Description
Bulk bag filler - Hygienic packing without pallets and automatic gross weighting
The FlowMatic® 04 H bulk bag filling equipment makes it possible to fill big bags in a critical area (white zone) for industrial companies filling bulk materials with high hygienic value. Manufacturers using the FlowMatic® 04 H are mainly manufacturers of dairy products or food supplements. The objective of this packaging line is to avoid any wooden pallets in the product area. However, at the end of the packaging line, the super sack is placed on its wooden pallet via a docking system installed outside the filling area.
The FlowMatic® 04 H filling machine integrates all the necessary solutions for the automatic packaging of bulk bags, namely: dosing unit, filling tube with inflatable containment seal, big bag shaping system, product densification by vibrating table, dust removal, weighing in legal metrology and bulk bag conveying and palletizing systems.
The palletization of the bulk bag is carried out by a two-level conveyor: a belt conveyor for the bulk bag and a roller conveyor for the pallet. The stacked and synchronised conveyors ensure that the bulk bag is placed on the pallet outside the packing area. Beforehand, the pallet is lined with an interlayer.
Usually, these hygienic packaging lines integrate magnetic detectors and samplers.
For industrials requiring even more stringent hygiene constraints, PALAMATIC PROCESS has developed a FlowMatic® 10 bulk bag filling system that ensures pallet-free filling and handling of the bulk bag by a suspended system that avoids any ground equipment.
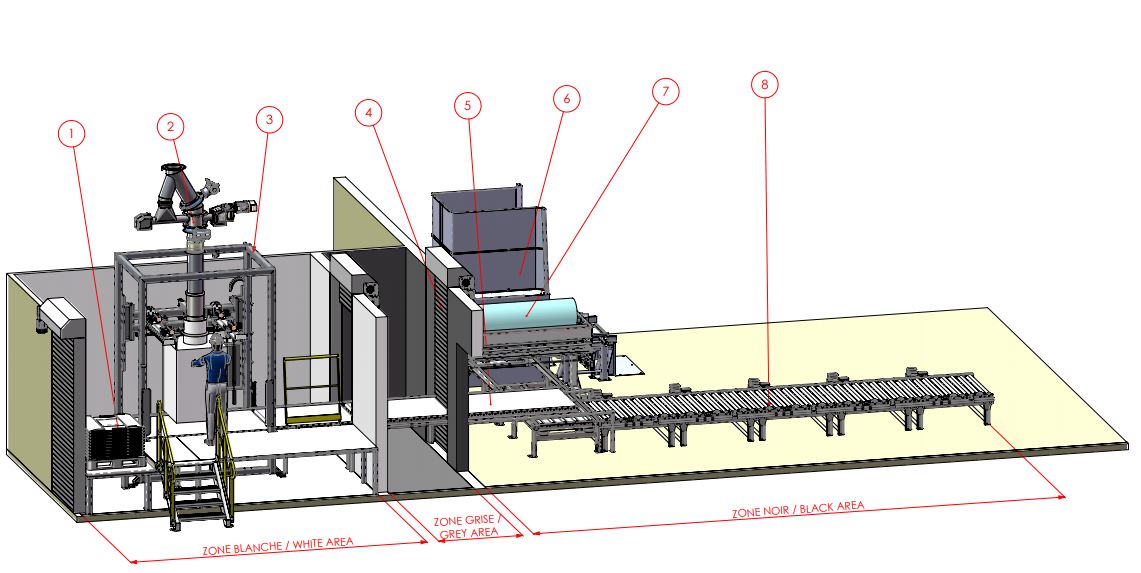
Operating mode:
1. Placing the bulk bag on the station via the rotating head
2. Sealed fastening of the spout by inflatable seal
3. Tensioning of the bulk bag by pneumatic jack
4. Inflating the bulk bag for preforming
5. Switching from the inflation system to the dust collector
6. Start filling high flow rate
7. Vibration of the densification table with intermittent operation
8. Weighing management with a low speed shift to adjust the dosage
9. End of filling: descent of the filling head, deflation of the seal and automatic unhooking of the bulk bag loops
10. Closing the bulk bag by sealing the bag
11. Automatic removal of the bulk bag via the hygienic belt conveyor to the pallet docking area
12. Placing a layer pad on the wooden pallet or removing a placemat (operation carried out in the storage area)
13. Placing the pallet via the roller conveyor under the bulk bag conveyor belt
14. Synchronisation of the belt and roller conveyors for docking the bulk bag on its wooden pallet. The bulk bag is deposited on the pallet by the simultaneous advance of the conveyors.
