Description
High-speed, automated bulk bag unloader station - FlowMatic® EF500
Automatic deconditioning, hydraulic gripping of the bulk bag without operator intervention.
The super sack discharging station is fed by a set of motorized conveyors that supply the hydraulic gripper. A pallet stacker is integrated to evacuate the empty pallets once the bulk bag is lifted by the gripper. The only manual intervention required for the Flowmatic EF500 system are the unloading of the stacked pallets and loading of the bulk bags to be emptied, via forklift operation.
Autonomous handling of the bulk bags is done by the hydraulic gripper system, mounted on a bridge crane, which transfers the bulk bags from the conveyor to the discharge hoppers. Once empty, the bulk bag is automatically discharged to a baler or bulk bag compactor.
Operation mode:
1. Bulk bags loaded by a forklift on the motorized roller conveyor line(s) (several lines = several products possible for recipe formulation, with "picking")
2. Automatic management of the accumulation (storage and advancement) of the bulk bags via discharging by the supervision automaton.
3. Automatic selection of the bulk bag to be emptied on the dedicated conveyor line (in applications requiring recipe management)
4. Automatic transfer of the loaded bulk bag by the hydraulic gripper mounted on a motorized trolley (handling crane)
5. Automatic bulk bag feed above the discharging station
6. The containment doors of the EasyFlow® EF500 Bulk Bag Discharging Station enclosure open and close automatically to ensure maximum containment during the big bag breaking phases (the containment enclosure is optional).
7. Lowering of the bulk bag onto cutting blades for automated opening
8. Management of the pressure of the hydraulic clamp during the bulk bag discharging / breaking phase
9. Automatic feed + automatic release of the bulk bag into the baler or bulk bag compactor
10. Management of the empty pallet: automatic transfer to a pallet stacker
11. Automated gripper return positioning for the next bulk bag
-
Rate4
-
Automation5
Cutting of the bulk bag:
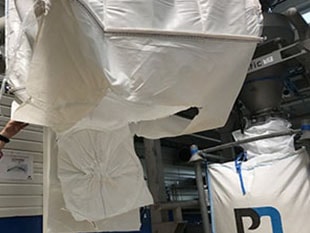
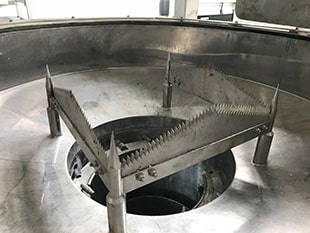
The bulk bag is opened via cutting by cross or "U" shaped blades depending on the bulk bag design. For bulk bags with an outlet spout, the cutting system will be a "U" shaped system. Bulk bags with no discharge spout are cut by cross or diamond points as a preference.
For difficult flowing products, massage cylinders can be installed on the discharging station. These hydraulic or pneumatic massage cylinders can be used to force the extraction of the product.
Bulk bag gripping clamp :
The bulk bag gripper is the heart of the Palamatic Process EasyFlow® EF500 system. This gripper has its own hydraulic unit. It is designed with a double clamping system to hold both full and empty bulk bags. This double clamping system is fully synchronized and remotely controlled with a chain of safety sensors depending on the cycle. This hydraulic bulk bag handling clamp makes the presence of an operator on the discharging station unnecessary. The movement of the clamp at the different stations is as follows:
1. Gripping of filled bulk bags
2. Cracking hopper / FIBC discharge
3. Drop zone: bulk bag compactor, waste bin or baler
This displacement is managed automatically by a positioning system supervised by the PLC.
This automatic bulk bag discharging system integrates a large number of features specific to each of our customers. Do not hesitate to contact our pre-project department to study your automatic bulk bag discharging solution.
Equipment advantages
- No operator
- Automatic cutting
- Automatic bulk bag gripping
- Automatic bulk bag opening
- Automatic bulk bag discharging
- Automatic evacuation of the emptied bulk bag
Media
View our equipment in videos
Gripping by hydraulic clamp - EF500
View our equipment in photos
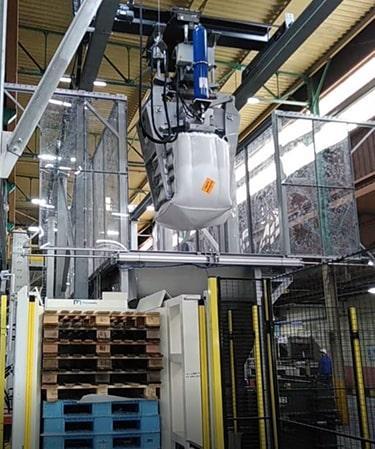
Hydraulic clamp for discharging
Bulk bag gripping by hydraulic clamp.
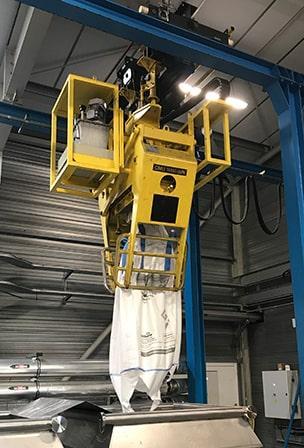
Secondary jaw for big bag discharge
Bulk bag discharged automatically and held by the secondary jaw.
