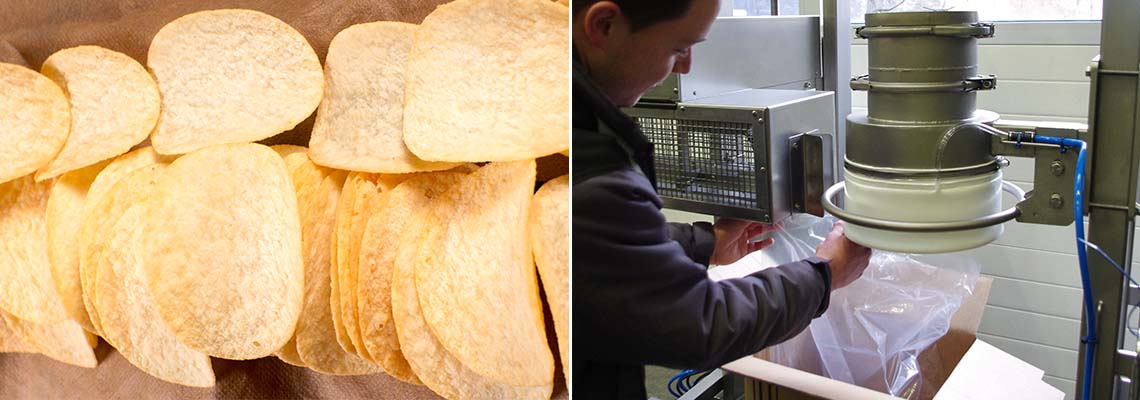
There are different technical solutions for the transport and packaging of fragile products. Some are intended for food products, and others for non-food related items. For this purpose of this article, we will explore how best to package food and snack products.
In order choose the best bagging machine for the type of products being handled as well as the type of industrial process, it is important to consider the characteristics of the product to be packaged. Other important factors include the packaging rate, desired fill capacity and the type of packaging that the product requires. Regarding the type of packaging, we must also take into account the dimensions of the sachet or bag, which depend on the volume of the product to be packaged.
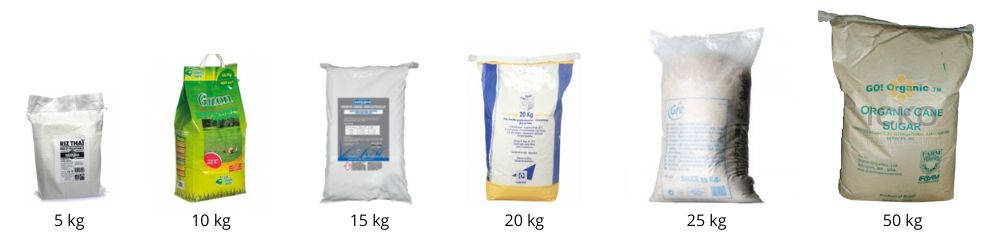
Finally, it is necessary to determine the type of sealing method, i.e., whether the bagging process requires sealing on one, two, three or four sides, depending on the initial shape of the packaging.
Some bag filling systems can also integrate the labeling of bags or pouches, whether by inkjet, thermal transfer or laser printing.
Here are some examples of fragile foods be packaged in bags or sachets at the end of the production line: coffee beans, potato chips, dried pasta, flake products, puffed snacks, biscuits, legumes, confectionery, dried fruits, seeds, spices, tea leaves, pet food, extruded products, etc.
1. Packaging in the food industry
The food industry is probably the most demanding in terms of quality and precision of packaging machines. Parts in contact with food are usually made of stainless steel. In addition to the aesthetic aspect of the sack, it is also important that the quantity is as accurate as possible in order to avoid waste and ensure compliance with the packaged weight.
Food packaging contributes to the protection of the product during transport as well as compliance with hygienic requirements. The different types of food packaging provide a barrier that inhibits or eliminates the risk of exposure to elements, such as: dust, light or humidity, in order to maintain the integrity of the packaged product.
2. What are the feed equipment solutions for the filling machines?
The filling machine can be fed using different types of dosing equipment:
Pendulum Tilting Bucket Elevator
Allows delicate handling of fragile products.
