Discharging drums of raw material powders into loading hoppers is not an easy task when the methods used are not safe or efficient.
To understand which drum tipper to select, we need to define the type of drum to handle, the powders characteristics and the industrial sector of operation.
1. What type of drums to unload?
First of all, you have to define the type of barrel you have to tip.
The packaging in barrels can vary. The main criteria for characterizing the barrels are: weight, diameter, height, manufacturing materials and the presence of an internal liner.
The weight of the drums generally vary between 15 and 350 Kg. The 350 Kg drums are generally used for packaging liquids, but certain powders are also packaged in these “oil drum” type of containers. The metal oil drum is made of steel and its full opening is ensured by removing the cover.
In the pharmaceutical sector, the drums handled are made of cardboard / kraft drums or stainless steel metal drums for internal transport. In this area, the drums incorporate internal bags which prevent the packaged powder from coming into contact with the container.
Full opening plastic drums with a capacity between 30 and 220 liters are very often used in food applications. An internal bag can be used, or desiccant sachets, depending on the product or the powder packaged.
In Palamatic Tipping DrumFlow® applications, bung drums are not supported as these drums remain specific for packaging liquid products. Only handling / lifting / stacking solutions are offered for the bung drum type.
Plastic drums made of HDPE offer the advantage of not presenting any risk of corrosion and are resistant to the risks associated with transport. The lever ring system allows the barrel to be opened and closed easily and completely sealed.
All these types of powder kegs can be handled and tipped on a Palamatic keg turner.
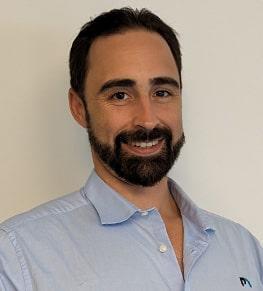
Do you need personal advice on your
drum turner? I am at your disposal.
Tarik, powder expert
2. What type of tipper / turner for my drum?
Tipping a keg, canister or drum can generate dust when the mass is suddenly transferred. Palamatic drum tipper solutions include several options depending on your expectations and handling constraints.
Tipping emptying: the DrumFlow®03 drum stacker station
The unloading of solid bulk products such as olives, kibble or sand barrels can be carried out on tippers without capture of the DrumFlow®03 model type . When products generate little or no dust, it is not necessary to "cap" the barrel before it is tipped. The DrumFlow®03 model ensures the tilting of any type of container by turning up to 160 °. The barrel is positioned on an articulated chair and is held in position by a pneumatic system when the angle of inclination is important. When the product packaged in the barrel incorporates an internal bag, plunging rods hold the bag in order to avoid any risk of falling into the receiving hopper.
Drum emptying by sunction: the DrumFlow®01 drum unloading station
Emptying drums directly from the storage pallet offers a big advantage in handling and operator safety. Reducing the handling of drums is an important issue for operator safety. The DrumFlow®01 drum discharging equipment allows the powders contained in the drums to be vacuumed via a suction rod connected to a pneumatic transfer cyclone. The applications are generally pharmaceutical with the possibility of capping the barrel head in a sealed enclosure. This flexible solution remains applicable for reasonable flow rates of 1 ton / hr.
Emptying by extracting the bag: DrumFlow®02 drum tipper
Unloading a drum with an internal PE bag requires suitable equipment to avoid the bag tearing in the drum! The DrumFlow®02 drum turner solution integrates a pneumatic tipper and an enclosure for extracting the bag. This solution, particularly suitable for drums weighing around twenty kilos, offers great ergonomics and excellent containment for emptying drum bags. Thanks to its unique design, the DrumFlow®02 drum emptying station allows tipping of the drum and a dust tight connection with the enclosure. When the drum is in the tilted position, the operator only has to extract the bag by pulling it out of the container via glove box style containment gloves. The bag is then cut open in the same a sack of ordinary powder is.
Sealed barrel emptying by tilting and styling head: DrumFlow® 04
Tilting a powder keg 180 ° over an open hopper can generate a large amount of dust. To avoid contaminating the drum dumping area, Palamatic has developed a hydraulic drum tipper with a capping head. The styling head is pressed against the barrel when fully opened via a pneumatic cylinder. The seal between the ring of the barrel and the styling head is reinforced by an inflatable seal. The styling head equipped with a butterfly or guillotine valve, after tilting, connects to the feed flange of the loading hopper. The connection between the barrel turner and the hopper is also reinforced by an inflatable seal system.
Palamatic engineers have developed various complementary options to enhance ergonomics and flexibility of use. With these options, the DrumFlow®04 keg turner can empty different types of drums on the same tipping equipment, drums with internal bags and powders with poor flow properties.
Your drum handling application, due to the type of drum and the powders processed, needs a specific solution. Contact our technical service to define the model and options that suit you!