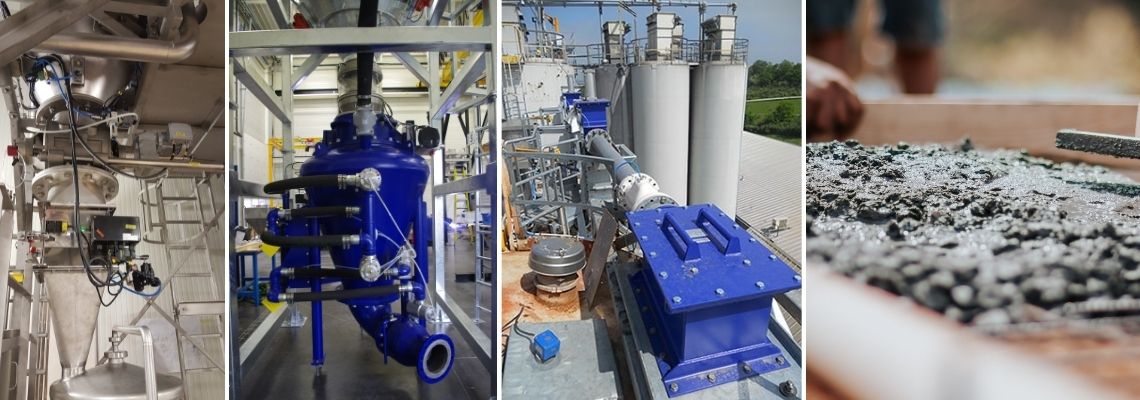
When dealing with the building materials industry, a manufacturer needs to consider all potential powders that will potentially be processed. Some mineral powders have no issues with abrasiveness while others will cause faster wear and tear on your bulk material handling equipment. Powders such as Portland cement and fly ash are abrasive and wear down process and conveying components quickly. That is why certain factors must be taken into consideration when dealing with moving parts or components that will experience friction during the production process.
1. Unloading bulk bags and sacks in an automatic and confined way
These powders tend to be delivered in either 1 ton big bags or small 50 kg paper bags. When meeting the requirements of clients who wish to automate their process and increase production capacity, an equipment supplier needs to look at how a plant can quickly open and dump sacks of powder, while also withstanding the abrasiveness of the material.
Palamatic Process offers automated bag splitting solutions, one of which is our Rotaslit® - High speed bag opening system. This automated bag dump station consists of several mechanisms to help open up bags of powder varying in size and nature. The bag is fed into the cutting machine via a motorized incline belt conveyor. Once inside the cutting chamber, circular high-speed steel blades mounted on a transmission that gives them a peripheral speed of about 60 km/h, cut the bags open. The speed of the blades helps limit emission of flakes or pieces of the bags. The cutting chamber is directly integrated into the discharge drum which rotates and flips the bag over 5 to 6 revolutions, which aids in the full discharge of the powder inside the bag. The powder then falls directly into the discharge hopper, which is clamped or bolted to the downstream process, such as a rotary valve feeding into a pneumatic conveying system.
The empty bags are then augured into a sack compactor for containment and easy disposal. To keep the work station and area clear of dust and debris, a dust filter unit can be integrated directly into the automated bag splitter.
2. Increasing the gauge or thickness of the process line material contact surfaces
Furthermore, pneumatic conveying lines can also experience significant wear and tear when dealing with powders such as dry cement and fly ash. In dilute phase pressure conveying, powder particulates are transferred along a pipe network using high velocity speeds but low pressure. As particles come into contact with pipe walls, especially at pipe bends, the wall of the pipes will wear down over time. When dealing with abrasive materials, the high velocity contact with the pipe walls and bends will quickly erode and leaks will eventually occur.
One solution to this dilemma is to increase the thickness of the pipe wall diameter. In this specific example, schedule 40 piping is utilized which is a much thicker pipe wall then standard schedule 10. For the bends of the piping network, they are reinforced with ceramic material which offer an excellent resistance to abrasives. However, due to the thicker pipe walls, the open area of the pipe section is reduced and equipment suppliers will have to consider increasing the diameter size to maintain rate as well as pressure within the powder conveying line.
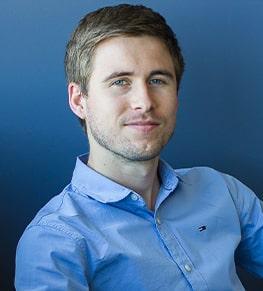
Do you handle abrasive products?
I am available to discuss your project.
Guillaume, powder expert
3. Controlling the speed at which particles move through the system
Another type of conveying system that is excellent with handling abrasive materials is dense phase conveying. Dense phase differs from the previously mentioned dilute phase by using low velocity and high pressure to slug feed the material along the conveying line. In essence, dense phase slowly and gently “drags” the material along the pipe network. By slowing down the particles inside the pipe, there is less wear on the pipe walls.
Palamatic Process has developed transfer equipment dedicated to abrasive materials such as:
- The MultiAshFlow® pneumatic conveyor is suitable for a wide variety of ashes. It ensures dust-free operations and can withstand high temperatures.
- The SAS dense phase pneumatic transfer system, specially designed for highly abrasive products. The equipment ensures slow and gentle transport of the pellets. The Inflatek® inflatable seat valve is usually integrated into the process because it offers long life and high reliability.
- The Cementveyor® pneumatic conveyor transports cement and other construction products with great versatility.
4. Using abrasion resistant coatings
When dosing and discharging into pressure conveying equipment, one must also consider the wear and tear that the rotary airlock valve will experience. Rotary valves can indeed experience a lot of wear and tear in a normal production process. The operating principle of this bulk material equipment is a rotating mechanism with several lobes (or pockets) contained within a housing. As the rotor spins, the pockets fill with the powder on the inlet side and discharge into the conveying line. Because the pressure can never directly escape into the process above, the airlock effectively seals and doses between the upstream and downstream processes. Since the rotary valve is constantly managing the powder to be conveyed, the rotor, seals and housing unit will wear down faster, especially in applications dealing with abrasive materials. Different coatings can be utilized to help prevent the internal components from wearing down to fast. For example, a chromium coating can be applied to all internal components, giving the powder valve increased durability and wear resistance.
Other areas of consideration for potential wear and tear are any parts that are constantly coming into contact with the bulk materials. These include diverter valves, butterfly valves, speed boxes, powder mills, powder mixers, etc. All can be treated with different wear coatings and special alloys to increase their durability. These potential treatments include Hardox, carbide charging, ceramics, Teflon, etc.
In summary, the key elements to handling abrasive powders is:
1. Controlling the speed of moving parts of the equipment (cutting saws)
2. Using abrasion resistant coatings (hardox, chromium, Teflon, etc.)
3. Increasing the gauge or thickness of the process line material contact surfaces (i.e., conveying lines)
4. Controlling the speed at which particles move through the system