Bag emptying, pneumatic transfer and containment: a secure ATEX solution for military powders
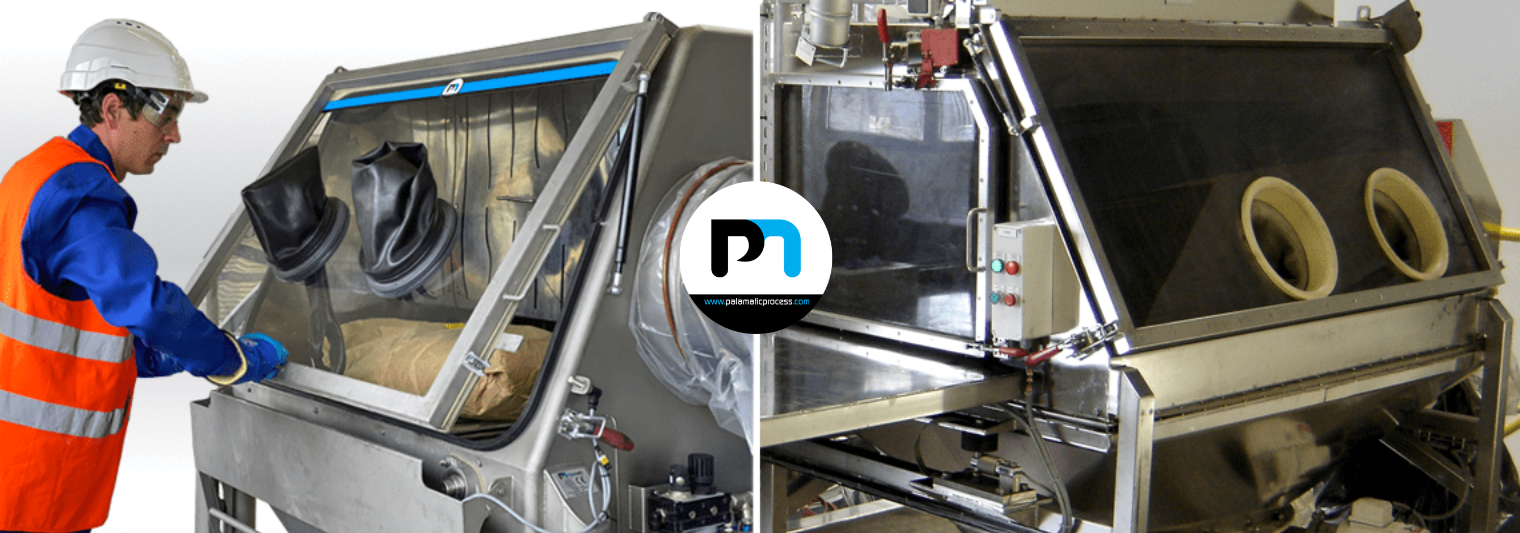
- 1. Comprendre les exigences ATEX pour les poudres militaires
- 2. La station de vidange de sacs confinée : sécurité, ergonomie et performance
- 3. Le transfert pneumatique : la technologie idéale pour les poudres explosives
- 4. Une solution industrielle complète, modulaire et certifiée ATEX
- 5. Intégration métier : applications spécifiques dans le secteur militaire
- 6. Conclusion
In the military sector, the handling of sensitive powders – whether explosive, pyrotechnic or simply reactive – imposes extreme requirements in terms of safety, containment and regulatory compliance. The slightest dispersion of dust in the ambient air can generate a risk of explosion in ATEX zones, endangering both operators and installations.
To meet these challenges, a complete industrial solution integrating an ATEX bag emptying system, secure pneumatic transfer and absolute containment is the appropriate response to the highest standards. This approach guarantees reliable and repeatable handling of military powders, while ensuring traceability, cleanliness and process continuity.
Palamatic Process designs customised lines capable of integrating each stage of the material flow – from bag reception to final bagging – in a hermetic, filtered and automated environment. This article presents the specific features of these systems, their compliance with ATEX standards and their relevance for the most sensitive defence applications.
1. Understanding ATEX requirements for military powders
1.1 Objective: to handle powders safely
In the military industry, the handling of sensitive powders – whether they are explosive, pyrotechnic or simply reactive – imposes extreme safety requirements. These substances, often used in the manufacture of ammunition and explosives or in propulsion processes, present a dual danger: explosiveness and volatility. Handling them in bulk (during unloading, transfer or dosing) exposes operators to the risk of deflagration, inhalation of toxic particles and cross-contamination.
