1. The characteristics of the bulk bag
When selecting the right type of bulk bag filling station, we first need to consider the physical characteristics of the bulk bag to adapt the station design accordingly.
1. Unique or variable size and bulk bag capacity: The big bag hanging apron height adjustable via a piloted pneumatic cylinder. This adjustable structure makes it possible to efficiently condition bulk bags of different heights, depending on the densities of the materials. Manual adjustments are also possible, both in height and in width, by adjusting the center distance of the forks. An optimal width adjustment is essential to ensure efficient big bagging and stability of the container on its pallet.
2. 4 handles or 1 handle depending on the industrial sector.
2. Process Requirements
1. Define the desired fill rate to select the equipment required for your bulk bag packaging system. (Which equipment to invest in for what type of return?)
Maximum return requires the investment be put into the right type of system. For big bag packaging at very high rates, automation of the filling tasks is integrated and must be carried out effectively while keeping human intervention to a minimum. For example, adding a pre-dosing hopper prepares the next dose to be conditioned in the bulk bag. This provides a more efficient filling system that allows the packing station to reach higher fill rates.
Also, the addition of a rotating filling head allows ergonomic positioning of the empty big bag by the operator.
2. Gross or net weighing? By installing the station on 4 load cells, it is possible to automate the filling sequence of the bulk bag. A commercial weighing system can be added to certify the weight of the big bag and a label printer can further be integrated to print the certification on a label for packaging.
3. Transport and conveying: Automatic conveyor or manual transport? Forklift or pallet truck, on pallet or by handles (U-shaped forks)? The choice of a fully automated, semi-automated or manual process depends on the desired bulk bag packaging rate.
For a rate of up to 20 bulk bags per hour, manual conveying is sufficient: Hooking the bulk bag handles with forks offers easy loading of the shoulder straps as well as optimized hygiene. Furthermore, we can opt for U-shaped forks to remove the bulk bag without a pallet, by the shoulder straps using a forklift. As part of a more sustained and continuous bulk bag packing rate, up to 60 bulk bags per hour, automation is recommended.
A conveyor system is then added to the station: the loading of the pallets are carried out automatically by means of an automatic pallet unstacker.
The latter ensures, via a series of motorized roller conveyors, the supply of the packaging station with handling pallets. It is necessary to take into account the format of the pallets in order to adapt the dimensions of the unstacker. Motorized roller conveyors provide the transfer of empty pallets as well as loaded bulk bags. Finally, the addition of an automatic bulk bag unhooking system is installed on the filling station in order to remove the package at the end of dosing. In the case of bulk bag packaging on a truck or silo loading handle, new constraints related to the handling of powders must be taken into account.
First, a handling frame supporting the entire bulk bag filling station providing the necessary stability for the weighing system is installed. This type of structure allows safe movement of the entire station by forklift.
The addition of stabilizers is essential to make the bulk bag filling operation more reliable.
Finally, a docking cone, equipped with a inflatable seal and a re-centering hopper, ensures easy and secure placement of the truck loading sleeve.
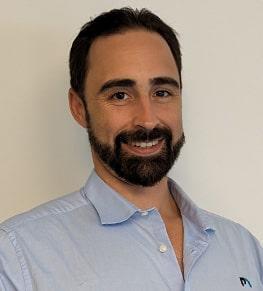
If your require further assistance,
I am at your entire disposal.
Tarik, powder expert
3. Constraints related to the product
1. Industrial sectors:
Depending on the requirements related to the industrial sector, the characteristics of the packing station can differ.
For example in the food, pharmaceutical and chemical sectors, varying levels of hygienic measures and ATEX regulations need to be taken into account.
For the packaging of large quantities of bulk products , mainly dedicated to the quarries, cereal or fertilizer industries, a packaging line for bulk bags with 1 handle loading by manuscopic hoist might be preferred.
Specific equipment for 1-handle big bags must be considered. Our FlowMatic® 08 and FlowMatic® 09 models are suited to this need.
2. Hygienic constraints:
For the treatment of powders and bulk products subject to strict hygienic requirements, a suspended bulk bag filling station would be recommended. The installation of the weighing system directly on the big bag filling head reduces the material retention zones on the floor.
The bulk bag can be replaced by a lifting table and automatic hooks, or by a hydraulic cylinder.
In some cases, in the pharmaceutical and agro-food industry, a structure will be used to fill the bulk bags in a white zone, then extracted to a storage zone. The addition of an airlock closed by two hermetic doors connecting the two areas avoids the introduction of pallets in sensitive areas.
3. Confined packaging:
The double enveloped big bag filling head provides volume balancing and prevents any dust emissions. The displaced air is evacuated via the degassing line which can be connected to the dedusting network. Also important to consider the inflating seal which ensures a tight connection between the filling head and the bulk bag.
4. ATEX regulations:
It is essential to carry out an audit and compliance as well as a risk analysis for the machines and install area.
5. Aeration of the contents:
The addition of a vibrating table allows the deaeration of low density products while giving an optimal shape to the bulk bag. The intensity of the vibrators can be adjusted as needed.
6. Physical form:
The physical form of the packaged product must be taken into account. For example, is the material dusty, granular dense, fluid?
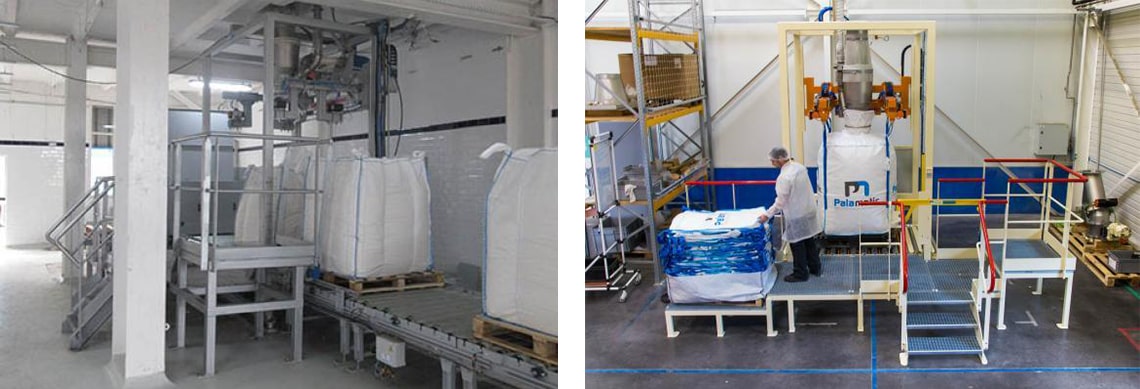
4. Additional equipment
Choosing additional equipment allows a suitable and efficient bulk bag packaging operation for the treatment of your powders and bulk products.
1. Need for a bulk bag shaping pre-forming fan to optimize filling.
2. Air tight sealing of the bulk bag:
An internal welder can be added to the station.
3. Bulk bag containment:
On exiting the bulk bag filling station, an automatic hooding machine provides the final containment of the FIBC on its pallet. It is also possible to install a place mat depositing station between the pallet unstacker and the big bag conditioner. By automatically applying a placemat to the empty pallet, the containment of the big bag is maximum and meets the quality standard of many industries.
4. Operator platform:
The integration of an access platform allows an operator to set up the bulk bag.
5. Manufacturing of the framework
Also, the physical structure must also be judiciously chosen.
1. The manufacturing materials of the support and product contact areas must be chosen according to the process requirements and the packaged products. A stainless steel structure will be suitable in the event of recurrent contact with corrosive materials.
2. Available space:
The available footprint will be taken into account when designing the station.