Optimising powder flow in hydrometallurgy: Key issues, best practices and industrial applications
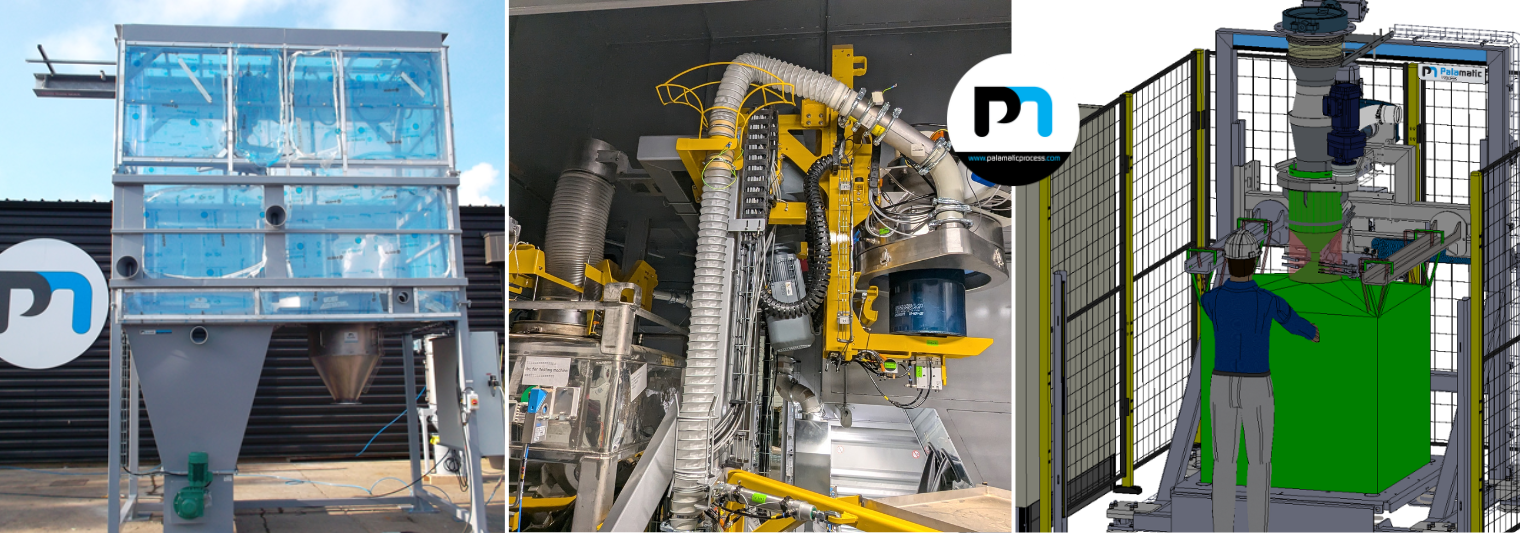
In the modern hydrometallurgical industry, mastering the flow properties of powders is a major technical and economic challenge.
Hydrometallurgical processes involve the handling of powdery materials at many stages: crushing of ores, handling of precipitates, filtration, drying and packaging of finished products.
An inadequate fluidity of the powders quickly transforms an efficient installation into an operational nightmare: blockages in the silos, formation of arches, segregation of particles and clogging of equipment.
This article offers a complete overview of the issues, methods and innovations that make it possible to sustainably improve the fluidity of powders in hydrometallurgical processes.
1. The technical and economic issues of poor powder flow
Impact on maintenance costs
The handling of powders with low fluidity leads to premature wear of transfer equipment.
Flow problems are responsible for 35 to 40% of unscheduled maintenance interventions in hydrometallurgical units.
A study conducted in 2023 on fifteen production sites showed that an improvement in the powder flow index (measured by the angle of repose) of only 5° can reduce the associated maintenance costs by 22% on average.
The components most affected are generally
- Screw conveyors and conveyors, whose lifespan can be reduced by 30 to 50%.
- Valves and flaps, which suffer accelerated abrasion
- The inner linings of silos and hoppers, damaged by excessive force
These recurring failures lead to direct expenses (replacement of parts, labour) estimated at between 2 and 4% of annual turnover depending on the size of the installations.
Associated production losses
Flow disruptions cause particularly damaging production stoppages.
A comparative analysis conducted on the Canadian hydrometallurgical sector in 2022 revealed that powder fluidity problems were responsible for:
- 7 to 12% of unplanned downtime
- 3 to 5% reduction in the overall utilisation rate of capacity
- An average loss of earnings of €850 per tonne of installed capacity per year
In leaching units where a steady supply of solid reagents is critical, flow fluctuations can reduce metal extraction yields by 3 to 8 points, directly impacting profitability.
Impact on product quality
Product quality is highly dependent on the homogeneous and controlled flow of powders.