To meet these constraints, installations must comply with the ATEX 2014/34/EU (equipment and protective systems intended for use in explosive atmospheres) directives. These regulations impose a precise classification of zones (zone 20, 21 or 22) and equipment capable of preventing sources of ignition, limiting the propagation of an explosion or containing its effects.
1.2 ATEX classification: what are the requirements for equipment?
ATEX regulations are based on a classification of zones according to the likelihood of an explosive atmosphere:
- Zone 20: permanent presence of explosive dust in suspension (inside a tank, filter or transfer equipment).
- Zone 21: frequent, but not permanent, presence during regular operations.
- Zone 22: occasional presence (breakdowns, accidental leaks).
Each zone imposes specific requirements in terms of materials, motors, sensors, emergency stop systems, and especially containment and filtration methods. A simple leak or a source of static electricity can be enough to trigger an explosion. This is why all components – from the bag emptying station to the pneumatic transfer system – must be rigorously selected, ATEX certified and installed in accordance with the standard.
1.3 What are the specific risks associated with pyrotechnic powders?
The powders used in military applications (nitrates, perchlorates, black powders, oxidisers, primers, etc.) have highly unstable physicochemical properties. They can:
- Spontaneously ignite under the effect of simple friction or static electricity.
- Form highly explosive clouds of dust suspended in the air.
- Chemically degrade on contact with moisture or ambient air, releasing toxic gases.
The simple spillage of a bag can be enough to create a dangerous zone if it is not properly contained. Hence the absolute necessity of an integrated system of containment, filtration, and grounding to evacuate electrostatic charges.
FAQ: What are the risks associated with handling powders in an ATEX environment?
The main risks are:
- Explosion due to a concentration of flammable dust in the air,
- Ignition by a spark (electrostatic, mechanical or thermal),
- Contamination of operators by inhalation of toxic particles.
In an ATEX environment, these risks are multiplied by the constraints of the process (unpacking, transfer, dosing), requiring a rigorous design of the equipment to guarantee the safety of people and installations.
2. The confined bag emptying station: safety, ergonomics and performance
2.1 Objective: to ensure unloading without dispersing dust
In the military sector, the manual unpacking of sensitive powders is a critical phase of the process. Simply opening a bag of pyrotechnic powder can release fine particles that are dangerous to both operators and the working environment. There is a real risk of explosive dust clouds forming, especially when emptying multi-layer paper bags or bags containing hygroscopic materials.
The objective is therefore clear: open, empty and dispose of the bags without ever exposing the product to the ambient air, while ensuring a healthy and safe working environment that complies with the ATEX directive.
2.2 How a Sacktip® SE station works in an ATEX environment
The Palamatic Process Sacktip® SE station is specially designed to meet the strictest safety standards, particularly for explosive or reactive powders. Its principle is based on a confined and sealed enclosure equipped with a glove box, allowing the operator to handle the bag without ever coming into contact with the powder.
Here are the key stages of operation:
- Lateral introduction of the bag through a secure, watertight hatch.
- Opening of the bag under containment, with the bag held in position.
- Controlled emptying into a hopper connected to a transfer or dosing system.
- Automatic evacuation of the empty bag to a compactor or collector, without manual removal.
- Continuous dust removal, integrated into the cabin, with H13 or H14 rated filter cartridges.
The structure can be made entirely of 304L or 316L stainless steel, with mirror-polished interior finishes to guarantee hygiene and the flow of the product without retention. All critical components (fans, sensors, motors) are ATEX zone 20/21 certified depending on the location.
2.3 Containment options: glove box, H14 filter, integrated dust extraction
Each oil change station can be customised according to the level of containment required:
- Single or double glove box for contactless operator intervention.
- H14 absolute filtration with automatic cleaning, for capturing fine dust.
- Dust extraction ring, ensuring continuous extraction of fine particles during emptying.
- Connection of bags with inner liner, reinforced seal and hermetic weld.
- Contactless foot pedal to activate the emptying cycle without risk.
Palamatic also offers the option of integrating a bag compactor into the containment chamber, avoiding the need to handle contaminated empty bags outside the cabin.
FAQ: What is a bag emptying system in an ATEX zone?
