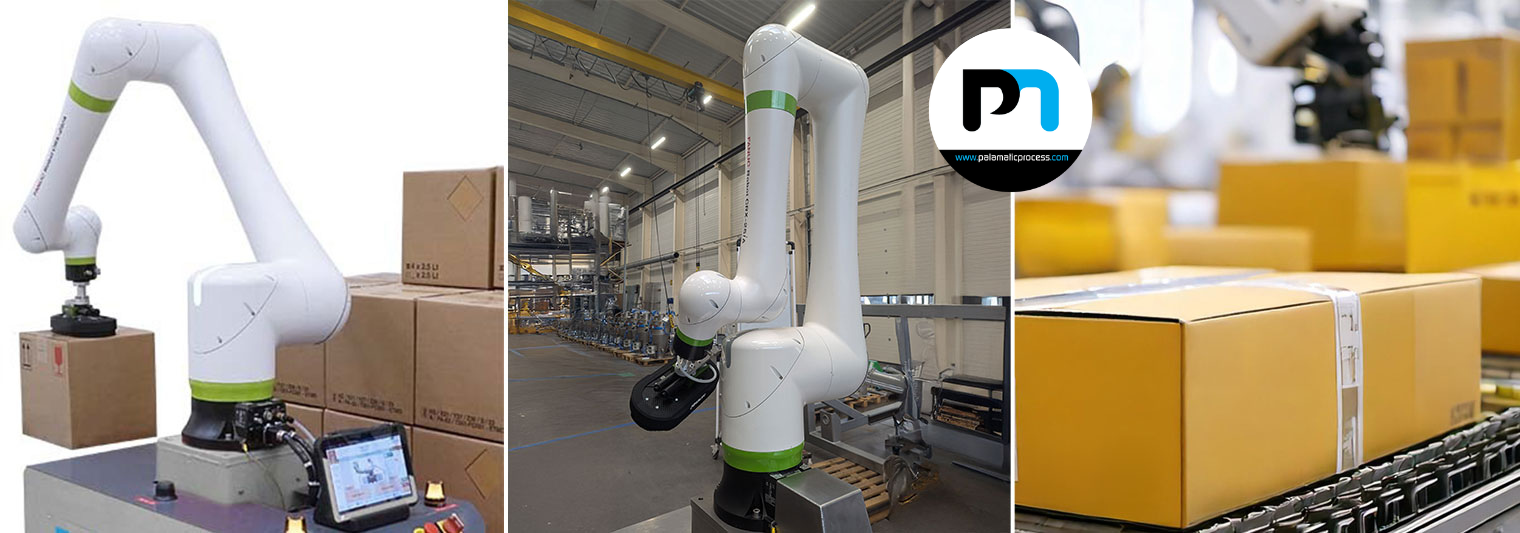
- 1. The benefits of cobots in industry
- 2. Disadvantages of cobots in industrial environments
- 3. Examples of cobot applications at Palamatic Process
- 4. Comparison: Cobots vs. conventional industrial robots
- 5. Recommendations for successful cobot adoption
- 6. Conclusion: cobots, a strategic technical solution (h2)
Today, cobots, or collaborative robots, are a tangible reality transforming our factories. But as with any great revolution, there are opportunities... and challenges.
Unlike traditional robots, they are designed to work in direct interaction with humans. However, their integration into industrial processes brings with it both advantages and technical challenges.
This article presents a detailed analysis of the advantages of cobots, as well as the constraints to be considered before their implementation.
1. The benefits of cobots in industry
Increased safety for cobots
As in the works of Asimov, cobots are designed to protect humans. Thanks to their advanced sensors, cobots detect the presence of obstacles or people nearby and adjust their movement or stop automatically to avoid accidents.
- Key technologies : Force sensors, 3D cameras, power-limiting systems.
- Concrete benefits : Reduced risk of accidents in shared environments.
The flexibility and adaptability of cobots
Cobots can be programmed for a wide range of tasks, from handling to quality control.
- Application examples :
- Palletizing finished products.