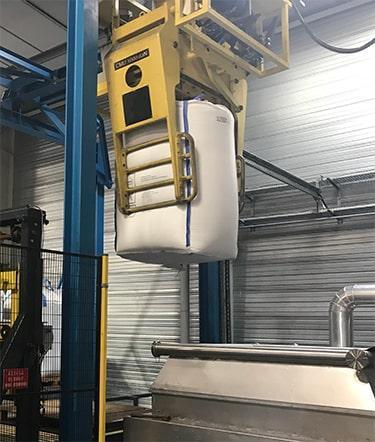
Automatic bulk bag emptying clamp
Gripper for 100% automatic bulk bag discharging.
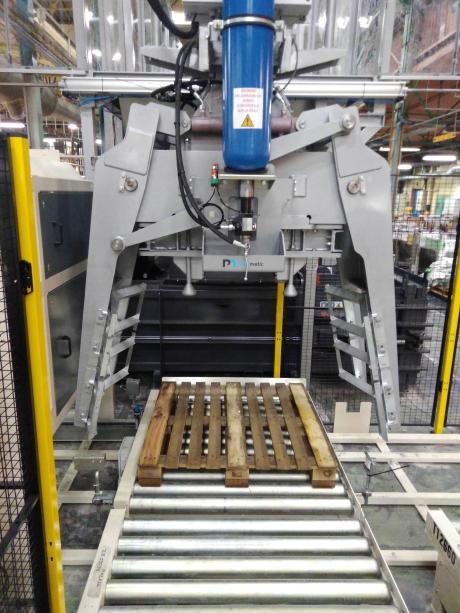
Roller conveyor
Clamp for bulk bag gripping and discharging.
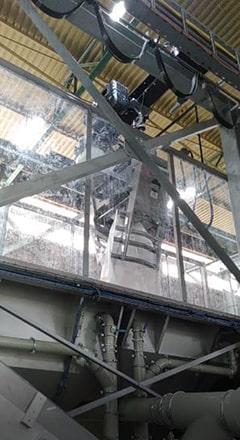
Dust removal from the bulk bag emptying system
Dust collection network for the whole bulk bag emptying system.
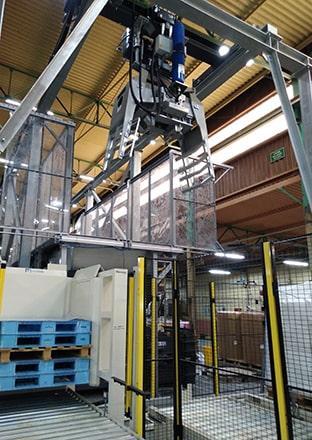
Pallet stacker for bulk bag unloading
Pallet stacker on conveyor feeding the bulk bag emptying system.
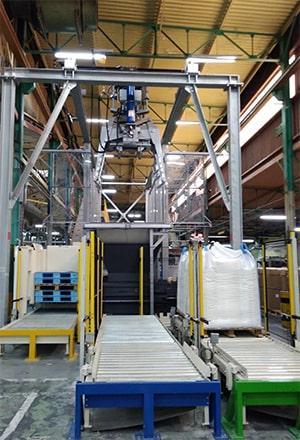
Contained and hig rate rate bulk bag emptying system
Complete contained high rate bulk bag emptying system.
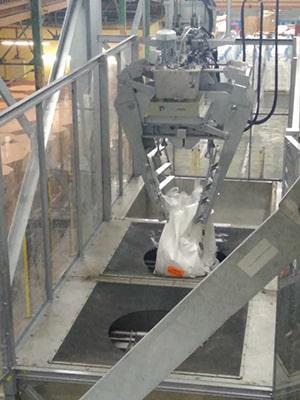
Discharging the bulk bag
Bulk bag unloading thanks to an hydraulic clamp EasyFlow® EF500.
Features
Technical specification
Rate | 1 to 25 bulk bags/hr. |
---|---|
Manufacturing materials | Painted steel, 304L stainless steel, 316L stainless steel |
Finishing touches | RAL 9006, micro-blasted, electropolishing |
Installed power |
- Pneumatic 6 bar - Hydraulic - Electric 400 V - 50Hz - 5 to 10 Kw |
Required dust collecting rate (optional) | 3,000 m³/h. |
Maximum dimensions of the bulk bags (length* width * height) |
1,100* 1,100 * 1,200 mm |
Lifting capacity | 1 000 daN |
Bulk bag gripping | Hydraulic clamp with 2 synchronized arms |
Options
Case studies
CASE STUDIES WITH THIS EQUIPMENT
High-rate bulk bag unloading system for the plastics and polymer industry
Processed powders: PET resin granules and PET flakes - Fully automated big bag discharging line - Big bag compaction at the end of the lineInsect breeding
Quartz production process
Processed powder: Quartz - Quartz production process - A customized solution to automate the unloading of bulk bags for a world leader in the production of high-purity quartz.Energy
Nickel hydroxide production process
Processed powder: nickel sulfate - Tailor-made solution to increase nickel hydroxide production in response to growing demand for electric vehicle batteries.Energy
Optimizing automated bulk bag discharge for lithium powders
Powders handled: Lithium carbonate (Li₂CO₃), iron oxide (Fe₃O₄), lithium Optimizing automated bulk bag discharge for lithium powders.Energy