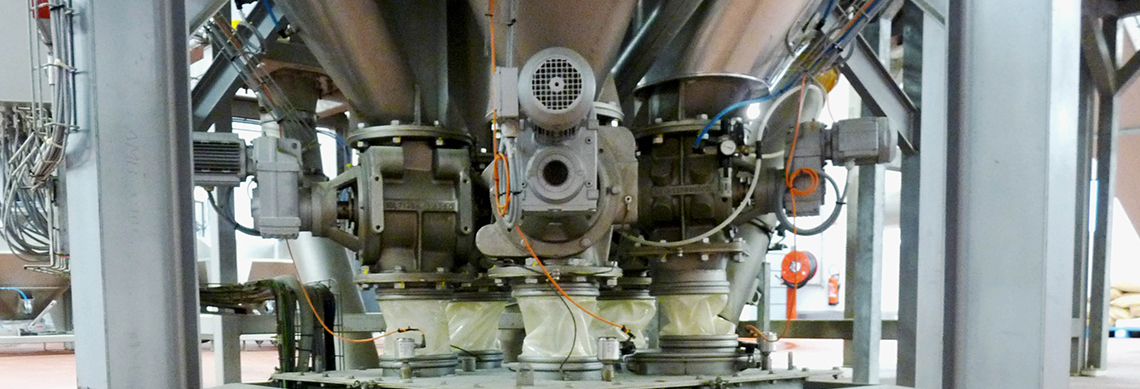
One of the most important components of any powder or bulk solids handling process is the rotary airlock valve. Simple in construction, yet modifiable to fit almost any industrial application, the rotary feeder plays a vital role in material handling and transfer.
The typical rotary airlock valve configuration is an outer housing assembly with rotating airlock valves welded or fused to a central drive shaft. The vanes form pockets that allow material to fill each pocket gravitationally from the top of the inlet. A chain drive or direct drive motor rotates the central shaft, which presents each pocket to the inlet for material filling, and empties the powder or granules at the bottom outlet.
When using a VFD (variable frequency drive), the rotor speed can be adjusted, but the valve speed will be limited to the required bag filling capacity. In other words, the faster the valve rotates, the less efficient the filling capacity of each bag will be, which ultimately results in a decrease in efficiency at the maximum valve feed speed.
In this article, we will look at the 3 most common applications for which rotary valves are used in industrial processes.
1. Providing a pressure differential airlock for the feeding of a pneumatic conveying system
Probably the most common use for a rotary valve is the ability to safely introduce bulk material into a dilute or dense phase pressure or vacuum conveying systems. Rotary airlock valves are designed with extremely tight tolerances between the rotating vanes and the valve housing, sometimes within .004 to .006”. Even though a rotary valve may not be air tight, it creates enough of a barrier to significantly reduce any pressure escaping from the conveying system below.
Typically, these valves are used below silos, hoppers, IBCs and bulk bag unloading stations where gravity is used to discharge the material via the pocketed vanes of the valve.
As the valve spins, it seals against the pressure differential and allows material to drop safely into the conveying stream. This specific design loans the moniker of “blow through rotary airlock valve” since the conveying air is literally blowing through the drop stream below the valve.
Because the pressure of the conveying line will seek the path of least resistance, as the material discharges from each pocket it can be replaced with pressure. As the pocket spins back to the inlet for receiving more material the pressure can escape into the storage vessel above.
Over time this pressure can build up and cause operational issues or even equipment failure.
Two methods can be used to solve this problem of pressure back up.
- One method is to put a degassing vent directly on the return side of the rotary housing assembly and connect to a central dust system.
- The other would be to use a reverse air jet filter directly on the storage vessel feeding the valve. Either method will prevent back pressure build up as the valve turn.
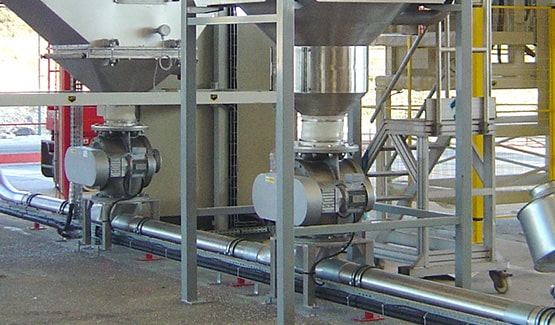
2. Unloading fines from a dust collection system
In order for a dust bag house to function properly, it must contain a vacuum at all times to pull the fine particulates from your upstream process. Not isolating the vacuum will cause a major loss in the efficiency of the central dust system. As the filter cartridges become overloaded and blocked up with dust, a pulse of high-pressure air set to a timing mechanism will send a shock blast down the length of the filters.