The pendulum bucket elevator is particularly suitable for the delicate and hygienic mechanical transfer of bulk food products. The use of both the corrosion-resistant, lubricant-free food grade rubber chain and easy-to-clean pendulum buckets, meets the stringent requirements of food manufacturers. The absence of lubricants considerably reduces the risk of contamination of the conveyed materials.
This elevator is specially designed for the vertical feeding of granulated products as well as chips, croutons, almonds, rice, and all types of fragile products.
The choice of tilting bucket elevator technology is simple: this mechanical conveyor solution ensures continuous transfer at high volumetric flow rates with total respect for the products integrity (avoids product breakage). This equipment technology makes it possible to transfer very fragile products. In addition, its cleaning is quick and efficient by design, which allows easy dismantling.
The vibrating feeder
Also allows transfer and dosing of friable ingredients. Installed on load cells, the vibrating feeder is used to dose by weight loss or weight gain, depending on the chosen configuration.
Helicoidal vibrating corridor/conveyor solutions can also ensure the elevation of fragile products by vibration. This vibration technology offers many advantages.
The belt conveyor
This type of conveyor is used for transporting dust-free and fragile products, such as: chips, snacks, pellets, dried fruits, biscuits, confectionery, etc. These belt elevators are also suitable for working with sticky or frozen products, such as: frozen fruits, frozen vegetables, jellies, blanched french fries, etc. The band is made of food grade rubber and comes with a food grade certificate.
The stainless steel structure can be designed in tubular form on the field, or in open profiles to reduce retention and meet the hygiene constraints of the food industry.
The aero conveyor
The use of an air conveyor is also possible because it can gently transfer fragile, brittle products over short to medium distances. As such, it represents a simple, ergonomic and robust solution.
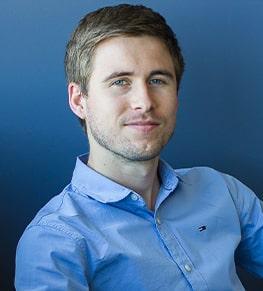
You have a handling project?
I am available to discuss the subject.
Guillaume, powder expert
3. Packaging solutions in bags
When it comes to packing different types of products in the same production batch, the multi-head weigher is the go-to solution. It is suitable for the simultaneous bagging of granular and/or fragile products while guaranteeing high dosing accuracy. Surfaces in contact with food are made in compliance with food regulations.
Some equipment can be integrated with a product stopper to prevent it from breaking.
4. Range of PalSack® bag fillers
The range is made up of 4 packaging machines available in gross or net weighing:
PalSack®01 which provides material dosing by a horizontal screw feeder.
PalSack®02 which provides material dosing by a vibrating feeder.
PalSack®03 Fast which provides high flow rates via dosing by twin-screw.
PalSack®04 ECD specially developed for hygienic applications due to the fast disassembly of its components.
The packaging machines in this range can be used to fill all types of bags ranging from 10 to 110 lbs, of various materials: burlap, paper, plastic, open mouth bag, bag with liner, single layer, double layer, microperforated, etc. The obtainable throughput rates can reach up to 100 bags / hour, in some instances.
Our PalSack® packaging machines ensure containment, precision and cleanability. They are particularly suitable for production lines processing products intended for human consumption. The integrated equipment is as follows:
• Magnetic safety grids to capture ferrous particles.
• Bag welder for total sealing.
• Densification of the product by vibrating plates.
• Shaping of the bag by push plates.
• Screw or vibrating feeder for high precision dosing with a uniform, progressive and controlled flow of your materials stored in a buffer hopper.
• Sampler to control product batches.
• Scale for commercial weighing. The tray is adjustable to adapt to different bag heights.
• Inflatable seal and pressure ring system allows the filling of any type of bag with implementation of our clamping system.
• Industrial dust removal with reclaim of fines.
By entering your email address, you agree to receive our latest articles and have read our privacy policy. You can unsubscribe at any time by contacting us at contact@palamatic.fr.