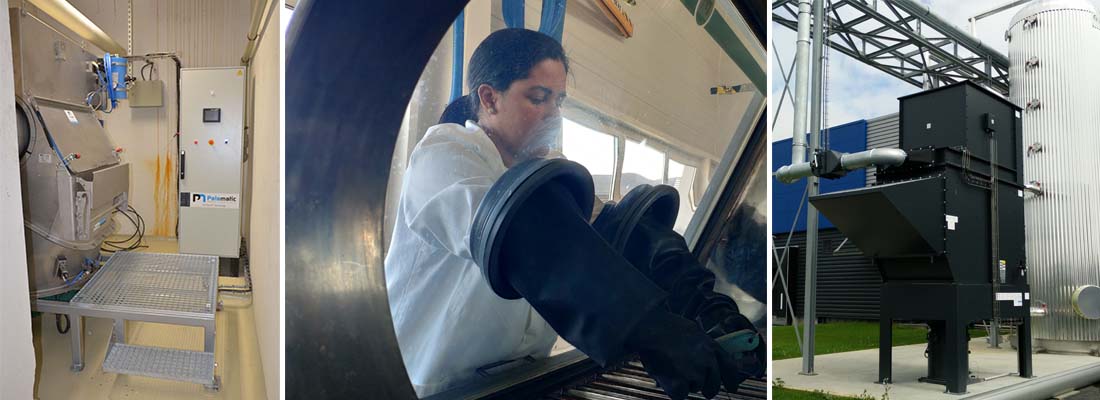
When considering health and safety aspects of a powder production process, it is necessary for any industrial plant to evaluate the toxicity of the material to be handled. Any good manufacturer will be able to produce a Material Safety Data Sheet (MSDS) stating the characteristics of the powder being produced. Certain chemicals, minerals and active ingredients can pose a serious health hazard to operators if they are not properly protected.
There are several key design elements to take into consideration when sourcing industrial equipment.
1. Dust filtration equipment
One of the most essential pieces of equipment that every manufacturing plant handling dry bulk material needs to invest in is a good quality dust collection system. This is for a variety of reasons but mainly to help prevent an atmosphere that could foster and explosion, as well as keeping the work environment healthy for your operators. There are several methods to filtering dust in a powder processing plant.
First, and most common, is a centralized dust collection system. Centralized dust collectors are typically used as a common collection point for the entire manufacturing process within a plant. It will be connected via a pipe network at several key production points (i.e., milling, mixing, filling, etc.). The dust is separated from the air flow by means of filter elements with flat or folded pockets, oriented either horizontally or vertically within the housing unit. Reverse jet pulses, or pneumatic counterflow of compressed air, is used as an air cleaning system to knock dust build-up off the filters. The fine particles from the cleaning cycle can be collected in a hopper underneath the housing and recycled back into the process to minimize product loss. A blower fan, sized according to the system requirements, provides the vacuum required to pull dust from the production process.
Dust collectors can also be built directly into the process equipment. For example, bag dump stations (also called sack tip trays) can be supplied with a dust filtration unit built directly on top of the equipment. The design of integrated dust filtration units is similar in principle and functionality when compared to central dust systems, just on a much smaller and concentrated scale.
Suction booths are another type of equipment utilized in the containment of powders and bulk materials. Weighing and packaging work stations will sometimes utilize this type of equipment where an operator may need work openly with the material, but pulling an atmospheric vacuum around the work station keeps the area dust and contamination free.
For directly loading dusty materials into tanks, hoppers and totes, dedusting rings can be used around the loading point. The concept is quite simple, consisting of an extended flange with a small tray to rest a bag or bucket for tipping. A pipe is connected to a dust collector to allow the vacuum to pull any dust through the ring, keeping the surrounding work atmosphere clean.
