Description
SackBot 210 and 220, optimising the feeding of automatic sack emptying machines
High speed, precision and flexibility for efficient industrial automation.
SackBot 210 and SackBot 220 embody excellence in industrial automation, with a design focus on efficiency, precision and flexibility.
These robots are designed to deliver superior efficiency, precision, and flexibility, making them ideal for optimizing sack-emptying processes.
-
Rate5
-
Rate5
-
Overall dimensions4
Key points of the 200 Series Sackbots
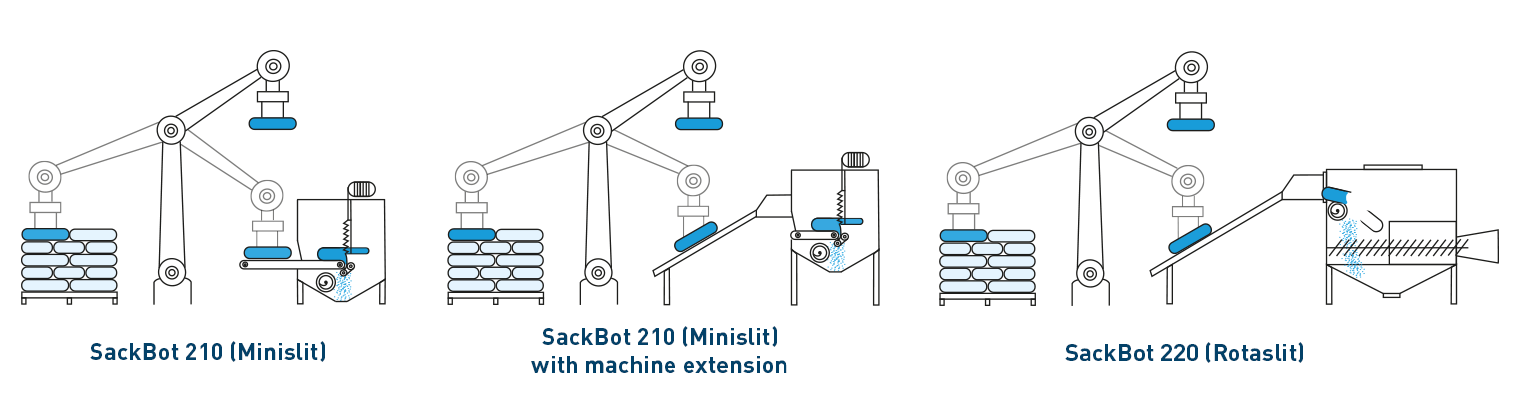
Performance and specialization
- Main Applications:
- Automation of feeding for sack-emptying machines.
- Reliable and continuous handling for optimized production flow.
- Efficiency:
- High-speed operation of up to 8 sacks per minute with the SackBot 250, ensuring increased productivity.
- Adaptable to demanding industrial environments with specific options for diverse materials and sack configurations.
Advanced gripping technology
The robots incorporate gripping systems adapted to the diverse needs of production lines
System A:
- Autonomous operation with preprogrammed palletizing plans.
- Simultaneous handling of up to three pallets.
System B:
- Sliding mechanisms for enhanced flexibility in pallet management and various configurations.
System C:
- Vision technology enabling precise sack positioning to minimize errors.
System D:
- Combined vision and sliding systems for maximum reach and handling of complex tasks.
Industrial benefits
SackBot robots integrate seamlessly into a wide range of industrial applications
- Food Processing: Emptying sacks of powders or granular food materials.
- Chemical Industry: Handling bulk materials like granules and grains.
- Pharmaceutical Sector: Precise and reliable palletizing for sensitive products.
Examples of industrial application
- Sack Emptying: Automation of sack-emptying machines to reduce operator fatigue and boost throughput.
- Palletizing: Accurate loading and unloading of pallets, even in complex environments.
- Diversified Handling: Integration into logistical flows requiring frequent configuration changes.
The SackBot 210 and 220 are ideal for companies looking to automate their handling processes while boosting productivity. Their technological versatility and performance make them invaluable tools for modernising and optimising industrial operations.
If you would like to include additional data or explore specific aspects (such as energy consumption or a detailed use case), don't hesitate to ask!
Here's a summary in table form for information on the SackBot 210 and SackBot 220.
Ergonomic design and reliability
- Ergonomics: Modular design for seamless integration into existing production lines.
- Robustness: state-of-the-art materials and technologies guarantee long-term durability, even in harsh industrial environments.
- Flexibility: Adaptable to a wide range of bags (kraft, PE, plastic, hessian) and contents (fine powders, granules, grains).
Limits to the use of robots
Unsuitable for environments requiring strict control of cross-contamination, limiting their use in certain pharmaceutical and agri-food sectors.
Discover our range of robots and cobots for industrial handling
Equipment advantages
- Increased productivity: High output and reliable automation reduce downtime.
- Precision: Advanced technologies (vision, slides) for optimal positioning and handling.
- Adaptability: Compatibility with various bag types and applications.
- Ergonomics: Smooth integration into production lines and ease of use.
Features
Technical specification
- Bag opening tools:
- Minislit ( SackBot 210): Ideal for fast, efficient cutting.
- Rotaslit ( SackBot 220): Designed for tougher bags or applications requiring more robust cutting.
- Gripping systems: Suction cups or grippers, depending on specific handling requirements.
- Handling capacity: Simultaneous or sequential handling of several pallets thanks to advanced configurations.
Comparison table
Specifications | SackBot 210 | SackBot 220 |
---|---|---|
Main application | Feeding of bag emptying machines | Feeding of bag emptying machines |
Type of bags | Kraft, PE, kraft + PE | Plastics, hessian |
Type of products | All types of powders | Free-flowing powders and granules |
Theoretical output | Up to 6 bags/min | 6-8 bags/min |
Gripper head | Suction cup | Suction cup or claws |
Bag opening tool | Minislit | Rotaslit |
Bag dimensions supported | Varies according to type of gripper | Varies according to type of grip |
Advantages | High speed All types of bags compatible |
High speed Compatible with robust bags |
Limits | Unsuitable for avoiding cross-contamination | Unsuitable for avoiding cross-contamination |
Table of available gripper system
Systems | Description | Ideal applications |
---|---|---|
System A | Pre-defined palletising plans; "blind" autonomy. | Simple flows with little variation. |
System B | Use of slides to extend the robot's reach. | Configurations requiring greater flexibility. |
System C | Vision technology for precise location of bags on pallets. | High-precision environments. |
System D | Vision and slides combined to maximise reach and precision. | Complex processes and varied logistics flows. |
Summary of advantages and limitation
Aspect | Advantages | Limitations |
---|---|---|
Performance | High output and continuous flow. | Not suitable for sterile environments. |
Flexibility | Compatible with various types of bags and materials. | Adjustments required for complex environments. |
Advanced technology | Integration of vision systems and slides. | Potentially complex initial configuration. |
Ergonomics | Easy integration into existing production lines. | Specific to certain applications. |
Typical application
Sectors | Example of use |
---|---|
Food industry | Automatic emptying of bags of flour, sugar or food granules. |
Chemical industry | Handling and feeding of bags containing chemical powders or granules. |
Pharmaceuticals | Automated palletising for products requiring precise handling. |
Case studies
CASE STUDIES WITH THIS EQUIPMENT
Secure automation of the emptying of drums of ammonium perchlorate in the aerospace industry with the DrumBot 300
Treated powders: ammonium perchlorate Secure automation of the emptying of drums of ammonium perchlorate in the aerospace industry with the DrumBot 300Defense