Pneumatic vacuum conveyor: an effective solution for safe transfer without contamination
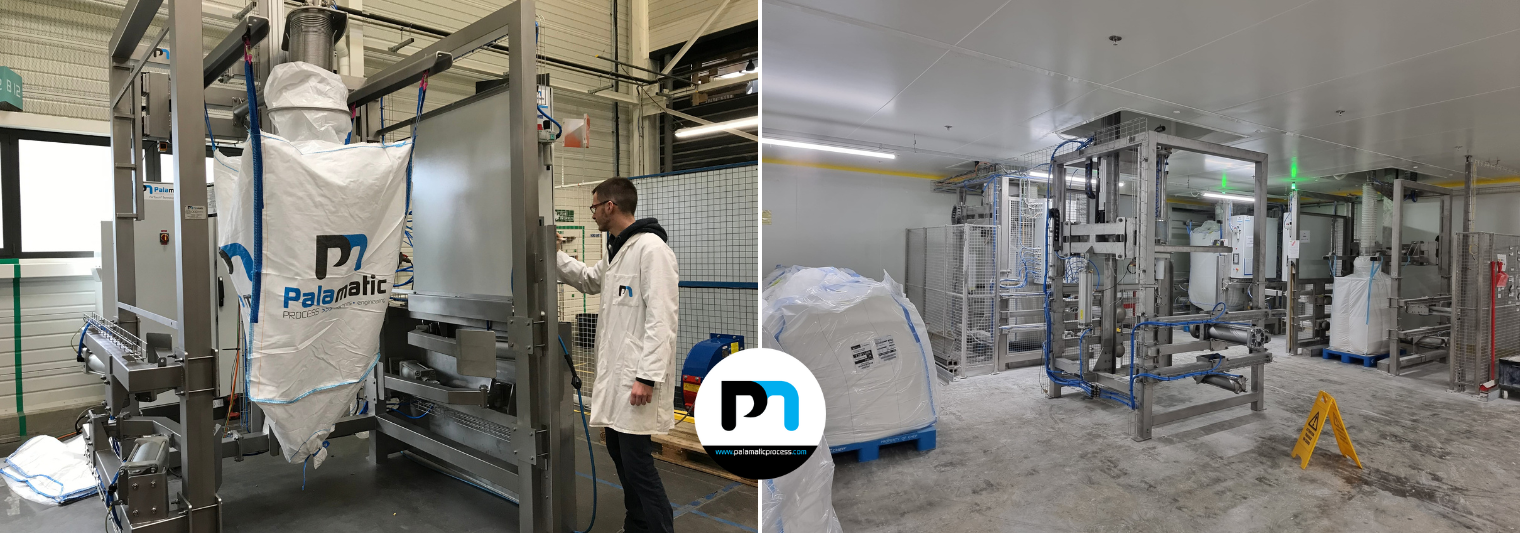
Powder transportation represents a key challenge for industries in various sectors, particularly the food, chemical and pharmaceutical industries. Companies are looking for conveyor solutions with optimised systems that guarantee operator safety, preservation of the products handled and optimal integration into their production chain.
Pneumatic conveying meets these requirements by ensuring the smooth and controlled movement of materials, without the risk of contamination or product loss. Thanks to efficient suction technology, this system reduces dust emissions, limits equipment wear and improves productivity.
To find out more about how it works, you can watch this explanatory video:
1. What is a pneumatic vacuum conveyor?
This system uses a vacuum pump to move materials through hermetically sealed pipes. Unlike mechanical conveyors, it has no moving parts in contact with the product, which limits wear and facilitates cleaning.
The main components:
- Vacuum pump: generates a vacuum to suck up the product.
- Airtight piping: ensures smooth and safe transfer.
- Integrated filter: retains fine particles and reduces air pollution.
- Receiving hopper: collects the transferred product before it is redistributed.
Thanks to these elements, the pneumatic conveyor with suction guarantees efficient handling without contamination of the powders.
2. A pneumatic conveyor with suction for more efficient transfer
Opting for a pneumatic conveyor by suction significantly improves productivity while reducing dust emissions. Thanks to its hermetic system and automated operation, it ensures the safe, fast and contamination-free transfer of powders.
2.1 Reduction of dust emissions by up to 50%
Limiting the dispersion of particles is a major issue for safety and hygiene in industrial environments. Thanks to its hermetic system and efficient filtration, the pneumatic conveyor with vacuum significantly reduces dust emissions, ensuring a cleaner working environment that complies with health standards.
- Hermetic system: limits the dispersion of particles and improves the cleanliness of the working environment.
- Complies with ATEX standards: compatible with environments sensitive to dust explosions.
- Integrated filtration: captures fine particles for healthier air and better operator protection.
2.2 Productivity gain of up to 30%
Smooth, uninterrupted conveying optimises production rates. This system guarantees controlled material transfer, reduces downtime due to blockages and limits maintenance, thus improving the overall productivity of industrial lines.
- Continuous, controlled transfer: eliminates interruptions due to blockages and optimises material flow.
- Reduced maintenance: no moving mechanical parts, reducing wear and tear and service interruptions.