This blast of air knocks the build-up of dust off the filters as part of regular cleaning maintenance in sequenced time. As the heavier fines fall from the cartridges, they collect at the bottom of the central dust house.
There are only two ways to extract the dust build up as it falls from the filters:
- The first one consists in shuting down the dust collection system to open the hopper and unload the fines into a collector (bulk bag, sack, drum...)
- The second one consists in using a rotary airlock valve to maintain the vacuum seal and discharge the fines without having to shut off the dust collection system. Using a rotary airlock valve to unload the fine particles provides the pros of minimizing the need for down time in your process as well as reduce the need for operator intervention.
This method of maintaining the vacuum via a rotary valve can also be used in processes where the manufacturer may want to reclaim the fines for a high value item and recycle back into the upstream process for product reclamation.
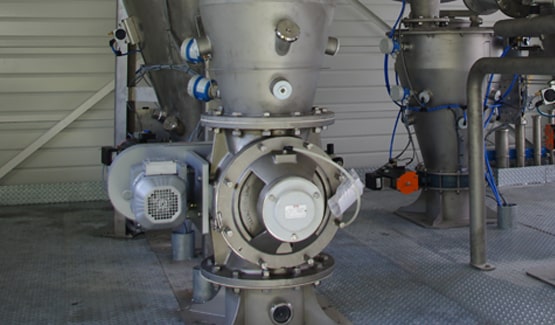
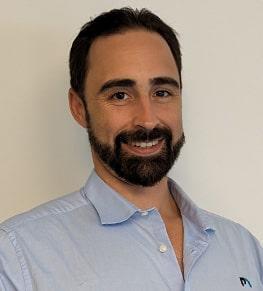
If your require further assistance,
I am at your entire disposal.
Tarik, powder expert
3. Feeding Processing Equipment
Most industrial processes will make use of mechanical process equipment to add value to the material they are manufacturing.
Sugar manufactures may want to mill granulated sugar to a finer confectionary or powdered sugar for the baking industry.
Pharmaceutical companies will want to blend their inactive and active ingredients. Mineral companies may want to create multiple grades of lime powder by classifying and screening their materials. All this value adding equipment have one thing in common, they need a controlled feed to function properly.
Cone mills, pin mill, air classifier mills, jet mills all need a steady rate of material flow to effectively grind the material for adding value to market.
Rotary valves can be used as a feeder from upstream storage and mixing vessels. If the material is allowed to fully discharge into a mill with no control device, the mill would be flooded and seize up.
Rotary valves are especially useful when utilizing vertical stack up processes. Being compact and simple in construction, they have a preference for multi-tiered processes where material is being unloaded from a hopper or bulk bag via gravity into screening and milling equipment underneath. There are many means of controlling material feed streams, but for gravity flow the rotary valve offers a simple and effective solution with minimal footprint.
Rotary Airlock Valves are simple but yet offer diversity in design, modifications and construction. They can be used in almost any application where powders and granular material are involved. Some examples included, food materials, pharmaceuticals, chemicals, wood chips, recycling, etc.
Changes can be made to the shape and size of the rotary pockets as well as the inner lining to handle high temperature and abrasive materials.
In order to determine what type of rotary valve is best suited for your application, contact one of our Palamatic Process experts. Together we can design and recommend the best valve for your process solution.
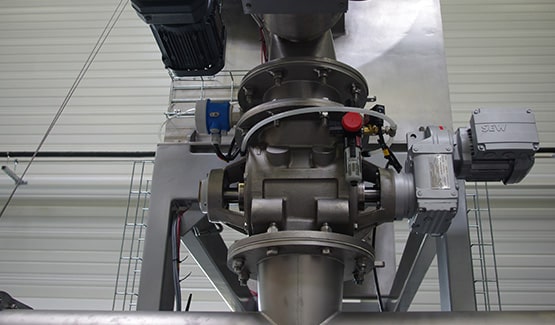