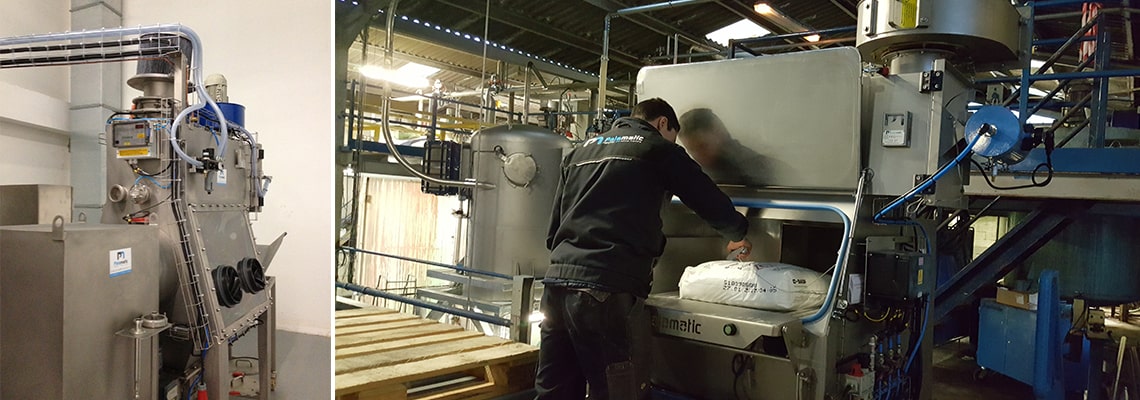
A large part of loading dry raw materials (powder and granules) in industry is still carried out manually by operators using bag dump stations.
The safety of these stations has become a major issue regarding the combustible nature of powders.
Most of the cases encountered in the industry can be summarized around 3 processes:
- Vacuum bag station equipped with a transfer system (screw, pneumatic transfer, etc.)
- Vacuum bag station equipped with a storage hopper
- Feeding of a reactor with solvent
In order to minimize the risks for the operator, both from a HAZLOC and environmental health and safety perspectives, it is important to "confine" the workstation. First, by providing a box in which the operator will open the bags, then by connecting this box to a dust removal system (flanged directly to the box or connected to an independent dust collector).
In order to best designate the station, the essential data to know in these 3 cases is the MIE (Minimum Ignition Energy) of the powders handled. In simple terms, this means knowing whether your MIE is less than or greater than 10 mJ.
1. Bag discharge station equipped with a transfer system
In this case, the transfer system installed at the exit of the bag unloader indicates that the product will be conveyed as the operator unloads the bags. In this instance, there is no need for powder storage.
From a HAZLOC point of view, the inner area of the bag unloader and the transfer system will be classified as Class 2. The outside area is generally classified as Classification 2 / Division 2 within a 1m sphere around the opening of the station.
The precautions to be taken from a HAZLOC perspective vary according to the MIE of the powder.
Case 1 - MIE > 10 mJ
- Installation of a dust collector with an antistatic filter. It can be flanged directly to the vacuum bag or remote (independent dust collector).
- No cutting tools that can create a spark.
- All electrical equipment complies with the HAZLOC zoning.
- Earthing of all equipment.
- All conductive elastomers.
Case 2 - MIE < 10 mJ
- Connection of the vacuum bags to an independent dust collector equipped with an explosion vent.
- Flame arrestor on the dust collector pipework.
- No cutting tools that can create a spark.
- All electrical equipment complies with the HAZLOC zoning.
- All equipment grounded.
- All conductive elastomers.
In this case of scenario 2, you have no choice: it is imperative to provide an independent dust collector (with explosion vent and non-return valve). Indeed, the passage of air over filters (even antistatic ones) during the suction of fines can create sufficient energy to allow the explosion to occur. A vacuum bag with an integrated dust collector cannot be equipped with the safety elements to deal with a possible explosion.
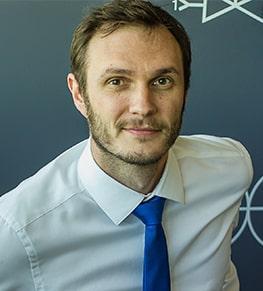
Do you need personal advice for your project?
I am available to discuss this in person.
Jean-Luc, powder expert
2. Unloading station for bags equipped with a storage hopper
In this configuration, the operator is unloading bags of powder into the buffer hopper located under the bag box. The objective is to store a sufficient quantity of powder to feed the process.
Regarding HAZLOC standards, the inner area of the bag unloader and its hopper will be classified as Division 1 (constant risk of explosion). The outside area is generally classified as Division 2, within a 1 m sphere around the opening of the station.
Case 1 - MIE > 10 mJ
- Installation of a dust collector with an antistatic filter. It can be flanged directly onto the vacuum bag or offset (independent dust collector).
- No cutting tools that can create a spark.
- All electrical equipment complies with HAZLOC zoning.
- Earthing of all equipment.
- All conductive elastomers.
Case 2 - MIE < 10 mJ
- Connection of the vacuum bags to an independent dust collector equipped with an explosion vent.
- Flame arrestor on the dust collector pipework.
- No cutting tools that can create a spark.
- All electrical equipment complies with HAZLOC zoning.
- All equipment grounded.
- All conductive elastomers.
In this second case, you have no choice: it is imperative to provide an independent dust collector (with explosion vent and non-return valve). Indeed, the passage of air over filters (even antistatic ones) during the suction of fines can create sufficient energy to allow an explosion. A vacuum bag with an integrated dust collector cannot be equipped with the safety elements to deal with a possible explosion.
3. Feeding raw materials to a reactor
Here, the operator feeds bags of powder directly into a chemical reactor via a manhole. The reactor is usually loaded with solvent. This is the worst case.
From a HAZLOC point of view, the inner area of the bag dump will be classified as Class 1 / Division 1 (constant risk of explosion). The outside part is, in general, classified in decreasing zones 1 and 2, on spheres of 1 m around the opening of the station.
Given the constant presence of solvent at the station:
Case 1 – MIE > 10 mJ
- Connection of the vacuum bag to an independent dust collector equipped with an explosion vent.
- Flame arrestor on the dust collector pipework.
- No cutting tools that can create a spark.
- All electrical equipment complies with the HAZLOC zoning.
- All equipment grounded.
- All conductive elastomers.
Case 2 – MIE < 10 mJ
The management of explosion risks for powders with an MIE < 10 mJ requires the implementation of an automatic loading system, without the action of an operator.
In fact, eagle discharges* (2 mJ) represent the main risk, as they cannot be controlled with a conventional emptying station. As the presence of solvent is constant, the risk of an explosion remains maximum.
The loading of powders must be carried out by means of equipment that allows the powder to be inerted with nitrogen before being introduced. Vacuum pneumatic transfer solutions have been developed by PALAMATIC for HaZLOC reactor loading.
*Discharges created by the simple sliding of the powder on a metallic surface such as stainless steel.