15. Film packaging machine, bulk bag and pallet wrapping machine (optional).

-
Automation1
Media
View our equipment in photos
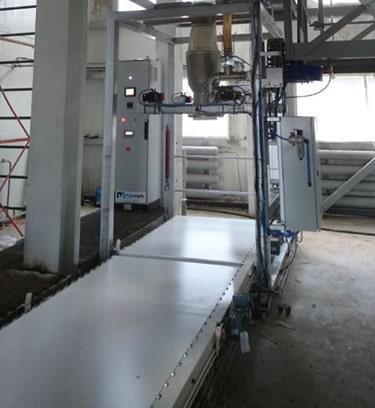
FlowMatic® 04 H Palamatic Process
FlowMatic® 04 H bulk bag packing station being installed before the packing cabin is set up. Bulk bag handling is ensured by a belt conveyor.
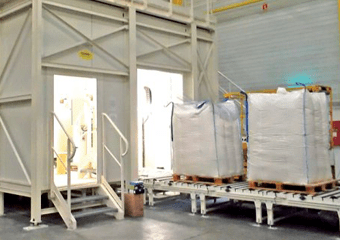
Bulk bag output area
An special area (grey zone) closed by two hermetic doors provides a link between the two zones and avoids the introduction of pallets in sensitive areas.
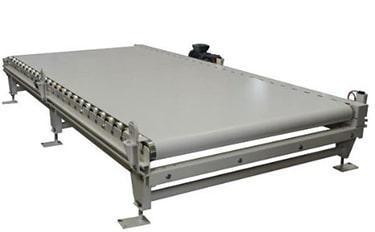
Belt conveyor
Belt conveyor for handling filled bulk bags without pallets and in hygienic area (called "white zone" or "red zone").
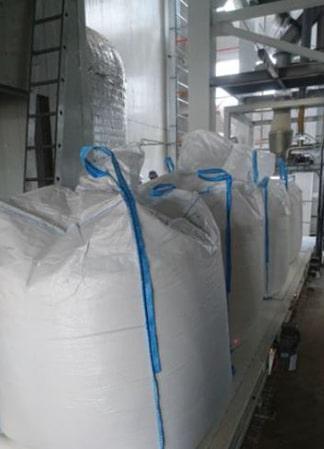
Big bag packing line
Once packed, the bulk bag is placed on the pallet and evacuated by a motorized roller conveyor, thus optimizing the rate of the bulk bag packing line.
Features
Technical specification
Rate | 20 to 30 bulk bags/h. |
---|---|
Capacity | 2 tons/bulk bag |
Manufacturing materials | Painted steel, 304L stainless steel |
Installed power | 8.7 kW |
Compressed air consumption | 6.8 Nm³/h. |
Dust removal rate | 300 m³/h. |
Conveyor for pallets | Rollers |
Conveyor for bulk bags | Belt |
Equipment integrated in the FlowMatic® 04 H model:
White zone:
- Filling head
- Weighing frame
- Bulk bag liner welding system
- Belt conveyor
Grey area:
- SAS bulk bag extraction by sliding door and quick lift door with conveyor belt
Storage area:
- Unstacker
- Placemat / divider removal on pallet
- Bulk bag and pallet docking area
- Buffer storage area for bulk bags packed and placed on wooden pallets