Ice sugar manufacturing unit
4 models available: PalSugarIce® 25, PalSugarIce® 100, PalSugarIce® 200, PalSugarIce® 350
Icing sugar production line from crystal sugar and incorporation of anti-caking agent.
Food and pharmaceutical grade sugar for immediate use or packaging.
- Capable of fine particle production 99% <90µm
- ATEX 20-22 standard
- Low energy consumption
- Hygienic design
The sugar grinding line is composed of a crystal sugar silo, bulk bag or sack tip unloading, feeding and dosing system to the grinding mill, a dosing storage assembly for anti-clumping (starch or potato starch) dosed at between 1.5 to 3%, a pin mill, a threshing hopper, an icing sugar extraction and a dust collection set.
Models
PalSugarIce® 25 | PalSugarIce® 100 | PalSugarIce® 200 | PalSugarIce® 350 | |
---|---|---|---|---|
Production flow
|
250 Kg/hr* | 1 000 Kg/hr | 2 000 Kg/hr | 3 500 Kg/hr |
Grain fineness capacity
|
70 to 600 µm | 70 to 600 µm | 70 to 600 µm | 70 to 600 µm |
% anti-caking agent - starch / starch that can be introduced | 0 to 5%** | 0 to 5%** | 0 to 5%** | 0 to 5%** |
Materials of construction | Steel, 304L stainless steel, 316L stainless steel | Steel, 304L stainless steel, 316L stainless steel | Steel, 304L stainless steel, 316L stainless steel | Steel, 304L stainless steel, 316L stainless steel |
Power installed on the complete line | 10 Kw | 25 Kw | 45 Kw | 85 Kw |
Compressed air flow | ||||
Air treatment flow | 800 | 2 000 | 4 000 | 5 800 |
* given for an output particle size <125µm
** Standard average application between 1.5 to 3% starch for standard starch sugars. Starch levels can be increased depending on sugar moisture levels and climatic temperatures at the installation location if temperature control is not ensured.
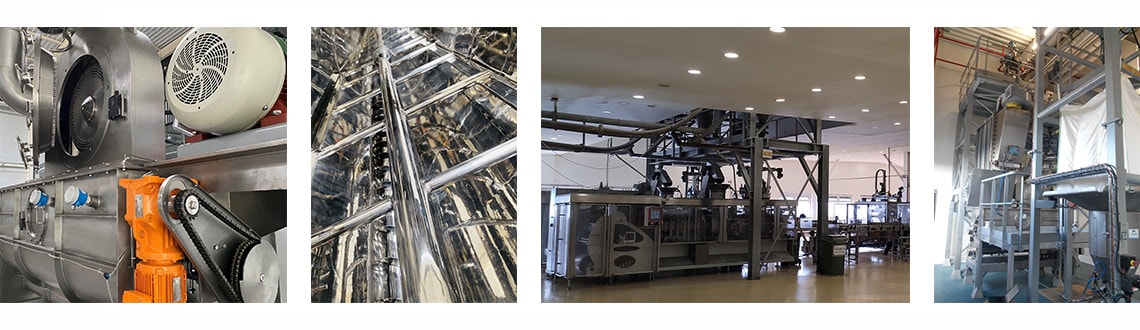
Milling technology
The grinder used for the manufacture of icing sugar is a pin mill with rotating plates. This technology makes it possible to reduce the granulometry of the sugar by shattering the particle. Moisture control during the reduction phase is achieved by dosing the starch via the screw feeder as well as the threshing hopper.
The threshing hopper, sized according to the PalSugarIce® model selected, provides the temperature drop buffer of the freshly milled sugar. Stirring of the hopper is provided by a rotating unit with straight blades.
Line automation
The control of the grinding line offers the operator the selection of the desired particle size, the desired flow rate and the amount of starch to be introduced.
Typical applications
Palamatic's PalSugarIce® grinding lines are widely used in industrial chocolate factories, sugar manufacturers, industrial bakeries and even the confectionery industries. The icing sugar produced on the PalSugarIce® Palamatic Process line is ideal for making meringues, chewing gum, chocolates, ice cream, icing, nougat, macaroons, caramel, etc.
The grinding line is ATEX 20-22 certified.
The air treatment and management of the dust collection line is fully integrated by the installation of a filtration assembly.
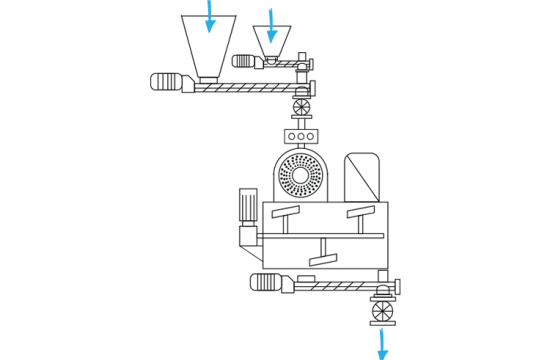
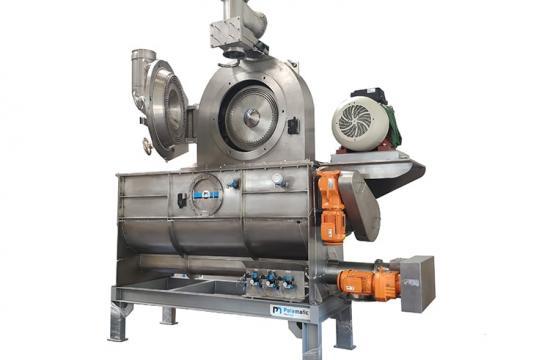
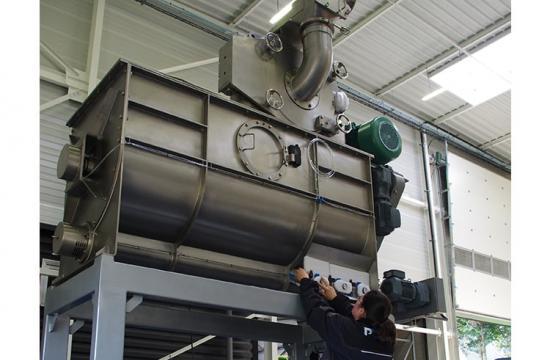
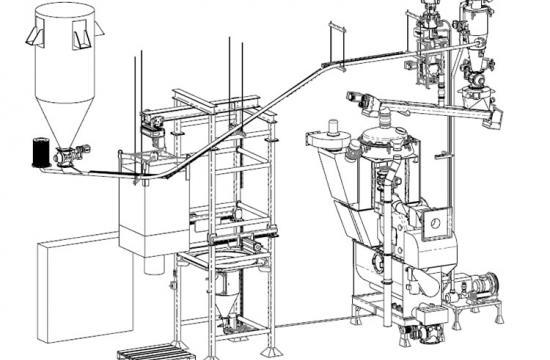
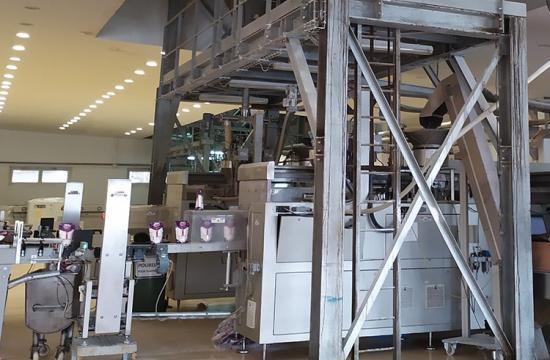
Discover the installations of our customers using the PalSugarIce® powdered sugar grinding line.
All the equipment integrated in the powdered sugar production unit is available below.