Semi-automatic ingredient dosing unit
The DosingMatic® Hopper unit prepares and balances all your ingredients in weigh-ins. The dosing carousel prepares ingredients in a mobile weighing hopper or preparation buckets.
Weighing cells incorporate a buffer volume ranging from 50 to 300 litres depending on your material consumption.
The amount of ingredients stored is 10 to 40 cells.
- Compact solution
- Storage buffer based on your material consumption
- Weighing accuracy of all your ingredients
- Short cycle time
The preparation of ingredients is a tedious but crucial step for the quality of the finished product. Palamatic DosingMatic® Hopper automatically prepares your ingredients by weighing in a mobile buffer hopper.
Range and accuracy of weighings type 1 | < to 1 Kg, precision +/- 2g - +/- 0,5% |
Range and accuracy of weighings type 2 | < to 5 Kg, precision +/- 10g - +/- 0,5% |
Design of the dosing unit* | Screw, bi-screw, vibrating, tape |
*The design of the doser is defined according to the type of powder dosed.
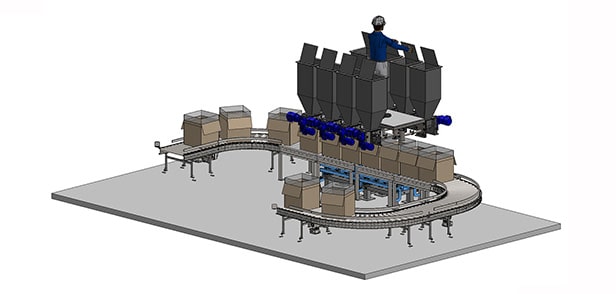
DosingMatic® - Hopper
DosingMatic® Hopper 4 | DosingMatic® Hopper 8 | DosingMatic® Hopper12 | DosingMatic® Hopper16 | DosingMatic® Hopper 20 | |
---|---|---|---|---|---|
Dosing system | 4 | 8 | 12 | 16 | 20 |
Weighing balance | 2 | 4 | 6 | 8 | 10 |
Time per batch | 60 s | 80 s | 100 s | 120 s | 140 s |
Time per cycle | 30 s | 30 s | 30 s | 30 s | 30 s |
Power Kw | 9 | 15 | 21 | 27 | 33 |
What actions for the weighing operator?
The weighing operator only fills the buffer cells of the dosing units. By scanning the material to be introduced, the automaton informs it of the cell to be loaded. Level sensors built into the buffer hoppers of the dosers inform you of the need for recharging. For customers who want large storage capacity, automatic restocking is possible by pneumatic transfer directly from silos or bulk bags.

Dosing technology:
The built-in dosers on this ingredient preparation unit are Precision Archimedes feeding screws. An agitator provides the proper flow of powders and feeding of the screws for uninterrupted dosing. When products have high granulometry or fragility, screws are replaced by vibrating feeders. Vibratory feeders are particularly suitable for the preparation of bulk products such as chocolate chips, flakes, micro-tablets, pellets, bark, etc.
How is the weighing done?
The integrated mobile hopper of the preparation unit translates on the motorized rail. This hopper incorporates load sensors to control the weights. The positioning control of the hopper allows the start of the selected doser. All weighings are stored in the pilot computer for total traceability of the recipe.
Recovery of pre-weights:
At the end of the cycle, the mobile weighing hopper is emptied into the transfer line, which is the charge for the continuous manufacturing process.
Palamatic's DosingMatic® Hopper solution is also compatible for the use of buckets or bags. In these instances, the mobile hopper and its rail are replaced by a conveyor belt and buckets.
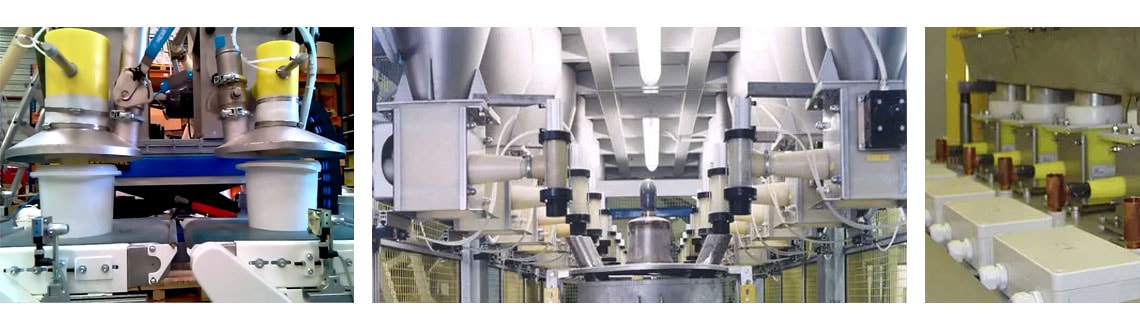
Applications standards :
The DosingMatic® Hopper dosing preparation unit is mainly located in the agri-food industry and more specifically in industrial bakeries for the feeding of kneaders, the manufacture of spice mixtures, the preparation of prepared dishes or in the field of rubber and compounding.