Flow anomalies lead to:
- Phenomena of segregation: Particles of different sizes or densities tend to separate during flow, creating heterogeneity in the mixtures.
In selective precipitation processes, this segregation can lead to variations in the purity of the final product of around 0.5 to 2%.
- Dosing irregularities: Erratic flow leads to flow rate fluctuations of up to ±15% around the nominal value, compromising the stoichiometry of the reactions and affecting the overall yield.
- Changes in physical properties: Excessive mechanical stresses can alter the crystalline structure and morphology of the particles.
A study on zinc oxide powders has shown that high shear stresses can reduce the specific surface area by up to 18%, directly affecting the reactivity of the product.
The non-conformities resulting from these problems represent on average 2.8% of total production in the sector.
Risks to industrial safety
The risks associated with poor powder flow also affect safety:
The risks associated with poor flow may include:
- Risk of collapse of vaults: The formation of bridges and vaults in silos creates areas of vacuum that can suddenly collapse, generating instantaneous overloading.
- Dust emissions: Manual interventions to unblock flows cause potentially toxic dust emissions, representing a significant risk of occupational exposure.
- Mechanical overloads: The efforts made to restore flow can subject the structures to stresses exceeding their design limits.
Sector statistics indicate that 12% of serious industrial accidents in the hydrometallurgical field are linked to problems of solid matter flow.
Analysis of incidents shows that the time operators are exposed to risks associated with working with blocked powders can be reduced by 78% by preventative measures to improve the flow of materials.
2. Optimisation of particle size and morphology
Mechanism of action
The distribution of particle size and the shape of particles have a direct influence on interparticle interactions and therefore on overall fluidity.
Optimisation consists of:
- Adjusting the distribution of particle sizes to minimise interstitial spaces while limiting cohesive forces
- Favouring spherical or ellipsoidal morphologies that reduce mechanical blockages and contact surfaces
These modifications have a direct effect on the coefficient of internal friction and the angle of natural slope, which are determining factors in fluidity.
Advantages and limitations
Advantages:
- Long-term solution that does not require chemical additives
- Simultaneous improvement of compactness and fluidity
- Significant reduction in arching phenomena (up to 65% according to the cases studied)
Limitations:
- Requires precise and well-maintained grinding/sieving equipment
- May modify other physicochemical properties of the material (reactivity, solubility)
- Initial investment often substantial
Industrial example
The hydrometallurgical refinery in Kokkola (Finland) optimised the granulometry of its precipitated zinc hydroxide by adopting a two-stage pneumatic classification system.
The narrower particle size distribution (90% of particles between 45 and 75 μm) enabled an improvement in the Hausner flow index from 1.38 to 1.22.
Results obtained:
- Reduction of 82% in unblocking operations
- Increase of 7.3% in mass flow in transfer systems
- Return on investment achieved in 8.5 months of operation
- Estimated annual savings of €420,000
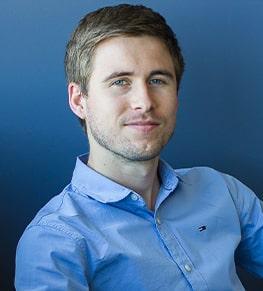
Do you have a project in mind?
I am available to advise you and assist you in your research.
Guillaume, expert in powder flow optimisation for hydrometallurgy
3. Operational solutions to improve powder flow
Addition of fluidising additives
Mechanism of action
The fluidising additives act according to three main mechanisms:
- Reduction of electrostatic forces by neutralisation of surface charges
- Reduction of Van der Waals forces by modification of surface roughness
- Creation of a boundary layer reducing direct contact between particles
The most commonly used additives in hydrometallurgy are pyrogenic silica (0.1-0.5%), metal stearates (0.2-1%) and certain organic derivatives such as polyethylene glycol (0.3-0.8%).
Advantages and limitations
Advantages:
- Rapid implementation without major modification of equipment
- Dosage adjustable according to operating conditions
- High efficiency even at low concentrations (typically <1%)
Limitations:
- Recurring costs related to additive consumption
- Risk of contamination of the final product
- Compatibility sometimes limited with subsequent stages of the process
Industrial example
In a copper oxide production unit in Chile, the incorporation of 0.3% hydrophobic fumed silica in the oxide powder after filtration resulted in
- A reduction in the dynamic angle of repose from 56° to 38°
- A 91% decrease in blockages in the bagging systems
- An improvement in dosing accuracy from ±12% to ±3%
- An additional material cost of €1.2/tonne offset by a reduction in operating costs of €3.8/tonne
The use of a bio-based additive based on modified starch (0.4%) has shown comparable efficiency with a 43% reduction in environmental impact according to the life cycle analysis.
Specific mechanical treatments
Mechanism of action
Mechanical treatments aim to disrupt the cohesive forces between particles and provide the energy needed to initiate and maintain flow.
