Description
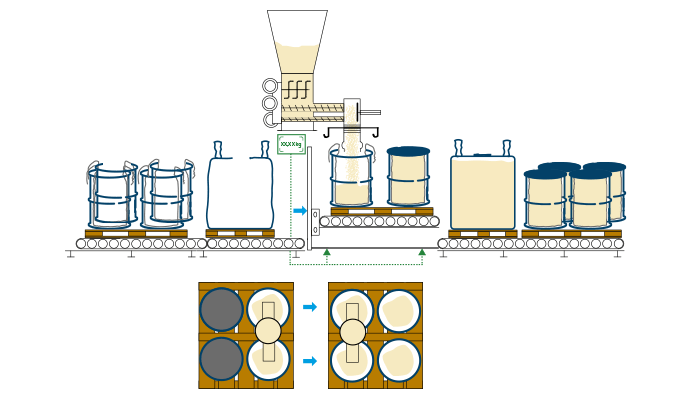
-
Automation4
-
Ergonomics5
-
Containment4
The Paldrum®06 semi-automatic packing line allows for the filling of super sacks and 55-gallon drums on the same powder filling line. Interchangeable filling heads can adapt to the various types of bulk containers.
For bulk bags, an inflatable seal is used for a secure connection between the packaging station and FIBC.
For 55-gallon drums, a diverter valve with twin feed chutes can be fitted onto the packaging station. This method allows for 4 drums on their pallet to be filled, two at a time. Industrial automation allows for pallet feeding, container conveying, dosing and weighing of the products and the container to be filled.
The integrated D14 screw feeder uses dual augers that are independently driven for high and accurate fill rates via gain in weight load cells under the station.
To ensure good flow control and maximum precision, the dual screw feeder makes use of an integrated agitator to provide smooth bulk material flow.
The Palamatic Process pre-weigh systems are accurate to +/- 1% of the target fill weight for bulk bags and drums. A digital scale display provides accurate fill rates in real time.
The entire filling system is mounted onto a support structure. For bulk bags, the operator secures the feed spout to an inflatable seal for dust tight containment and security of the container. The operator simply hangs the bulk bag handles on the forks of the support structure.
For drums, an adaptor plate is hung on the bulk bag forks and clamped onto the filling head. A pneumatic cylinder raises and lowers the drum cover plate with diverter valve. The four empty drums are conveyed and indexed so the first two drums are under the dust cover plate.
The plate is lowered onto the drums and the diverter valve fills the drum in the 1st position. Once the target weight is reached, the diverter valve switches to the drum in the 2nd position. Once both drums on the front of the pallet are filled, the mechanical roller conveyor indexes the position of the pallet so the 3rd and 4th drums are under the cover plate and the filling operation repeats.
Once all drums on the pallet are filled, the roller conveyor moves it to a buffer area so it can be removed by a forklift operator. The conveyor underneath the fill station has an automatic height adjustment via a pneumatic cylinder. The bulk bag, or drum, is raised to an ergonomic level to allow the operator to easily make the secure connections. The conveyor is lowered at the end of the filling cycle.
The different possible configurations of the PalDrum®06 model:
Ref. | Integrated equipment | Functions | Advantages | |
---|---|---|---|---|
Choice 1 | I | Inflatable seal | Secure connection to bulk bag | Maximum containment |
C | Diverter Valve and Cover Lid | Dust containment of open drums on pallet | Ergonomic design, various drum sizes | |
Choice 2 | Loss | Loss in weight | Accurate preparation of the material | Accelerated rate (dosing in hidden time) May require double check weighing |
Gain | Gain in weight | Weighing of the entire container and contents | Commercial weighing, traceability | |
Conveyor | C | Feed and removal | Holding and evacuation of the pallet during packaging | Efficiency and safe operation |
Our PalDrum®06 packaging machine is configurable by modulating the possible basic equipment: choice 1 + choice 2.
