Processed products: spices
Preparation of spice mixtures
The company is a spice mixture manufacturer.
The objective is a spice blending line with easy to clean equipment and recipe flexibility.
Palamatic Process' goal in this project was to design an entire spice blending line for maximum flexibility in recipe formulation. Over the course of 4 days of spice recipe production, the customer wished to have the capability of progressively increasing the taste and color profiles. The last day of production would be reserved for cleaning and drying the mixing line.
In order to ensure the flexibility of the line, the system design choice integrated stainless steel containers. A set of 100 containers of different capacities were ordered by the customer. These containers are used to make the pre-weighed products as well as the premixes. A container mixer (IBC tumbler blender) ensures dry mixing, and a horizontal mixer with Palamatic-EasyClean features provides mixing with the incorporation of liquid (oils and additional flavors).
Due to the varying demands of end users, our customer wanted several packaging lines to offer the custom formulation blends for each type of end product.
The spice blending line can supply finished product packaged in bulk bags, as well as blends packaged in 25kg bags - Bag filling PalSack®01 - and bags of various weights. Our team also integrated a packaging line for buckets and small bags.
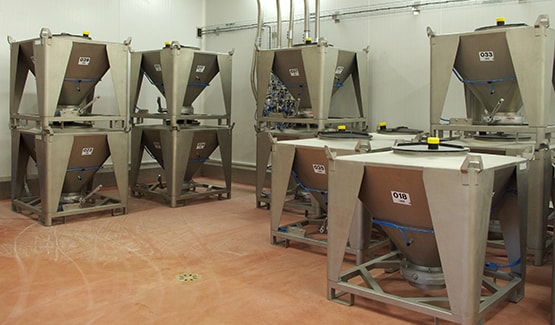
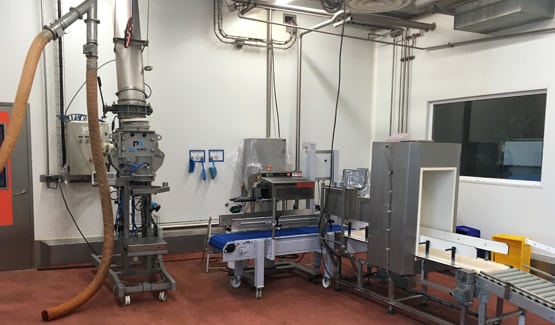
These spice sachets can be directly used in meat processing cutters.
The stainless steel containers are cleaned after each use in a dedicated washing room which facilitated changes in manufacturing without the need to stop production.
In addition, a clean in place network was used on all "fixed" processing equipment. A technical room holds the water tanks for the different cycles: pre-washing, washing, rinsing. Forced hot air was used to provide the drying phase of the equipment.
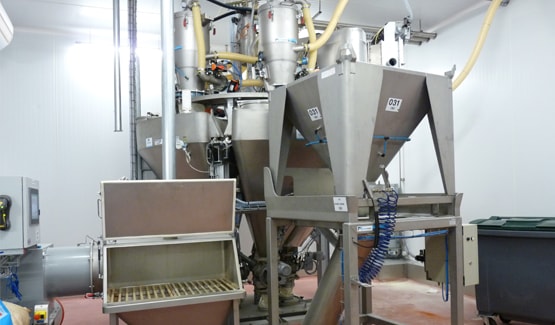
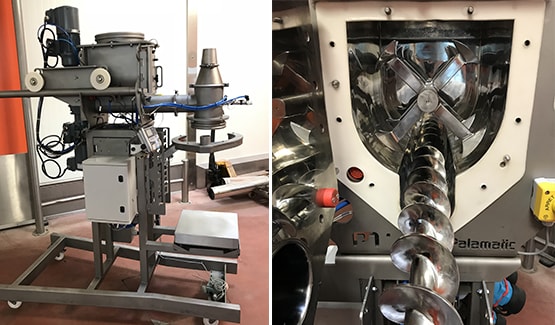
The washing cycles are controlled directly by PLC with operator validation phases to ensure the installation of any removable washing nozzles, as well as dewatering solutions used to reduce drying times.
The equipment was designed to facilitate the flow of the cleaning solutions and avoid retention. Access hatches enable operators to inspect the interior of the equipment and check the sanitation of the powder processing machines.
According to the recipes processed on the line, dry rinsing batches are carried out with salt to ensure a preliminary cleaning of the equipment.