Reactor loading line
The reactor loading line is designed to supply powder to your pressurized chemical reactors and in gas ATEX zones. Introducing your powders under nitrogen is necessary for optimal process safety.
The specific PALAMATIC design allows the lowest nitrogen consumption on the market.
- Loading in ATEX gas zone
- Reduced nitrogen consumption
- Remote maintenance
- The operator works outside the reactor zone
- Vacuum transfer
Loading chemical and pharmaceutical reactors is a sensitive step in production because of the risks involved. This process, when in a closed environment, presents high risks of explosion especially when the reactor is previously loaded with solvent. Palamatic Process has developed a turnkey process line dedicated to this application integrating all the constraints encountered when supplying reactors.
The Bulk-NitroFill® line allows production operators the ability to safely load their materials into a reactor remotely, therefore significantly reducing the risks involved.
Whether you use an open reactor, a bioreactor or a Grignard, the Bulk-NitroFill® is the solution for deconditioning your powders with pneumatic vacuum transfer and a nitrogen introduction lock.
Models
Type of packaging | Number of reactors | Cyclone filtration | Loading rate | Ingredient weighing | |
---|---|---|---|---|---|
Bulk-NitroFill® 1 | Bag and big bag | 1 | Integrated | 5 tons / hr | Yes optional |
Bulk-NitroFill® Multi | Bag and big bag | 2 to 10 | Deported | 5 tons / hr | Yes optional |
The deconditioning of your powders
A chemical reaction involves the use of several ingredients to ensure the transformation process. The PALAMATIC Duopal® combined sack and big bag unloading station offers the manufacturing operator the flexibility of cracking big bags (bulk volume ingredients) and sacks (minor ingredients) of powders or pre-weighed bags. The ergonomics are designed so the powder unloading rates are achieved. The loading of big bags on the handling station is generally carried out by electric hoist to offer autonomy to the operator. An empty packaging compactor is included to keep a clean and safe work area. Find out more about the Duopal® station and its options .
Pneumatic transfer
Whether you manufacture your product on one or more chemical reactors, the Bulk-NitroFill® solution can load all of your reactors from the same unloading point. The transfer cyclones are located on the reactor inlet flanges. When your manufacturing workshop integrates several reactors, the pneumatic conveyor solution consists of a common and remote filtration. Remote filtration pneumatic conveyors offer many advantages and provide an extremely efficient solution. Discover all the advantages of pneumatic transfer with remote filter.
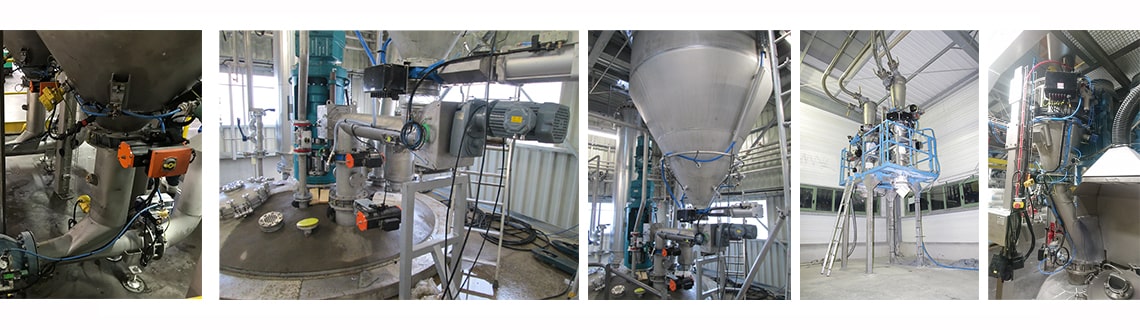
The introductory airlock
This reactor introduction hopper provides the nitrogen inertion of your powders and allows isolation of the reactor head with the pneumatic transfer line and outside atmosphere. This physical barrier, controlled by the Pal'Touch® automation system, represents the key indispensable equipment of the Bulk-NitroFill® solution. The use of this introduction hopper makes it possible to obtain very low nitrogen consumption compared to alternative transfer solutions. This is due to the fact that only the introduction hopper is connected to the nitrogen network, unlike other solutions where powder is transferred under nitrogen. Given the low consumption it is not necessary, as for pneumatic transfers under nitrogen, to have a recycling loop. The use of a nitrogen recycling system requires complex maintenance that the Bulk-NitroFill® solution does not require!
