Processed powder: chromium powder
Drum and bulk bag loading
Our client is a leading company in metal manufacturing and fabrication.
The chromium powder is stored in containers (IBC) which are emptied into a collection hopper.
The objective is to screen and package the bulk material in super sacks or 55 gallon drums with an integrated feeding system. The production rate of the installation is 20 tons/hr.
The equipment includes an IBC unloading system which loads the industrial container using an electric hoist. The storage container unloading station is equipped with centering devices to optimize its installation and improve operator ergonomics. The connection with the container is made by a socket gasket to optimize dust containment. Once the container is installed on the bulk unloading station, the operator will manually open the drain valve, allowing the chromium powder to flow into a collection hopper. This hopper feeds a vibrating conveyor which provides the dosing and material transfer of the chromium powder to a vibrating screen. At the outlet of the sieve, the powder is packaged in bulk bags or drums.
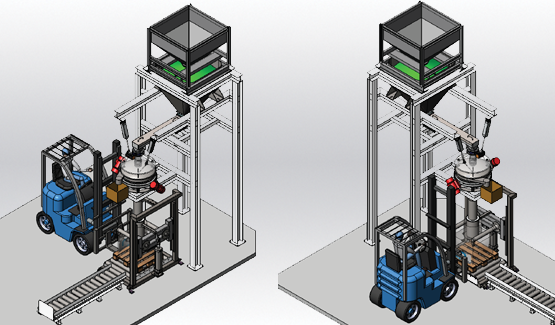
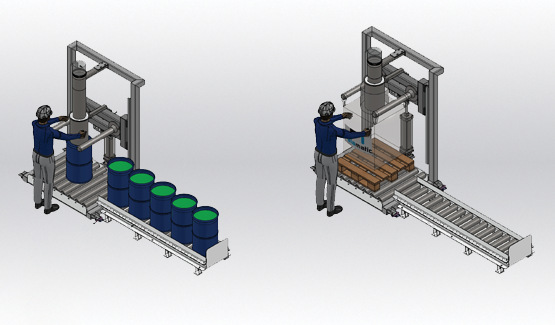
Palamatic Process has designed a packaging station for big bags and drums. This machine is used for filling big bags and drums, limiting dust emissions as much as possible and facilitating the flow of the material. An automatic big bag tensioning system ensures optimum filling and excellent stability of the big bag on its pallet.
The FlowMatic® 02 filling machine includes 2 parts. The first is the filling station for big bags and drums. The second is a movable part for the accumulation of drums.
The filling of the big bags is perfectly airtight thanks to the filling head allowing a strap connection. Indeed, a leather strap is used to tighten the big bag cuff on the filling pipe.
At the end of the filling process, the drums are removed on the roller conveyor. The roller accumulation conveyor can handle up to 2 industrial drums. Big bags are evacuated by forklift truck or pallet truck.