- Component assembly.
- Handling delicate materials.
- Benefit : Reduced time and costs associated with production configuration changes.
Improving productivity with cobots
By automating repetitive or tedious tasks, cobots enable operators to concentrate on higher value-added tasks. A gain in efficiency reminiscent of the technological utopia of "The Night of Days".
- Impact : Continuous production and increased efficiency.
- Example : Use of cobots for packaging, guaranteeing constant throughput.
Long-term cost reduction
Cobots require few modifications to existing infrastructures, and consume less energy than traditional robots.
- Maintenance costs : Low, thanks to standardized, robust components.
- Typical ROI : often achieved in 1 to 3 years, depending on the application.
Cobots help improve working conditions
By taking on the most physical tasks, cobots reduce musculoskeletal disorders and improve operator satisfaction.
- Example : Handling heavy loads in a warehouse.
2. Disadvantages of cobots in industrial environments
Limited load capacity
Cobots are designed for light to moderate tasks. They are not suitable for applications requiring high power, high speed or extreme precision.
- Payload : Generally between 3 and 15 kg.
- Limitation : Not suitable for heavy industry or extreme environments.
High initial cost
Although competitive with conventional industrial robots, cobots represent a significant initial investment, especially for small businesses.
- Typical cost : between €20,000 and €50,000, excluding installation.
- Challenge : Justify the investment for small runs or short cycles.
Integration complexity
Integrating cobots into existing production lines may require in-depth study and adjustment.
- Possible problems : Compatibility with existing equipment, software adjustments.
- Solution : Plan a pilot test phase before large-scale deployment.
Training needs
Even if the interfaces are intuitive, programming and managing cobots requires initial training. Like HAL 9000 in "2001: A Space Odyssey", a poorly mastered cobot can pose technical challenges.
- Time required : From a few hours to several days, depending on the complexity of the task.
- Impact : Temporary reduction in productivity during the transition phase.
Vulnerability to cyber attacks
Connected cobots can be a target for cyber attacks.
- Requirement : Implement appropriate IT security protocols.
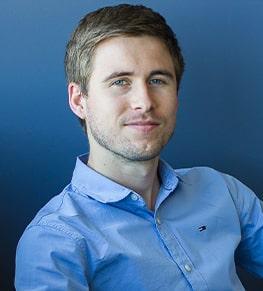
Do you have a cobot implementation project?
I'm available to advise and support you in your study.
Guillaume, cobot expert.
3. Examples of cobot applications at Palamatic Process
Bag handling
- Context : Automated bag loading and unloading.
- Solution : Use of cobots to manage various formats, adjust filling cycles and guarantee optimum throughput.
- Result :
- Reduced operator fatigue.
- Productivity increased by 20%.
Automated packaging
- Context : Packaging lines in the food industry.
- Solution : Integrated cobots for assembly, screwing and packaging.
- Result :
- Improved production rates.
- Reduced human error.
4. Comparison: Cobots vs. conventional industrial robots
Criteria | Cobots | Industrial robots |
---|---|---|
Human interaction | Direct collaboration | Areas isolated by barriers |
Payload | Up to 15 kg | Up to several tons |
Installation costs | Low (few modifications) | High (specific infrastructures) |
Maintenance | Ease of use and reduced costs | Specialized maintenance required |
Flexibility | Easy reprogramming | Limited to fixed tasks |
5. Recommendations for the successful adoption of cobots
- Assess needs : Identify repetitive, tedious or time-consuming tasks.
- Feasibility study : Analyze the compatibility of cobots with existing equipment and production flows.
- Train teams : Plan training sessions to get you up to speed quickly.
- Plan integration : carry out a pilot test before full-scale deployment.
- Maintenance : Implement a monitoring program to optimize performance.
Useful links for further information
6. Cobots, a strategic technical solution
Cobots are powerful tools for modernizing industrial processes, but their adoption must be carefully planned. A rigorous analysis of needs, capabilities and constraints helps maximize their impact while minimizing technical obstacles.