Our clients project involves the construction of a new plant capable of producing several qualities of POLYESTER. The final products will be in solid and liquid forms on a SEVESO classified site.
This manufacturing process involves a mixture of liquids and solids heated in a reactor.
The solids are delivered in the form of 1000 kg bulk bags and 25 kg sacks, unloaded and stored in a weighed buffer hopper for accurate dosing.
The characteristics of the different materials vary, such as: powders, crystals, scales and petals.
Terephthalic acid, Isophthalic acid, Adipic acid, Sebacic acid (crystals), Azelaic acid (scales), Dimethyl terephthalate (DMT) (petals).
All the preparation of powdered raw materials is done upstream in the buffer hopper, which collects the bulk recipes, and production is done in batches.
Some materials can be packaged in sacks, which is why the stands are equipped with a bag dump station. The introduced quantity is then managed by the operator (bag weight or pre-weighing).
A pneumatic transport, positioned under the bag dump, transfers the materials to this loading hopper located above the reactor. The transfer is carried out at a rate of 24 m³/hr. To ensure the Atex safety of the loading line, all storage and loading is done through a closed circuit, under nitrogen, in order to remain under 5% oxygen.
The different polyester recipes, the types and quantities of integrated solids, are variable and can be introduced several times (load). Therefore, the hopper is on load cells for weighing and dosing functionality.
The hopper has a volume of 24 m³ and a reactor loading capacity at a flow rate of 5 t/hr.
The reactor is fed from the hopper by means of a screw conveyor and rotary airlock valve.
The reactor is equipped with a heated double jacket ensuring the melting of the powders and resin scales.
The bulk bag and sack unloading stands are equipped with a containment system connected to a local dust collector. These dust removal filters are deported and all filters are unclogged with nitrogen pulses. The lower cone of the reactor loading hopper is also equipped with a nitrogen unclogging system, providing fluidization and the inerting process. The hopper is also equipped with an automatic cleaning head filter.
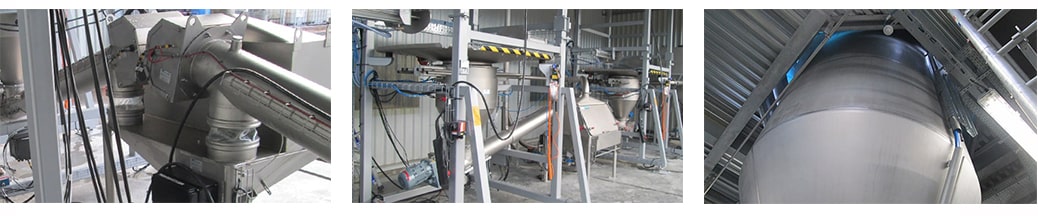
Simplified operating mode:
- A type of product to be manufactured is defined (recipe), this recipe is detailed in quantity and type of solid raw material to be introduced (several types of material possible in several charges)
- A screen interface indicates to operators which material in which quantity.
- The operator programs the weighing unit of a bulk bag emptying stand to indicate the quantity to introduce (e.g., 8500 kg).
- The two bulk bag unloading stands work alternately, one emptying while the operator installs a bulk bag on the other super sack cracking station.
- When the unloading cycle is finished, the operator enters the exact quantity introduced into the screen interface.
- When the charge is complete, the hopper is emptied into the reactor and a new charge can be prepared.
- Unloading into the reactor is carried out in small rotational sequences of the metering system, depending on the state of the mixture in the reactor.
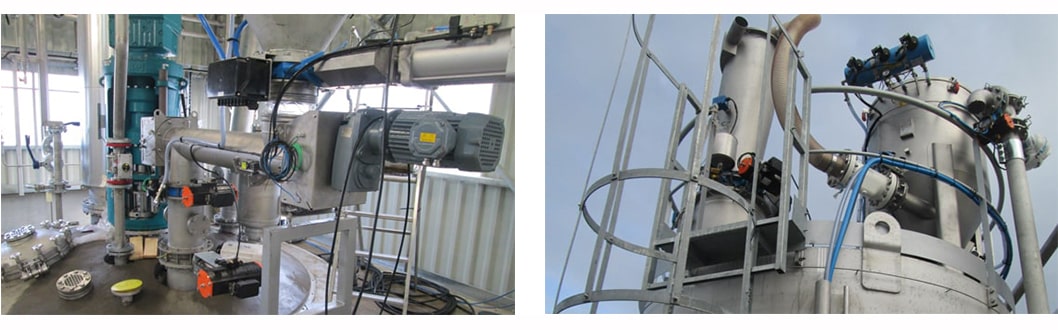
Palamatic Process has developed a turnkey process line for reactor loading for chemical manufacturers, just like this customer achievement.