- Energy optimisation: compressed air and energy consumption adjusted for more efficient operation.
2.3 A flexible and scalable solution
Each industrial process has specific requirements in terms of material transfer. The pneumatic conveyor adapts to a wide variety of products and integrates easily into existing installations, offering a modular and scalable solution to meet constantly evolving production needs.
- Suitable for a wide range of products: fine powders, granules, fragile or abrasive materials.
- Easy integration into existing production lines: no major modifications required.
- Modular and scalable system: configurable according to the specific needs of each industrial process.
- This equipment is thus an efficient alternative to mechanical conveyor systems, guaranteeing a cleaner, faster and safer transfer of raw materials.
3. The applications of the pneumatic vacuum conveyor
A pneumatic vacuum conveyor is an essential asset for industries handling powders. Its hermetic system guarantees safe transport, without loss of material and in compliance with hygiene and safety standards. It is particularly suitable for environments where cleanliness and process efficiency are priorities.
3.1 Food industry: hygienic and contamination-free conveying
- Transport without alteration of raw materials such as flour, sugar, cocoa, starch and spices.
- Prevention of cross-contamination thanks to an airtight system limiting exposure to external agents.
- Compliance with health standards for optimal food safety.
3.2 Pharmaceutical industry: controlled transfer of sensitive substances
- Safe handling of active ingredients and excipients, avoiding any accidental dispersion.
- Reduction of contamination risks with hermetic conveying and possible cleaning in place (CIP).
- Adapted to the requirements of clean rooms, guaranteeing strict compliance with good manufacturing practices.
3.3 Chemical industry: a robust system for demanding products
- Safe transfer of pigments, additives, polymers and metal powders.
- Adapted to abrasive and hygroscopic materials, reducing the risk of clogging and product build-up.
- Compatible with ATEX environments, guaranteeing the safe transportation of flammable or explosive substances.
Thanks to its versatility, this equipment is an essential solution for industries requiring the precise, clean and safe transportation of powders.
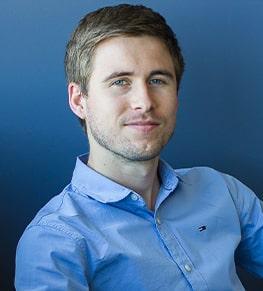
Do you have a project?
I am available to advise you and support you in your study.
Guillaume, expert in powder containment.
Q&A: All you need to know about the pneumatic vacuum conveyor
How does a pneumatic vacuum conveyor work?
This equipment uses a vacuum pump to create a vacuum in a closed pipe circuit. This difference in pressure allows powders to be sucked from a feed point (silo, hopper, big bag, etc.) to a discharge point (feeder, mixer, bagging machine, etc.).
The product is conveyed in a controlled manner, without loss or dispersion, guaranteeing a safe, clean and efficient transfer. This type of conveying is ideal for sensitive products requiring gentle handling, such as food, pharmaceutical or chemical powders.
What are the advantages of a pneumatic conveyor compared to a mechanical conveyor?
The pneumatic conveyor has several key advantages over mechanical systems such as belt or screw conveyors:
- Reduction of dust emissions by up to 50% thanks to a hermetically sealed closed circuit.
- Reduced maintenance requirements: no moving parts in contact with the product, limiting wear and breakdowns.
- Optimal hygiene: no product retention, possibility of adding a Cleaning in Place (CIP) system.
- Adaptability to various environments: compatible with ATEX zones, clean rooms and sectors with high sanitary requirements.
- Smooth and continuous transfer avoiding the frequent build-ups and blockages with mechanical conveyors.
What types of products can be transported with this system?
A pneumatic vacuum conveyor is designed for a wide variety of bulk products:
- Agri-food products: flour, sugar, starch, cocoa, spices, protein powder, etc.
- Pharmaceutical substances: active pharmaceutical ingredients (APIs), medicinal powders, etc.
- Chemicals and plastics: pigments, additives, resins, polymers, metallic powders, etc.
It is suitable for fragile products, abrasive materials and hygroscopic substances sensitive to humidity.
How can compliance with health and ATEX standards be ensured?
Depending on the industrial sector and regulatory requirements, the pneumatic conveyor can be designed with specific materials and options:
- Polished surfaces and absence of retention zones to facilitate stripping.
- High-performance filtration to capture fine particles and guarantee healthy air.
- ATEX versions for explosive environments (transport of combustible powders).
Options such as Cleaning in Place (CIP) make it possible to maintain impeccable hygiene between each production batch.
How can it be maintained to guarantee its longevity?
The maintenance of a conveyor belt is very minimal compared to a mechanical conveyor belt. However, to ensure optimal performance and extend its lifespan, it is advisable to:
- Regularly check the filters and clean or replace them as recommended.
- Check the ducts and hoppers to prevent the accumulation of residue.
- Inspect the valves and flaps to ensure they are properly sealed.
- Implement a cleaning-in-place (CIP) system to remove powder deposits between each cycle.
Regular preventive maintenance reduces the risk of clogging and ensures smooth operation over the long term.
Conclusion
Need an efficient and secure transportation solution? Contact our experts for a personalized study and find out how to optimize your industrial process today!