A system for emptying bags in an ATEX zone is a piece of equipment designed to enable the safe opening and unloading of bags containing potentially explosive powders. It is contained, watertight, equipped with explosion-proof filters and designed to avoid any source of ignition (static electricity, mechanical heating, sparks). It protects operators and the working environment and prevents the risk of explosion linked to airborne dust.
3. Pneumatic transfer: the ideal technology for explosive powders
3.1 Objective: to transport the powder without breaking containment
In an ATEX installation intended for military powders, the transfer of product between two pieces of equipment (for example, from the emptying station to the dosing or filling system) is a critical stage. This transfer must be carried out without loss of containment, without product accumulation, or friction likely to create a source of ignition.
Pneumatic transfer is the optimal solution for moving explosive powders, as it allows for completely hermetic conveying, without manual intervention or mechanical transport by chain or screw, which often generate too much kinetic energy or heat.
3.2 Choosing between dilute or dense transfer depending on the military powders
There are two main principles of pneumatic transfer by pressure or vacuum:
- Dilute transfer: the product is conveyed at high speed in a fast and continuous air flow. This method is effective for light powders but can generate abrasion or static electricity. It is therefore not recommended for pyrotechnic or fragile powders.
- Dense transfer: the product is pushed in bursts in a high concentration, low speed air flow. This method reduces friction, the formation of dust clouds and electrostatic risks. It is ideal for explosive, unstable or hygroscopic powders.
At Palamatic Process, dense pneumatic transfer is favoured for these sensitive applications. It is often equipped with antistatic sleeve valves, 316L stainless steel lines with internal treatment, differential pressure sensors and grounding points.
3.3 Integration of a secure transfer circuit with terminal filtration
A complete pneumatic transfer installation for military powders generally includes:
- A confined emptying station or buffer hopper,
- A pneumatic injector or ATEX rotary airlock,
- An antistatic stainless steel pipe network with long-reach elbows,
- An absolute terminal filter, often class H14, with explosion-proof cartridges,
- Pressure switches, non-return valves and secure purge systems.
The whole system is controlled by a Pal'Touch® automated controller, which manages the transfer sequences according to weight, time or pressure criteria, guaranteeing both performance and traceability.
Finally, maintenance is simplified thanks to Easyclean systems for the rapid dismantling of the transfer lines and complete cleaning between two sensitive batches.
FAQ: What is the difference between dilute and dense pneumatic transfer?
Dilute pneumatic conveying uses a fast air flow to transport low-concentration powders, ideal for less sensitive products. Conversely, dense conveying transports the product slowly, in packets, with little air and less turbulence. This method is preferred for explosive or sensitive powders, as it limits duct wear, static electricity generation and the risk of explosion.
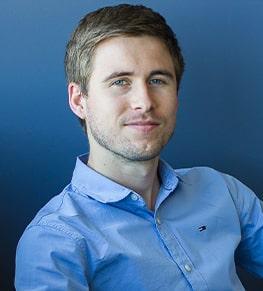
Do you have a project involving the transfer of explosive powders in an ATEX environment ?
I am available to assist you.
Guillaume, expert in explosion-proof powder transfer systems
4. A complete, modular and ATEX-certified industrial solution
4.1 Objective: to integrate all links in the process into a single secure line
Handling explosive powders in a military environment does not allow for improvisation. To guarantee the safety of operators, regulatory compliance and production performance, it is essential to integrate each phase of the process – from the receipt of bags to filling – into a unified, controlled and secure system.
An effective solution is not based solely on the addition of independent equipment, but on a complete line designed in a modular way where each module (emptying, transfer, dosing, filling, dust removal) is perfectly interconnected, adapted to the ATEX environment and designed to work in synergy.
4.2 Link between emptying, transfer and weight dosing
In a standardised Palamatic Process configuration, the equipment is linked as follows:
- Confined sack tipping (Sacktip® SE): controlled opening without dust emission.
- ATEX buffer hopper with vibrating bottom or mechanical de-wirrer, to ensure a smooth flow of sensitive powders.
- Dense pneumatic transfer system to a dosing or filling station.
- Weight dosing unit (screw or belt) for precise control of the quantity transferred.
- Secure filling (bags, drums, big bags) with management of weighing, containment and dust.
Each transition point is equipped with flexible anti-static sleeves, inflatable seals for tightness, and connected sensors for real-time monitoring of the process.