Example of possible reference: PalDrum®06-I-C-Loss
Description of choices :
Choice 1: 2 possible container connection types:
To provide clean packaging operations of drums and bulk bags, the PalDrum®06 packaging station offers two connection configurations:
- Inflatable seal: provides a dust tight connection of the feed spout of the bulk bag. The filling head is equipped with a double envelope to allow volume balancing, as well as dust removal during the filling sequence.
-
Containment plate: is actuated by a pneumatic cylinder and pressed against the top of the drums to provide a dust tight connection during the filling phases.
Choice 2: 2 weighing modes:
As with all PalDrum® stations, the weighing technology can be selected according to your throughput.:
- Gain-in-weight: for weighing drums during filling (IPFA commercial weighing certification)
- Loss-in-weight: for weighing your products upstream and checking the weight after packaging on a secondary conveyor (IPFA commercial weighing certification)
Fields of application
Used for bulk filling of 55-gallon drums or 1 to 2 tons bulk bags, this powder packaging system can be configured to fill either by weight, volumetrically, or a combination of both. The PalDrum®06 semi-automated bulk material filing line can be used in a variety of industries such as: food, chemical, pharmaceutical, cosmetic, mineral, and more! This bulk container filling system is available in chemical duty construction and food grade construction in top fill only operation procedures.
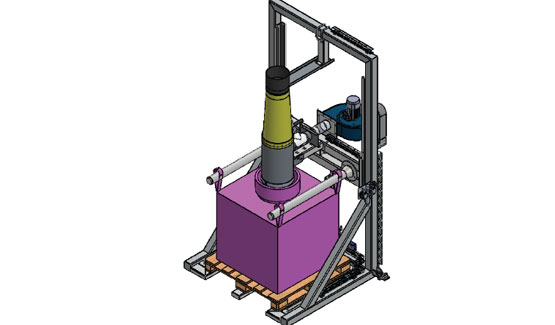
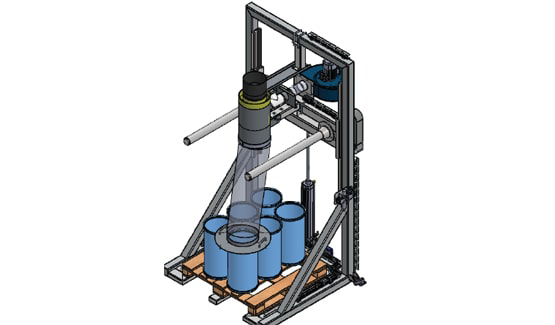
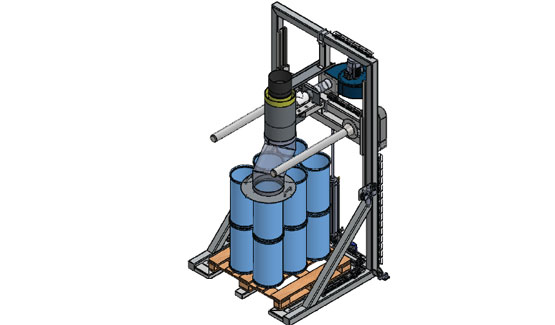
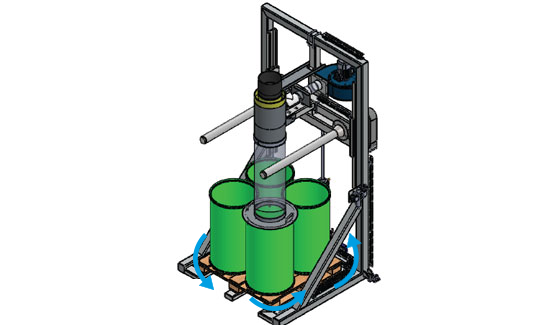
Equipment advantages
- Automatic and accurate dosing of bulk materials
- Adaptable to bulk bags and 55-gallon drums on the same station
- Integrated options for dust containment and dust collection
- Safe handling of drums via palletization
- Stainless steel scale with remote located digital readout
Features
Technical specification
Technical specifications:
- High Flow Rate Dual Screw Feeder
- Gain in weight or Loss in Weight Functions
- Pneumatic stop cylinder for greater dosing accuracy
- Dust tight connection by cover lid or inflatable seal
- Filling head support structure to secure the bulk bag handles on the station
- Diverter valve (bypass valve) for filling two drums, one at a time, while on their pallet
- Control Panel with Digital Weight Display
- Inflatable seal: the inflatable seal ensures a tight connection between the filling head and the container during the filling operation.
