Processed bulk material: infant milk powder
Infant formula powder preparation
Our client is a company that specializes in baby food production.
The process consist of conditioning infant formula powder in various container types: boxes, sacks and bulk bags.
Bulk Bag Unloading - EasyFlow® EF0
Six bulk bags unloading stations and one manual bag dump station - Sacktip® SH are integrated with load cells which allows the operator to meter milk powder into a vertical ribbon mixer.
The manual sack tip tray allows the feeding of ingredients into the mixer through a vibratory conveyor.
The discontinuous vertical ribbon mixer possesses a precision of ±200gr per batch.
In order to meet the strict hygienic requirements of this process, all contact surfaces and welds are grounded smooth and polished in the vertical ribbon mixer, preventing any cracks and crevices that could be material trap points.
The powder is then discharged through a screener connected via a flexible fitting for overall quality control of the final product.
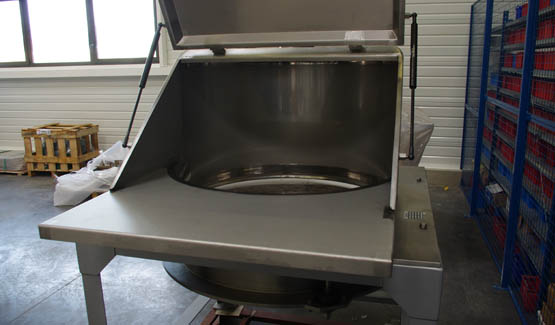
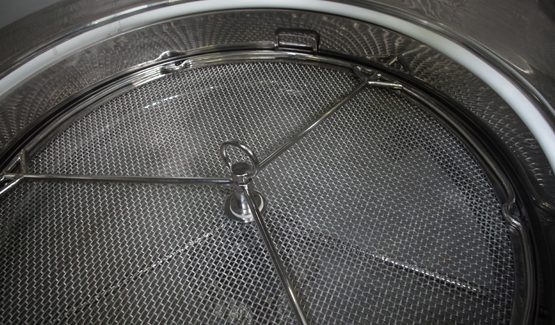
Screener
The vibrating screener provides control and protection of your production line. It is equipped with a metal detector and overs reject outlet. The sieve produces a clean product with no lumps and also captures tramp material in order to protect the milk production line from any mechanical damage. Therefore the final product is of high quality by eliminating agglomerates and foreign detritus.
In order to meet sanitary restrictions the vibratory screener does not have any areas of retention, and the flange assembly allows easy mounting and dismantling.
The Palamatic Process vibrating screener can be used both in gravity feed and pneumatic conveying applications.
End of packaging line
The packaging phase in boxes, sacks and bulk bags is integrated in an atmosphere controlled by a vaccuum system with nitrogen injection.
Capacity per batch: 1,500 liters (with potential to increase production)
Flow rate: 8 batches/hr.
Main advantages :
- Easy clean
- Low energy consumption
- Waste water treatment
- Compact design