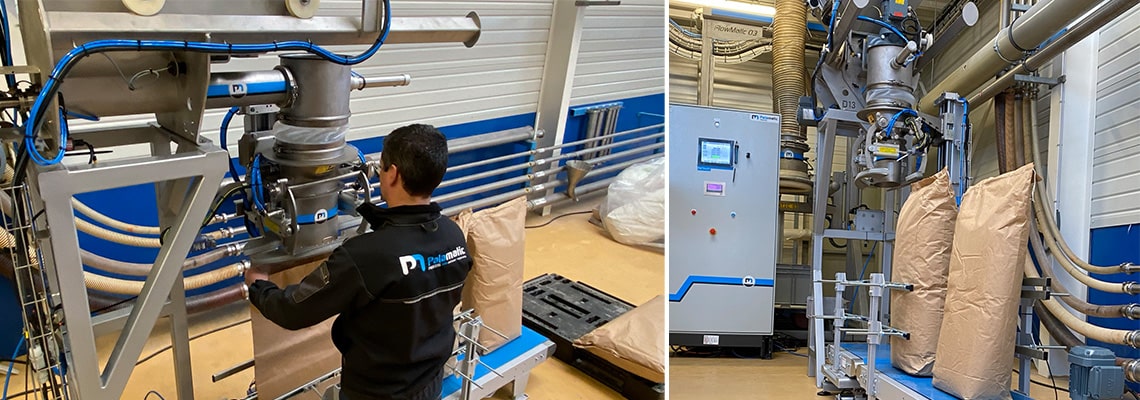
Many manufacturer’s production requirements involve both the large bulk quantities of major ingredients, as well as the addition of minor, or sometimes active ingredients. When it comes to delivery and feeding minor ingredients into your production system, 50 lbs sacks of powder is often the preferred packaging method. This means many suppliers need to adapt to varying client’s needs and deliver their materials in various packaging types. This includes bulk bags, sacks, buckets, drums, gaylords and IBCs. It can be difficult to determine what exactly your manufacturing requirements call for when it comes to choosing a semi-automatic or fully automatic bagging machine. Let’s further examine what the main differences are between these two types of filling machine, and what can help you determine which one is best for your industrial process.
1. Semi-automated bag packaging system
A semi-automatic bag filling station does exactly what is sounds like. Some functions need to be managed by a human operator, while other more critical functions our automated and handled by a local PLC. The main automated features on this type of system include batch weighing, feeding or dosing and filling the material into the bag. The control panel can still be programmed to record each packed bag for lot or batch traceability. The weighing typically functions based on loss-in-weight (LIW) or gain-in-weight operation. It is up to the operator to install the bag on the filling head, which typically either makes us of an inflatable seal or bag clamping device to secure the package and provide a dust tight seal. The operator then needs to remove the bag, seal it and place it on a pallet.
Equipment Advantages:
- Flexibility regarding packaging type and product runs
- Simple maintenance
- Easy installation
- Easy to operator with minimal training
- Low cost – quick ROI
- Easy to clean
Equipment Disadvantages (compared to fully automated):
- Physical requirements like lifting and carrying (although can be minimized with vacuum lifts)
- Need for manual labor by operator
- The rate can be limited by the efficiency of the operator
The good thing is this equipment is very versatile and can be used in nearly any industrial process that packages powders, granules and flakes in a 50 – 100 lbs. bag. However, they can be most beneficial for production processes where production output requirements are low, the planned budget is lean, manufacturing calls for small batch process with frequent recipe changes, plenty of labor resources in your local area, and the available space for installation is restrictive.
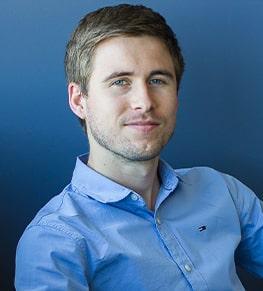
Looking for a bagging solution?
I am available to exchange.
Guillaume, powder expert
2. Fully-automated bag packaging system
Whether it is semi or fully automated, the goal of the system remains the same, to weigh and fill accurate amounts of dry materials in small bulk sacks. However, the major difference with a fully automated system is there is no need for operator intervention to manage the filling and packing cycles. The system will take the sack and load, open, fill, seal, convey and palletize it all based on the programmed PLC functions.
Because this type of system is trying to eliminate the need for labor inputs, the process and technology are much more sophisticated compared to the semi-automated version. These bag handling systems often times make use of robotic palletizing arms to load and pack the bags on a pallet for shipment to the customer.
Equipment Advantages:
- Total control of the positioning of the bag
- Clean and safe workspace
- Only labor required is general supervision of the system and re-supply the packaging materials.
- Maximized production
Equipment Disadvantages:
- Installation is complicated and should be handled by the supplier’s technician (commissioning)
- Larger footprint for installation
- Higher cost requires a more robust budget – longer ROI
Just like the semi-automated system, the fully automated version is adaptable to various industries handling dry bulk materials. Example industries include food & beverage, chemical, pharmaceutical, cosmetics, building materials, cement, etc. Automated bagging lines are most beneficial where production requirements involve high bags per hour output rates, scarce labor resources in the local area, manufacturing goals require an explicit ROI goal based on sustained productivity metrics.
Palamatic Process offers different semi-automatic and automatic bag filling solutions. Powered by different dosing technologies (screw doser, vibrating doser, double screw, Easy Clean doser), the bag fillers of our PalSack® range meet different production needs (high flow, soft handling, easy and hygienic cleaning...).
3. Key questions to ask yourself before making a purchasing decision
Making sure you invest in the right industrial equipment solution can be a daunting task. How can you be sure you are choosing the right technology for your end of the line packaging process? Here are a few suggested questions to help guide you in your buying process.
- Over the past few years, what has been your company’s experience in hiring the necessary labor (retention included) for keeping up with your daily production requirements?
- What is your planned budget for the project? What is your ROI goal?
- What is the available footprint for the planned installation area?
- What type of bags will be used (open-mouth, valve, etc.)?
- What is your hourly production goal (bags per hour)?
Contact one of our experts today for assistance with needed material handling solutions and to request a quote.