The precise dosing of small components via the DosingMatic® Hopper solution allows you to accurately and reliably automate the preparation of all your pre-mixes. The different versions of implementation, linear and carousel with automatic reloads, can meet all your manufacturing constraints.
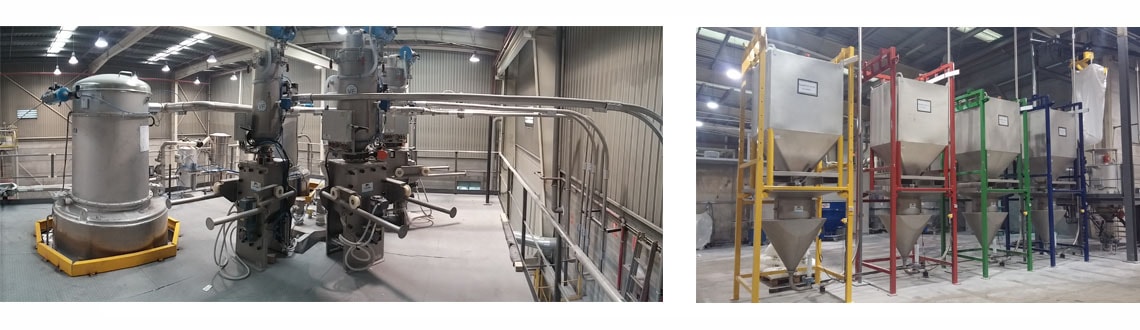
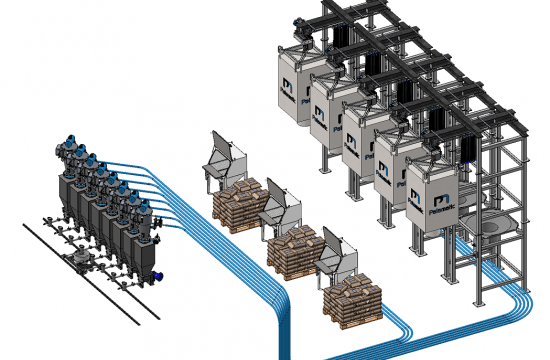
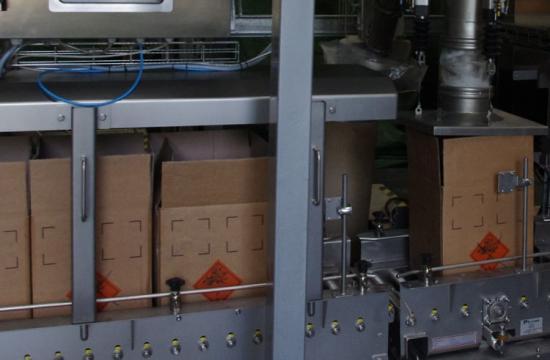
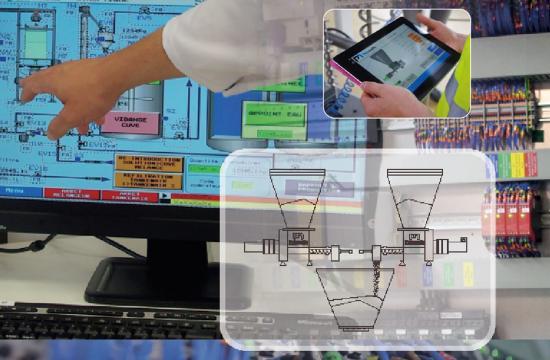
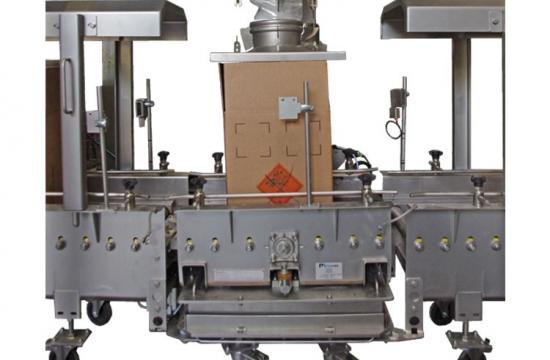
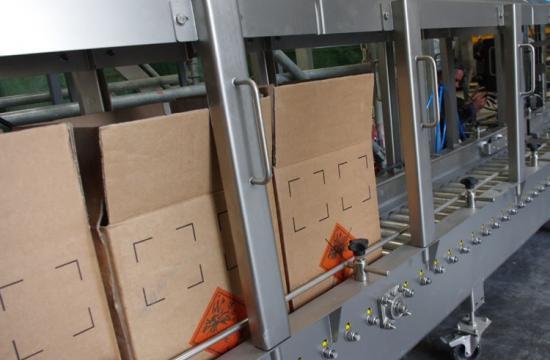
Discover the installations of our customers using the semi-automatic ingredient dosing line DosingMatic®.
All the equipment integrated in the semi-automatic ingredient dosing process line are available below.