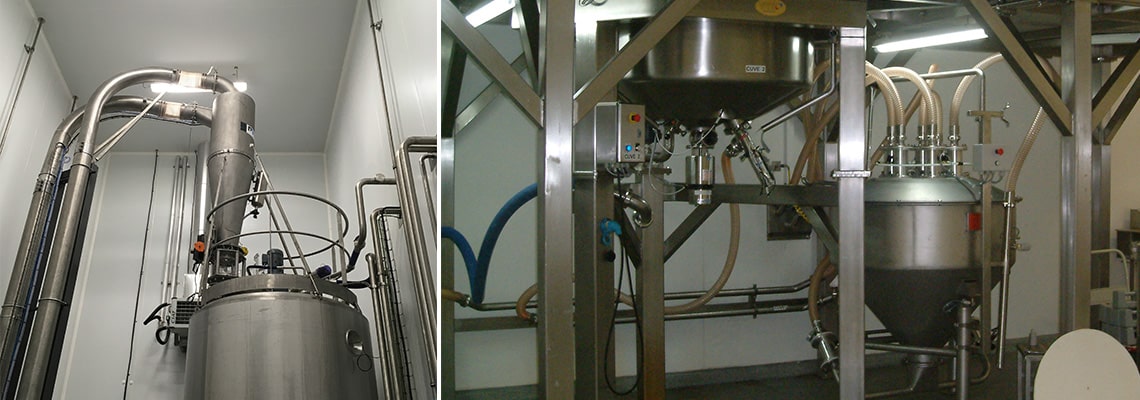
Pneumatic vacuum conveying, also known as vacuum transfer, transfers material from one or more feed points to the next stage of production in a plant with a suction cyclone and a closed pipe network.
1. What are the different types of vacuum conveyors?
Dilute Phase Vacuum Conveyors
This type of powder conveyor makes use of air flow at high speeds. High air velocity combined with low pressure is used to continuously fluidize the product. These vacuum conveyors are usually used for materials that do not pack when they are brought under pressure, such as grains, sugars, or plastic pellets. Dilute phase excels at long distance material conveying applications.
The high velocities impart a significant amount of force on this product. Therefore, one con to this type of system is that friable particles can experience attrition. However, vacuum dilute phase conveying can be helpful when conveying toxic materials because they minimize exposure to the substances. This is one of the reasons why they are preferred in agricultural, food processing, chemistry, and other industrial applications.
Dense Phase Vacuum Conveyors
Dense phase conveying is a type of transfer method that utilizes vacuum controlled at very low speeds. It is the opposite principle of dilute phase where instead of high velocity / low pressure, this powder transfer technology uses low velocity / high pressure. This will cause a “slugging” movement of product packets through the system. The main reasons for using dense phase are to either gently convey the bulk materials that may be friable, or, prevent wear and tear on the pipe network when dealing with abrasive materials. Therefore, the conveying of fragile materials is possible with pneumatic transfer systems.
Dense phase vacuum conveyors also offer an advantage in preventing too much buildup inside the pipes. Dense materials can be moved with this kind of high pressure. However, one drawback is that dense phase can be slower than dilute phase vacuum conveyors. Dense phase is still beneficial in processing abrasives such as salt and sugar, manufacturing plastics, transporting in bulk, and working with many fragile applications.
The system of dense vacuum conveying is mostly applicable for high-capacity materials. This is done from a range of short to long distances. This system can operate with a wide range of sources and reach many destinations. The low speeds provide the ideal conditions for dairy, pharmaceuticals, food, and other products that consist of both fragile and friable agglomerates.
The dense phase vacuum system has numerous advantages, which include its capability to efficiently contain food ingredients within the line. This is due to the vacuum’s inward pull effect.
Palamatic Process has a wide range of powder transfer system: VFlow® dense phase suction system, VF DEP remote filter conveyor, CYS® dilute phase cyclofilter, hygienic transfer cyclone as well as conveyors dedicated to certain powders such as cement (CementVeyor®) or ashes (MultiAshFlo®)
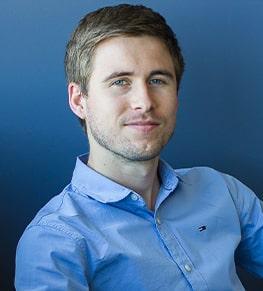
You want to implement a transfer system on
your line? I am at your disposal to discuss.
Guillaume De Clercq, powder expert
2. Advantages of using pneumatic vacuum transfer
Vacuum conveyors have a number of advantages over other mechanical conveying systems for bulk material transfers.
- Powders are transferred without the creation of excessive fines or dust because the material is conveyed gently when compared.
- They are reliable, easy to clean, and have a low cost of maintenance.
- The installation and control processes are simple and quick, as well as being preferred due to their hygienic design.
- In comparison to mechanical transfer systems, vacuum conveyors have very small footprints and are designed with high flexibility in mind.
- Vacuum conveyors are very adaptable for powders, tablets, pellets, pigments, granules, and capsules. In general, they are suitable for materials that are typically difficult to transport in bulk.
3. Common applications
Vacuum conveyors have many applications across various production industries. They are used in the chemical industry for their robustness and safety. They are also approved in the pharmaceutical industry due to their construction and hygienic design.
Because they are gentle, hygienic and low cost, they are also used in the food industry. Their applications are broad to the industry of bulk materials as modular and versatile.
Vacuum Conveyors in Food Packaging Operations
One challenge in the food packing industry is the transfer of powders and bulk material. The wrong process can affect production efficiency, product quality, and increase operator labor intensity. There is also a risk of material cross-contamination under such circumstances. Large amounts of dust, a pollutant and health hazard, can be created if the material is transferred without the use of proper powder conveying equipment.
Therefore, vacuum conveyors are best suited for fragile and crystal materials in the food packaging industry. These powder conveyors help increase production efficiency and quality, and reduce production costs.
Some of the advantages of using the vacuum conveyor include:
- Transfer of granules and powder without dust pollution. This is accomplished by the use of closed pipelines in the pneumatic conveying network. This results in a clean and safe work environment free of dust contamination.
- Vacuum conveyors navigate restrictive spaces with their minimal footprint.
- Vacuum conveyors can cover longer distances.
- Vacuum conveying systems reduces manual labor requirements for production floor operators.
To understand how a vacuum transfer system works, discover our dedicated article.