Description
The SackBot 130 for sack emptying: precision, cleanliness, and safety to enhance your productivity.
The SackBot range, encompassing models 110, 120, and 130, has been designed to address modern challenges in sack handling and emptying in the most demanding industrial environments.
Whether dealing with fine powders, granular products, or complex materials, SackBot robots stand out for their precision, efficiency, and ability to seamlessly integrate into various production lines.
From processing plastic granules to fine and challenging powders, each model offers tailored solutions to meet specific industrial needs, improving productivity, reducing operator risks, and ensuring optimal production flow continuity.
-
Automation5
-
Hygiene5
-
Rate4
SackBot 130: A Robotic Solution to Enhance Your Industrial Performance
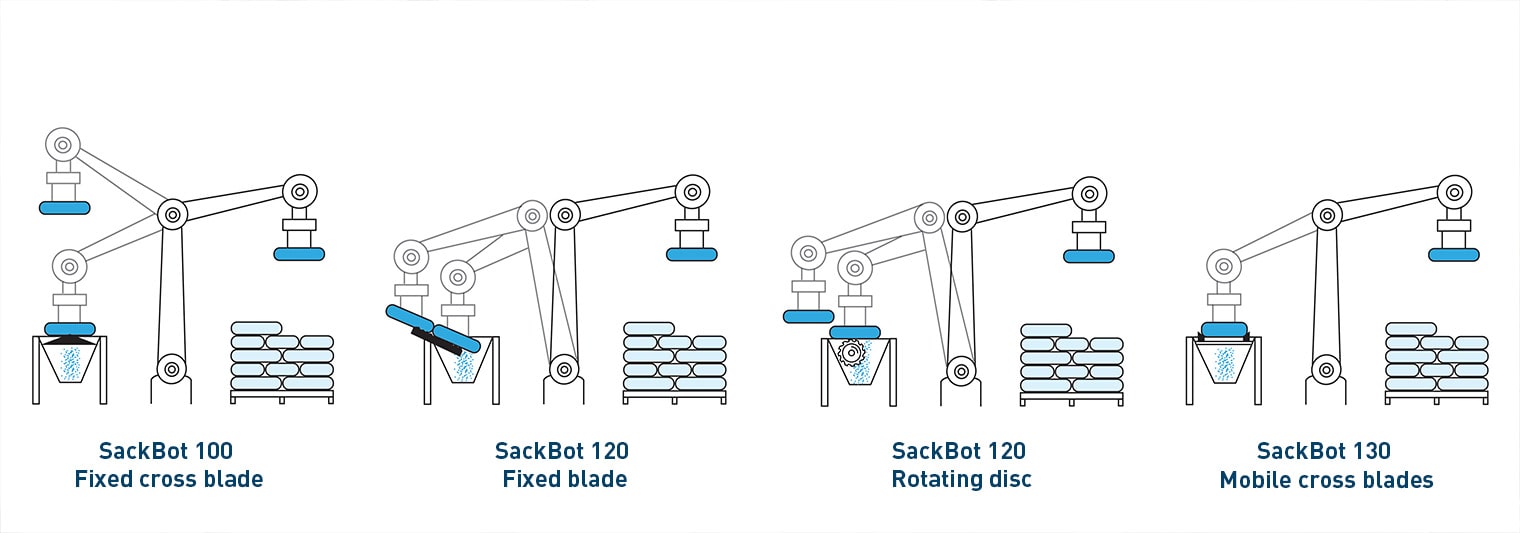
A Comprehensive Range of Robots for Diverse Needs
The SackBot 130 is the most advanced model in the range.
Engineered to handle the most complex powders and a variety of sack types (excluding woven bags), this robot features cutting and emptying technology that ensures consistent and flawless results.
With its cross-positioned mobile blades and precise gripping system, the SackBot 130 can manage a wide range of powders, even those with hygroscopic or compact properties.
Robots That Transform Your Industrial Processes
- Increased Operational Efficiency: With a throughput of 1 to 2 sacks per minute and residue-free cutting, the SackBot 130 optimizes the flow of your raw materials, enabling continuous and seamless production.
- Impeccable Hygiene: The stainless steel design ensures full compliance with food and pharmaceutical standards, reducing the risk of contamination.
- Risk Reduction: By minimizing manual handling, SackBot robots reduce hazards for operators while boosting their productivity.
Variants of Gripping Systems
Variant | Pallet Detection Method | Robot Translation Possible | Ideal Applications |
---|---|---|---|
A | Palletization plan | No | Stable configurations |
B | Camera | No | Precise repositioning |
C | Palletization plan | Yes | Expanded fixed zones |
D | Camera | Yes | Complex environments |
Example: The D variant, which combines a camera for sack detection with a translation system, is ideal for dynamic environments with variably positioned pallets.