4.3 Automation, weighing, traceability: the contribution of Palamatic Process solutions
Centralised control via the Pal'Touch® interface allows intuitive management of:
- transfer parameters (time, flow rate, pressure),
- traceability of operations (unloaded weights, batch number, operator, etc.),
- safety alerts (clogging, excessive pressure, ATEX fault).
The automation can integrate:
- personalised product recipes (by powder, by process),
- management of valves and flaps,
- integration into an MES or ERP for complete synchronisation of the production chain.
The result: a faster, safer system, without the risk of human error, compliant with the quality requirements of the defence sector.
FAQ: How does an integrated dust extraction system work?
An integrated dust removal system captures the fine particles released when emptying, transferring or filling powders. It consists of filter cartridges (often H13 or H14), an automatic cleaning system (using compressed air), an ATEX fan and a collection chamber. The filtered air can be discharged or recycled, and the system is designed to operate in negative pressure to guarantee total containment of the installation.
5. Job integration: specific applications in the military sector
5.1 Objective: to respond to the constraints of pyrotechnic and sensitive powders
The handling of powders in the military domain is not limited to a question of performance or automation. It is a matter of national security, where the slightest error can have dramatic consequences. The powders handled – propellants, primers, explosive charges, reactive chemical additives – have highly unstable properties, whether in terms of their sensitivity to friction, their hygroscopicity or their toxicity.
The facilities must therefore:
- Be ATEX zone 20/21 certified throughout the chain (inside the equipment and outer casings).
- Guarantee handling without emissions in a confined environment.
- Ensure complete traceability of the batches handled.
- Offer solutions for fast and safe cleaning between two series (change of powder, change of recipe).
5.2 Use case: safe filling line for primer powder
Let's take the example of a processing line for the primer powder used in the manufacture of detonators:
- Reception of the powder in unit bags, stored in an ATEX zone with hygrometric control.
- Manual emptying confined via a Sacktip® SE station with glove box.
- Dense pneumatic transfer with grounding at each connection point.
- In-line safety screening to eliminate agglomerates.
- High-precision weight-based dosing device for controlled filling of mini-containers.
- Semi-automatic filling station with product closure and sealing.
This configuration drastically limits operator exposure, prevents product loss, secures production and meets army requirements in terms of safety, repeatability and production hygiene.
5.3 Maintenance, cleaning, ergonomics: the advantages of a customised design
Unlike standard installations, ATEX lines for military powders must integrate:
- Systems for rapid disassembly (Easyclean, clamp connections, inspection hatches),
- Remote maintenance areas, to avoid any direct intervention in hazardous areas,
- A modular structure, allowing equipment to be isolated without shutting down the entire line,
- Cleaning in place (CIP) or dry cleaning, depending on the sensitivity of the powders,
- Ergonomics designed for the operator, with access via side panels, contactless controls, intuitive screens.
The objective is not only to meet standards, but to design a safe, fluid, reproducible working environment that is adapted to the human constraints of the field.
FAQ: What industrial equipment is used for sensitive powders in the military sector?
The recommended equipment is:
- Confined emptying stations with glove box (Sacktip® SE),
- Dense pneumatic transfer systems in antistatic stainless steel,
- Screw weigh feeders with containment and traceability,
- Filling stations (bags, drums, specific containers) in ATEX environment,
- Dust filtration systems (H14 cartridges),
- Supervisory interface (Pal'Touch®) with recipes, traceability and alarm management.
All these elements must be certified for ATEX zones 20 or 21 depending on their location, and configurable to meet the specific requirements of explosive, hygroscopic or toxic powders.
6. Conclusion
In the military industry, safety is not negotiable. Handling explosive or pyrotechnic powders requires absolute rigour at every stage: from the receipt of raw materials to final packaging. A compartmentalised approach, with isolated equipment, is no longer enough. Only a global solution, designed for containment, secure transfer and ATEX compliance, can meet the real challenges in the field.
Palamatic Process designs and integrates complete customised lines, combining:
- Confined emptying stations,
- Dense pneumatic transfer,
- Weight dosing,
- Filling under controlled atmosphere,
- H14 dust extraction,
- Centralised control.
These facilities are certified, proven and already in operation in several sensitive contexts related to defence or critical powders. They guarantee operator safety, process reliability and regulatory compliance.