speed (RPM).
The compounds are produced by the extrusion-granulation technique. The prepared mixture (dry-blend) is transferred to an extruder which softens and compresses the material, pushing it towards the outlet die. The small “noodles” formed are then repeatedly cut to product the pellets, which are cooled before conditioning. The pellets can be packed in bulk in 25 kg plastic bags or in 1 ton bulk bags and gaylors, which are transferred on pallets.
For very large quantities, the automatic feeding of the machines can be done from a silo.
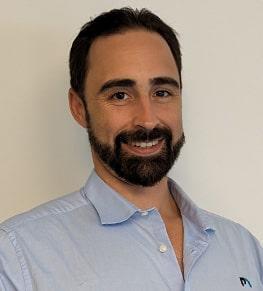
You work in the compound sector and have a handling project?
I am available to discuss the subject.
Tarik, powder expert
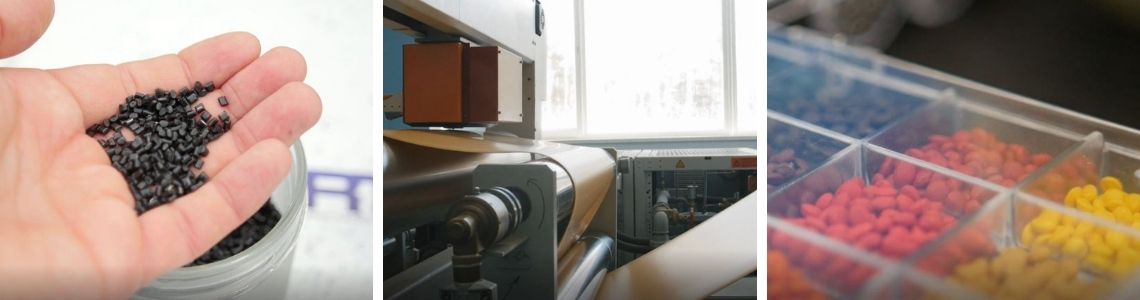
3. Other processes complementary to extrusion and their applications
Compounding is not limited to the extrusion technology described above. Other transformation techniques can be used for the manufacture of various parts.
- Fluidization
A preheated support is introduced into a tank where the powder is kept in suspension by forced air. Under the effect of heat, the plastic material covers the mesh screen with a thin and uniform layer.
- Injection
Injection molding is carried out by introducing the compound under pressure, previously heated and kneaded, into the cavity of a mold which defines the shape of the finished object, for example, bottle caps.
- Thermoforming
Consists of manufacturing elements from extruded plastic material in wire, sheet or plate. The starting material, whatever its presentation, is heated and then shaped on a mold by vacuum or air pressure. The part produced is kept pressed against the mold during the cooling phase which helps retain the shape.
- Blow molding
Consists of introducing extruded material into a mold and blowing air into it to shape the material to the mold. This is the main manufacturing process for hollow bodies such as bottles, for example.
- Rotational molding
This type of transformation is similar to extrusion-blow molding but requires the use of powder compositions (dry-blend). This method makes it possible to manufacture large volumes of finished products.