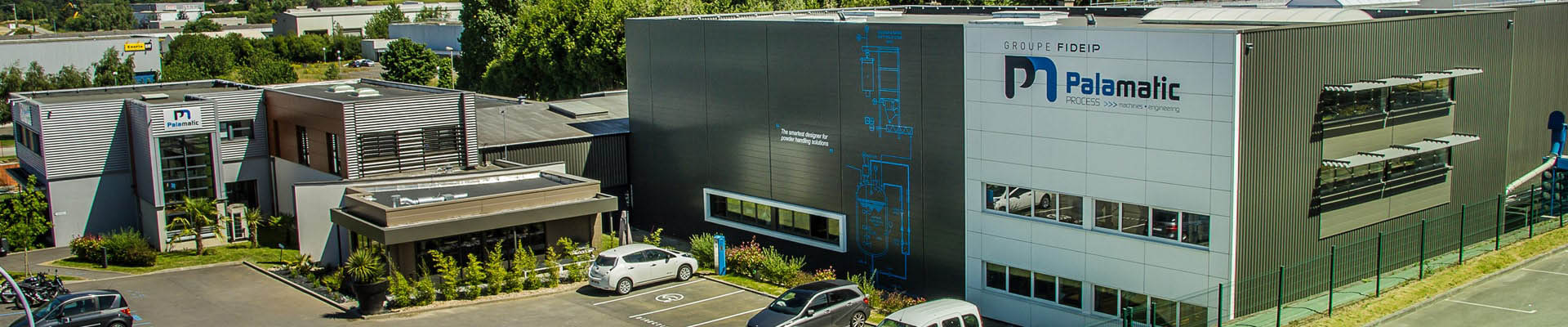
Case studies - Minerals and building
Our knowledge of the cement and quarry sector ensures you a quality service and a technical solution adapted to your project.
For your cement plants, quarries, industrial plasters, glass factories, minerals and metals, we have the solution for your bulk materials handling line or industrial powder handling line.
Case studies with our customers
Decompacting cement big bags
Cement and plastering Minerals and building
Unloading big bags of carbonaceous rock
Quarry Minerals and building
Automatic filling of spodumene big bags
Quarry Minerals and building
Semi-automatic big bag unloading
Cement and plastering Minerals and building
Semi-automated big bag filling for the construction materials industry
Minerals and building
Automated Big Bag Unloading and Conveying
Cement and plastering Minerals and building
Double deconditioning station and pneumatic dense phase cement transfer
Cement and plastering Minerals and building
Discharging station for bulk bags of ferric sulphates
Quarry Minerals and building
Process for the manufacture of plasterboard
Cement and plastering Minerals and building
Discharge and dosing for mixer feeding
Quarry Minerals and building
Big bag filling station with suspended weighing
Quarry Minerals and building
Big bag filling station Flowmatic 07
Cement and plastering Minerals and building
FlowMatic® 03 big bag filling line with barite
Quarry Minerals and building
Discharge of big bags of plaster for re-packaging into containers
Cement and plastering Minerals and building
Automatic opening and emptying of bags of plaster, cement and starch
Cement and plastering Minerals and building
Discharge of big bags of cement for truck loading
Cement and plastering Minerals and building
Big bag filling of white minerals, talc and carbonates under a silo
Quarry Minerals and building
Aggregate conveying and storage line
Quarry Minerals and building
Palamatic Process has proven expertise in the treatment, extraction, crushing, grinding, dosing, homogenization or conveying of bulk materials, such as quicklime, silica, alumina and iron oxides. Also, the use of admixtures in the manufacture of concrete makes it possible to attribute certain properties to it, particularly for high-performance concretes (technological innovation). The experience of Palamatic Process engineers and the powerful software packages used make it possible to design and implement these specific production processes. Palamatic Process offers a complete service from the definition of the requirement to the commissioning.
The process steps, for example for the manufacture of cement:
- Raw material extraction
- Grinding and storage of raw materials
- Baking of raw materials
- Storage, crushing and screening
- Packaging and conveying line
The pneumatic conveying of cement with specific equipment allows you to obtain a long service life of the installations by minimizing maintenance as much as possible.