2. Glove Boxes
There is no better way to protect your workers from exposure to toxic dust and fumes then a physical barrier. Glove boxes are used in various industries from pharmaceutical, chemical, mineral and more. The design concept typically involves a glass window (or hinged door) on a steel housing unit. Two holes are cut in the glass to allow elastomer gloves (latex, EPDM, PTFE, etc.) to be connected directly to the glass. The setup is dust tight and allows operators to manipulate packages for the safe opening and unloading operations of materials into a downstream process. Common examples are the use of a glove box on a bag dump station. The operator will open the glass door to load a 50 lb bag on the internal tray. The door is closed and sealed, and the gloves are then used to cut open the sack of powder and dump the material into the discharge hopper. The connected dust collection will remove any fine particulates from the inside of the chamber, allowing the operator to safely open the door for the next bag. Glove boxes can also be used on big bag unloading stations.
Usually, these types of unloading points will use a simple unlacing cabinet so an operator can reach through and untie the big bags discharge spout to release the material. Similar to the sack tip tray example, a cabinet with a glass access door and attached gloves allow the operator to untie the spout without any risk of being exposed to the material.
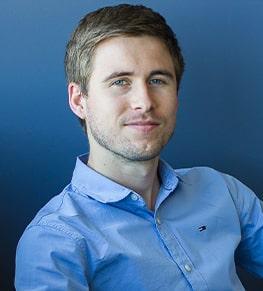
Do you handle toxic materials?
I am available to advise you.
Guillaume, powder expert
3. Containment housing
For larger process systems, a physical containment cage can be setup to surround the production equipment. It is a similar principle compared to glove box style process equipment.
Equipment suppliers can setup plexi-glass walls that help keep the material from spreading out and around the facility work area. This type of feature is especially useful when the material is toxic to the health of your workers. Other types of designs can include a steel sheet housing with hermetically sealed access doors and windows. As always, the intention behind this type of design is to keep operators from coming into contact with the powder and dust exposure. Here is a common example of plexi-glass containment on a big bag discharge station with swing-away access doors to allow the big bag to easily enter the unloading station.
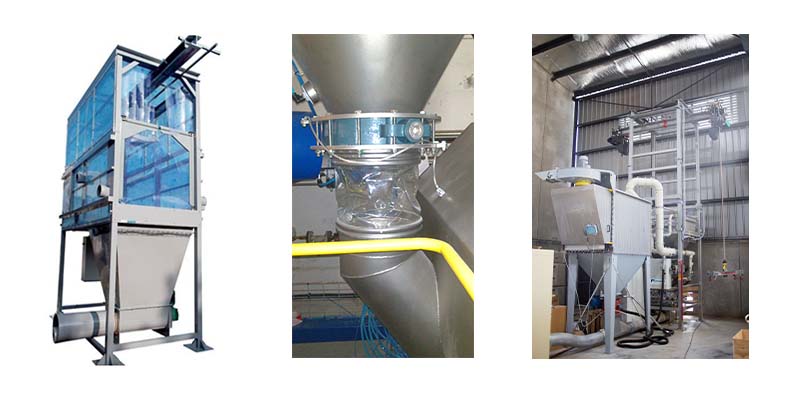
4. Seals and connection types
There are so many types of dust tight seals and connections, one could literally write a paper on that subject alone. But to briefly name a few examples to illustrate the point, let’s start with inflatable connection seals. Industrial equipment suppliers will often utilize inflatable seals on container filling equipment.
In the application of big bags and 20 kg sack filling, an elastomer type hollow ring material will be attached to the outlet of the filling station. When an operator places the fill spout of a big bag or paper sack onto the fill head, a pneumatic air supply inflates the seal to firmly secure the connection of the container. In this way the bag is both secured and sealed with a dust-tight connection. Once the fill operation is complete, the seal deflates and the flexible container can be removed.
Clamping mechanisms are another method of providing dust tight seals to keep operators from being exposed to free-floating particulates. Using the big bag or 20 kg sack example again, the inlet of the container will be fitted over a fill head. Two half-moon shaped clamps attached to pneumatic actuators will swing down and surround the inlet spout of the flexible container and firmly clamp it in place, preventing any possible dust backwash while material is flowing into it.
For 30 years, Palamatic Process has provided equipment to over 2000+ installations in over 30 countries. We offer knowledge and expertise in all manner of powder and bulk automated material handling needs. Examples include, pneumatic conveyors, screw conveyors, turnkey solutions, big bag filling, big bag unloading, bulk material handling, powder processing equipment, food-grade design, etc.
Contact one of our experts today for assistance with your material handling solutions, or to request a quote.