Processed powder: Icing sugar
Line for biscuit factory
Food manufacturer that specializes in biscuits, chocolate and cocoa powder.
The customer's process requirements involved the milling of granulated sugar to produce icing grade sugar. The icing sugar would then be suitable for use in chocolate pastes and icing. A secondary purpose of the powder mill is to improve the flow characteristics of the sugar and avoid agglomeration without the need for additional additives.
Bag dump station with integrated vibratory screener
The process starts with unpacking sacks of granulated sugar to feed into the production process line. The operator lifts the bags using a vacuum bag manipulator and places them inside our Sacktip® SH bag dump station with integrated screener. The bag is positioned on the safety grid above the powder discharge hopper and manually opened using a cutting tool. The bag is emptied of the granulated sugar and introduced to the next step in the process.
An integrated vibratory screen in the SACKTIP® manual bag emptying station protects the production line against foreign contaminants. The vibrating sieve ensures good quality control of the final packaged material and protects the pin mill during operation.
This custom-made industrial screener controls impurities and allows the operator flexibility to change mesh sizes. A vibrating motor improves the amplitude and intensity of the screening action. The vibrating screener can be adjusted according to the flow characteristics of the material and the mesh size of the screen.
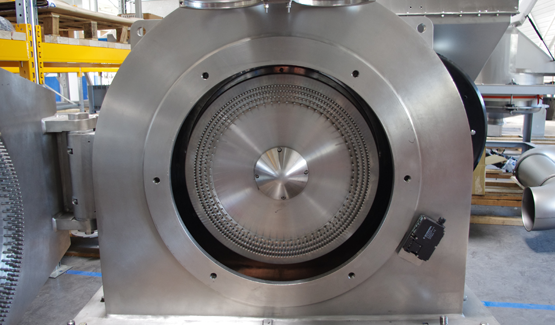
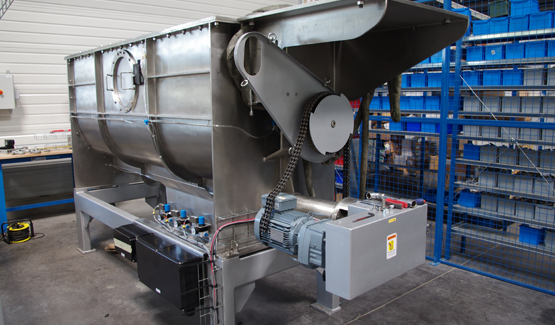
Tubular screw conveyor:
The tubular screw conveyor transfers the material from the Sacktip® SH manual bag dump station to the industrial pin mill. The purpose of the tubular screw is to maintain a continuous rate into the mill system and ensure smooth and steady operation.
Sugar milling :
Data :
- Rotational speed: 6,000 rpm.
- Input grain size: crystal sugar n°2
- Output grain size: D90 <100µm SPAN 6
- Capacity: 2.5 t./h.
- Atex 20 inside/22 outside
The Poly-Mill industrial pin mill offers excellent reliability and performance for fine grinding applications. It is fed at a controlled rate by the tubular screw conveyor. Designed with robust and high resistance mechanics, the pin mill offers efficient and safe operation, as well as easy maintenance and cleaning. Due to the design of the industrial pin mill, there is no risk of cross-contamination with proper maintenance and cleaning practices. A rotary airlock valve positioned above and below the industrial grinding mill allows steady sugar dosage to the downstream process. The rotary airlock valves further contributes to a steady and controlled feed rate of the mill from the tubular screw.
A threshing hopper is integrated post-mill to allow the icing sugar time to cool and avoid caking issues.
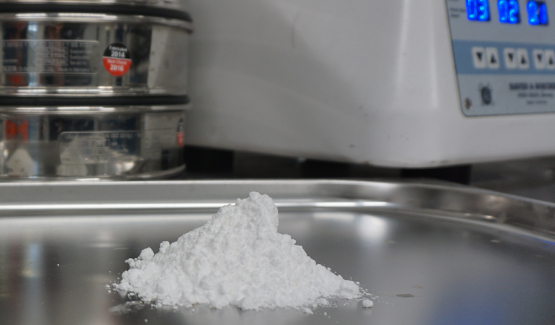
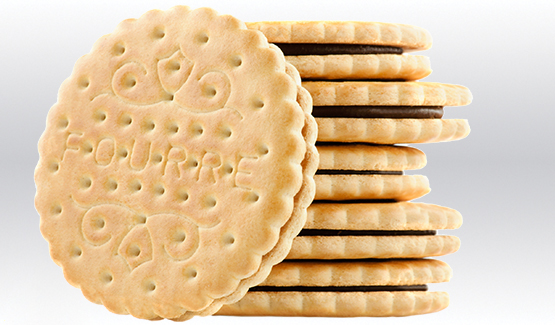
Bagging machine:
The grinding pin mill is positioned above a second tubular screw conveyor. This conveying screw is responsible for the dispensing that feeds two bag filling inlets. The PalSack® bag filling stations operate via gravity flow. The operator positions the bag between the inflatable seal and the clamping ring, which guarantees optimum dust containment. Pneumatic controls inflate the seal, locking the bag and sealing it against the clamping ring. Once sealed, the bag is then filled with the icing sugar. A weighing tray located below the bag allows control of the appropriate dosing amount. Once the target weight is reached the bag filling process stops.
A hopper venting filter completes the final part of this installation. The integration of a venting filter in this sugar processing line prevents pressure build-up in the equipment, maintaining contaiment over fine dust particulates.
The equipment is supplied with a complete electrical cabinet, including motor protection and necessary control functionality.