Three main approaches are used:
- Controlled vibration: Application of optimised frequency and amplitude vibrations to temporarily fluidise the powder mass without causing compaction.
- Mechanical fluidisation: Use of agitators, mixers or rotating discs to create a controlled shear that keeps the powder in a quasi-fluid state.
- Pneumatic assistance: Injection of low-pressure air to reduce interparticle contact and facilitate flow.
Advantages and limitations
Advantages:
- Immediate effect on flow
- Adaptability to variations in material properties
- Preservation of the physicochemical characteristics of the powder
Limitations:
- Energy consumption can be significant
- Possible attrition of fragile particles
- Specific design required for each installation
Industrial example
Umicore has implemented a mechanical fluidisation system using a vibrating cone in its anode slime treatment unit in Hoboken (Belgium).
The system combines low-frequency vibration (12 Hz) with synchronised injection of pulsed air.
The results speak for themselves:
- Increase in flow rate from 760 kg/h to 1250 kg/h (+64%)
- Reduction in flow rate variability from ±18% to ±4%
- Reduction in power consumption per tonne transferred from 1.8 kWh to 1.2 kWh
- Complete elimination of manual intervention for unblocking
The investment of €175,000 was recovered in less than 14 months thanks to productivity gains and reduced maintenance costs.
Changes in environmental conditions
Mechanism of action
The flow properties of powders are strongly influenced by the ambient conditions:
- Control of relative humidity: Reducing humidity limits the formation of liquid bridges between particles, a phenomenon that is particularly problematic for hygroscopic salts.
- Temperature management: Controlled temperature increases reduce moisture adsorption and can reduce adhesion forces between particles.
- Pressure modification: In some cases, slight pressurisation or depressurisation can significantly improve flow characteristics.
Advantages and limitations
Advantages:
- Uniform improvement of flow properties
- No chemical alteration of products
- Possible synergy with other optimisation methods
Limitations:
- Energy costs associated with air conditioning
- Technical complexity of environmental control systems
- Sensitivity to seasonal variations
Industrial example
A nickel sulphate production plant in Australia has set up an integrated environmental control system for its drying and conditioning units.
The system maintains a relative humidity of less than 35% and a constant temperature of 33°C in the critical powder transfer zones.
The documented results after 12 months of operation are significant:
- Improvement of the Carr flowability index from 22 to 16
- Reduction of 68% in flow incidents
- Decrease in product loss due to handling from 2.3% to 0.8%.
- Additional energy consumption of 135 kWh/tonne offset by an increase in productivity of 11%.
4. Recent technological innovations and future prospects
Nano-structured coatings
Polymer or ceramic coatings on a nanometric scale are now applied to surfaces in contact with powders.
These treatments create optimised surface patterns (such as ‘sharkskin’) which drastically reduce the adhesion of particles.
Industrial tests show a reduction in the friction angle of 30 to 40% compared to conventional polished surfaces.
The durability of these coatings now reaches 18 to 24 months in abrasive environments.
Online characterisation systems
The rheology of powders can now be monitored continuously using non-intrusive acoustic and optical sensors.
These devices analyse in real time:
- The particle size distribution
- The interparticle cohesion
- The tendencies to agglomerate
Coupled with artificial intelligence algorithms, these systems make it possible to anticipate flow problems and automatically adjust the operating parameters before blockages occur.
Controlled electrostatic fluidisation
An innovative approach consists of applying a modulated electrostatic field that modifies the cohesive forces between particles.
Current prototypes make it possible to reduce adhesion forces by up to 60% without chemically modifying the powder.
This technology, which is still in the industrial demonstration phase, seems particularly promising for fine metal powders and semiconductor oxides.
Bio-additives from the circular economy
Recent research has identified several agricultural and forestry by-products which, after specific treatment, have excellent fluidising properties.
These bio-based additives offer a sustainable alternative to synthetic fluidity agents with a 70 to 85% reduction in environmental impact.
Modified lignin derivatives and cellulose nanofibrils show comparable performance to conventional pyrogenic silica at equivalent concentrations.
Conclusion
Conclusion
Optimising the fluidity of powders is a crucial performance lever for the hydrometallurgical industry.
For manufacturers wishing to improve their processes, we recommend:
- Characterising precisely the flow properties of powders at each critical stage of the process
- Developing an integrated strategy combining granulometric optimisation, additives and appropriate mechanical assistance
- Install monitoring systems to enable early detection of deviations and preventive action
- Train operational teams in the fundamentals of powder mechanics
- Integrate fluidity as a key parameter in the continuous improvement process
The return on investment, generally less than 18 months, combined with the improvement in working conditions and product quality, fully justifies the growing attention paid to this issue by the leaders of the hydrometallurgical sector.
📞 Do you work in the processing or recovery of hydrometallurgy ?
Contact our experts to design a customised, high-performance and secure production line together.