Customer Benefits with the SackBot 130
Reduction in Operational Costs
By automating repetitive manual tasks, the SackBot 130 minimizes the risks of human errors and accidents, significantly reducing maintenance and safety costs while boosting overall profitability.
A Flexible Solution for Complex Environments
The SackBot 130 is capable of handling a wide variety of sacks and powders, even those with challenging properties such as high hygroscopicity or a tendency to clump. This versatility ensures easy adaptation to your needs, regardless of your industry.
Protected Operators and Compliance with Standards
The food, chemical, and pharmaceutical industries impose stringent hygiene and safety standards. With integrated dust removal systems and a hygienic design, the SackBot 130 provides a clean, safe working environment that complies with international regulations.
Increased Productivity
With the SackBot 130, your teams can handle a wide range of sacks and powders without interruption. This efficiency gain translates to reduced downtime and a significant increase in production rates.
Guaranteed Compliance and Hygiene
SackBot robots meet the strictest hygiene and industrial safety requirements. Whether for food, pharmaceutical, or chemical products, their design ensures complete powder containment and reduced dust emissions.
Features
Technical Details and Applications
Model | SackBot 100 | SackBot 120 | SackBot 130 |
---|---|---|---|
Product Types | Plastic granules, sand, frozen IQF products | Seeds, grains, kernels | All types of powders, including challenging ones (carbonate, flour) |
Sack Types | Single-layer plastic | Woven sacks and single-layer paper sacks | All types except woven sacks |
Theoretical Throughput | 2 sacks/min. | 3 sacks/min. | 1 to 2 sacks/min. |
Gripping Head | Suction cup with safety claws | Claws | Suction cup with safety claws |
Sack Opening Tool | Fixed cross blades | Fixed or rotary blade (disc); the sack slides over a plate and blade | Mobile cross blades operated by guiding units |
Advantages | Easy cleaning with a fixed system | - Easy cleaning - Easy blade removal - Clean and precise cuts |
Efficient cutting for all sack types |
Disadvantages | Does not accept all sack types | Does not accept all sack types | Lower throughput compared to other models |
Primary Applications for SackBot 130
- Food Industry: Hygienic emptying of flours, powders, and sensitive granular products.
- Chemical Industry: Handling hygroscopic and corrosive materials.
- Pharmaceutical Industry: Ensuring sterility standards for medical powders.
Technical Features of SackBot 130
- Gripping Head: Suction cup with safety claws for reliable sack handling.
- Cutting Tool: Mobile cross blades operated by guiding units for clean, residue-free cuts.
- Design: Stainless steel structure, ideal for applications requiring impeccable hygiene.
Characteristics of Gripping Systems
Gripping System | Key Features | Ideal Applications |
---|---|---|
A |
- Utilizes predefined palletization plans for precise positioning. |
Stable configurations with fixed pallet positions. |
B | Same principle as System A, with an added slide to extend reach. | Dynamic environments requiring greater flexibility. |
C | Integrated vision system for precise sack detection and localization on pallets. | Ideal for environments where sack positions vary. |
D | Combines a vision system with a slide for maximum flexibility and reach. | Large-scale, high-variability operations. |
Descriptions of Gripping Systems
- System A: Simple and Reliable Management
The A system relies on predefined palletization plans, allowing the robot to operate without a vision system. With its range, it can manage up to three different pallets, making it perfect for environments with fixed and stable pallet positions.
- System B: Extended Reach with a Slide
System B improves on System A by incorporating a slide, which extends the robot's range. This makes it suitable for managing a larger number of pallets, ideal for environments requiring greater flexibility and dynamism.
- System C: Precision with Vision
With an integrated vision system, System C detects and precisely locates sacks on pallets regardless of their arrangement. This technology minimizes gripping errors, optimizing productivity and ensuring efficient handling.
- System D: Maximum Flexibility and Precision
System D combines the benefits of Systems B and C, pairing a slide with a vision system. This dual capability allows it to handle sacks across a wider range of pallets, making it the optimal choice for complex, large-scale operations.
Why Choose Palamatic Process for Your SackBot Robots?
Recognized Technical Expertise
At Palamatic Process, we understand the unique challenges faced by modern industries. This drives us to develop custom equipment, like the SackBot range, designed to meet the highest standards of safety, efficiency, and regulatory compliance.
Tailored Solutions for Every Client
By collaborating with our experts, you gain an in-depth analysis of your needs, ensuring seamless integration of the SackBot 130 into your production line. Our robots boost productivity while maintaining impeccable quality standards.
Comprehensive and Continuous Support
From feasibility studies to post-installation maintenance, our team is dedicated to maximizing the performance of your equipment. This commitment ensures a quick return on investment and long-term satisfaction.