A customized solution to automate the unloading of bulk bags for a world leader in the production of high-purity quartz.
Processed powder: Quartz
Our customer is a world leader in the production of high-purity quartz. This highly purified quartz is used in applications such as microelectronics, semiconductors, renewable energies and fine chemicals. Our customer extracts the mineral in the USA, then processes and purifies the material with various types of acids to remove impurities at their plant in Norway.
The customer wanted to expand their production, which was manual, with a fully automated system adapted to the production environment. To achieve this goal, they called on Palamatic Process's expertise to design and implement a solution that was both efficient and respectful of the current environment.
Customer's main objectives
- Expand production from manual to fully automatic
- Achieve a high output of 20 bulk bags per hour
- Ensure a sufficient volume of bulk bags in automatic conveying, allowing the operator to perform other tasks in parallel
- Implement a flexible system that could handle bulk bags stacked 2 by 2, or single bulk bags on a pallet
- Automatic stacking of pallets
- Avoid dust generation outside the emptying area
The solution
The standard version of the EF500 automatic bulk bag unloading station met most of the customer's requirements. Stacking the bulk bags on top of each other presented a new constraint to which our teams had to innovate and adapt the existing system. In order to integrate this feature into our design, a system for grasping the top fabric of the bulk bag was developed for the automatic emptying system.
Additionally, we had to adapt to the pallets, as these did not comply with standard dimensions and were difficult to handle and transport. All this was taken into account to design a tailor-made solution that perfectly met our customer's needs.
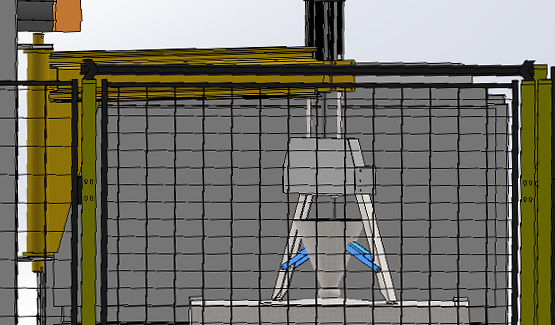
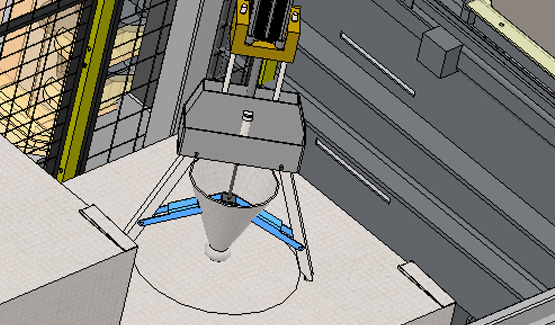
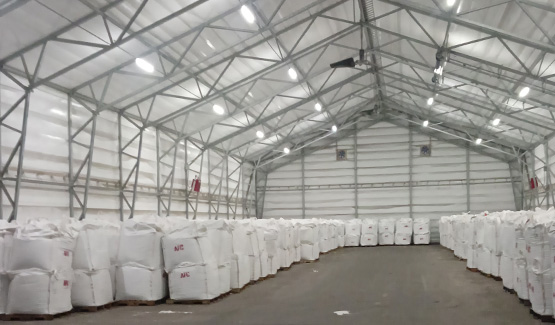
High output and enhanced reliability
The results achieved by our customer lived up to their expectations, highlighting the innovative skills of our teams. The proposed machine was tailor-made, adapting to the specific requirements of the customer, including the handling of bulk bags stacked 2 by 2. The solution made it possible to keep up with the high production rate, while offering greater reliability and avoiding the need for frequent maintenance downtime.
Transition to automation
How Palamatic Process designed a customized solution for its customer
The automated bulk bag discharge solution allowed our customer to make the transition to a fully automatic and hydraulic process, while guaranteeing the robustness and reliability of the production line. This tailor-made solution, designed in close collaboration with our customer, enabled us to maintain a high output of 20 bulk bags per hour. As a result, we achieved significant savings in terms of production time and costs. Thanks to a specially designed gripper system, the machine can handle and empty stacked bulk bags. The results achieved by our customer testify to Palamatic Process's expertise in industrial process automation and the design of customized solutions.