What loading rates?
The Bulk-NitroFill® solution allows you to load your reactors at a rate of up to 5 t / hr. For some products, the flow rate can increase up to 10 t / hr when using bulk bag and high flowability materials, such as sequins or resin beads.
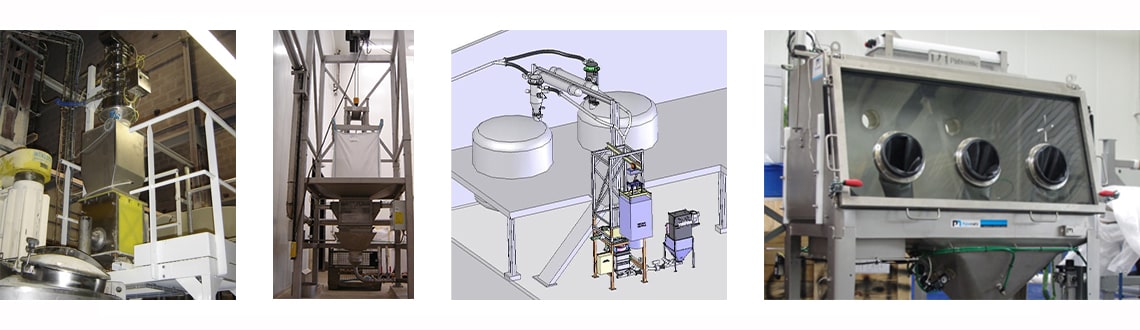
Automatic control
The powder loading solution is fully controlled by a complete automation system integrating the cycles necessary for correct operation and operational safety. To ensure manufacturing quality, product purging cycles are integrated and configurable according to your processed powders. For the safety of redundant sensors, residual oxygen thresholds are integrated into the control programs. For operator ergonomics, the powders to be introduced are displayed on the main control screen at the level of the bulk bag and sack emptying station. The quality and manufacturing department will use this computer tool to provide all the traceability of production batches: identification of operators, weighing control, loading times, flow rates, etc. Find out more about our management solutions.
What manufacturerers use Bulk-NitroFill® ?
Bulk-NitroFill® is the solution for manufacturers of resin, gel, powder coatings, printing inks, glues, hot melt capsules, etc. Basically, it is intended for all companies where the manufacture requires powders and a chemical reaction in an enclosure or reactor.
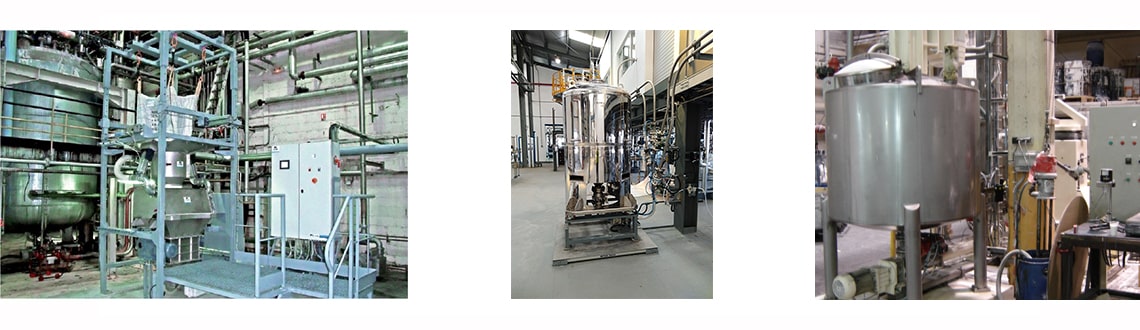
Our teams of experts are at your disposal to analyze your powders and set up the solution best suited to your needs and process constraints. Contact us!
Discover the installations of our customers using the Bulk-NitroFill® line for reactor loading.
All the equipment integrated into the chemical reactor loading process line is available below.