- Pallet feeder: the pallet unstacker provides, via a motorized roller conveyor, the supply of handling pallets to the packaging station. The pallet size supported by the unstacker is adaptable.
- Roller conveyor: a series of motorized roller conveyors aid in the transfer of empty pallets to the bulk material packaging station. They are equipped with positioning sensors to ensure a buffer storage of containers at the outlet of the station.
- Height adjustable filling conveyor: the conveyor section under the filling head is capable of automatic height adjustment for raising and lowering the bulk containers for operator ergonomics.
Rate | 20-30 drums/hr or 10-15 bulk bags/hr |
---|---|
Capacity | 500 lbs./drum or 2,000 lbs. bulk bag |
Materials of construction | Painted Carbon, 304 or 316 Stainless Steel |
Accuracy | Possibility of +/- 1% |
Power supply | 480V / 3ph / 60 Hz |
Dust removal rate | 300 m³/hr |
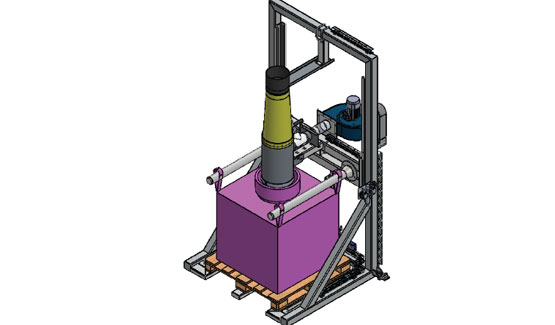
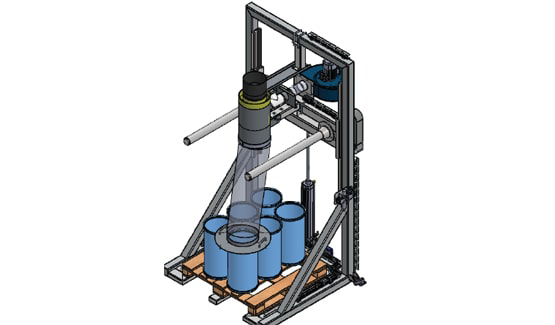
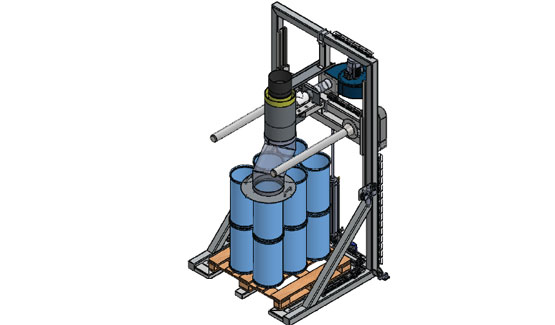
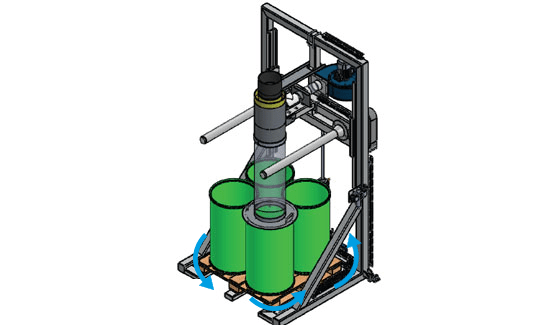